Metal vacuum composite insulation plate with getter and preparation method thereof
A technology of getter and heat insulation board, which is applied to heat exchange equipment, mechanical equipment, and pipelines through heat insulation protection. The effect of low puncture strength, reliable sealing and low cost
- Summary
- Abstract
- Description
- Claims
- Application Information
AI Technical Summary
Problems solved by technology
Method used
Image
Examples
Embodiment Construction
[0037]Referring to the accompanying drawings, the metal vacuum composite insulation panel with getter is composed of a shell 1, a core material 2 and a core plate 3, and the shell 1 is made of a stainless steel plate with a thickness of 0.15-1.5mm, a stainless iron plate, an electroplated tin plate, Zinc plate or aluminum alloy plate and other thin metal plates; Drying, plastic bag packaging, pre-vacuumizing and other treatments; the core plate 3 is a metal plate, glass plate, ceramic plate or high temperature resistant polymer plate, preferably a tempered glass plate of 3-5mm or an aluminum alloy plate of 1-2mm or The high temperature resistant plastic plate is directly placed in the vacuum chamber; the air exhaust port 4 is composed of an air exhaust nozzle and a metal cover directly punched out of the upper metal plate of the shell 1, and a low temperature solder 5 such as tin, zinc, magnesium and others is placed in the air exhaust nozzle. The low-melting-point alloy, the ...
PUM
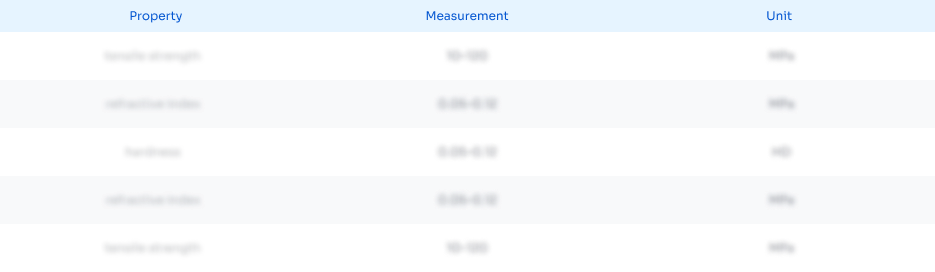
Abstract
Description
Claims
Application Information

- Generate Ideas
- Intellectual Property
- Life Sciences
- Materials
- Tech Scout
- Unparalleled Data Quality
- Higher Quality Content
- 60% Fewer Hallucinations
Browse by: Latest US Patents, China's latest patents, Technical Efficacy Thesaurus, Application Domain, Technology Topic, Popular Technical Reports.
© 2025 PatSnap. All rights reserved.Legal|Privacy policy|Modern Slavery Act Transparency Statement|Sitemap|About US| Contact US: help@patsnap.com