Die release agent and preparation method thereof
A technology of release agent and release powder, which is applied in the direction of manufacturing tools, casting molding equipment, metal processing equipment, etc., can solve the problems of ductility, film formation and poor adhesion, and achieve multiple demoulding times and high precision , the effect of long demoulding time
- Summary
- Abstract
- Description
- Claims
- Application Information
AI Technical Summary
Problems solved by technology
Method used
Image
Examples
preparation example Construction
[0050] In the present invention, based on the parts by weight of the release powder, the parts by weight of the graphene are 0.1 to 5 parts, preferably 0.5 to 4 parts, more preferably 1 to 3 parts , most preferably 2 parts. In the present invention, the particle size of the graphene is preferably 0.5 micron to 1.2 micron, more preferably 0.8 micron to 1 micron. In the present invention, the raw material for preparing graphene is preferably biomass carbon source. In the present invention, the preparation method of described graphene preferably comprises the following steps:
[0051] 1), under the action of a catalyst, the biomass carbon source is subjected to catalytic treatment to obtain a first intermediate product, and the catalyst includes one or more of manganese chloride salts, iron compounds, cobalt compounds and nickel compounds Several;
[0052] 2) In the presence of a protective gas, the first intermediate product is heated from a first temperature to a second temp...
Embodiment 1
[0099] At 90° C., hydrolyzing corncobs in sulfuric acid for 10 minutes to obtain lignocellulose, the mass of the sulfuric acid being 3% of the mass of the corncobs;
[0100] At 70°C, the lignocellulose was subjected to acidic sulfite treatment for 1 hour to obtain porous cellulose, the pH value in the acidic sulfite treatment process was 1, the acid was sulfuric acid, and sulfite It is magnesium sulfite, the quality of the sulfuric acid is 4% of the quality of the lignocellulose, and the liquid-solid ratio is 2:1.
[0101] The obtained porous cellulose is bleached with hydrogen peroxide, the mass of the hydrogen peroxide is 5% of the mass of the porous cellulose, the bleaching temperature of the hydrogen peroxide bleaching is 100° C., and the bleaching time is 5 hours.
[0102] Stir the porous cellulose and manganese chloride at 20°C for 2 hours for catalytic treatment, the mass ratio of the manganese chloride and porous cellulose is 0.01:1; Drying at a low temperature to obt...
Embodiment 2
[0106] At 180°C, hydrolyzing corncobs in nitric acid for 10 hours to obtain lignocellulose, the mass of the nitric acid being 20% of the mass of the corncobs;
[0107] At 180°C, the lignocellulose was subjected to acidic sulfite treatment for 6 hours to obtain porous cellulose, the pH value during the acidic sulfite treatment process was 7, the acid was sulfuric acid, and sulfite It is sodium sulfite, the quality of the sulfuric acid is 30% of the quality of the lignocellulose, and the liquid-solid ratio is 20:1.
[0108] The porous cellulose is bleached with hydrogen peroxide, the mass of the hydrogen peroxide is 5% of the mass of the porous cellulose, the bleaching temperature of the hydrogen peroxide bleach is 100° C., and the bleaching time is 5 hours.
[0109] Stir the porous cellulose and ferric nitrate at 180°C for 10 hours for catalytic treatment, the mass ratio of ferric nitrate and porous cellulose is 2:1; dry the obtained catalytically treated product at 120°C , ...
PUM
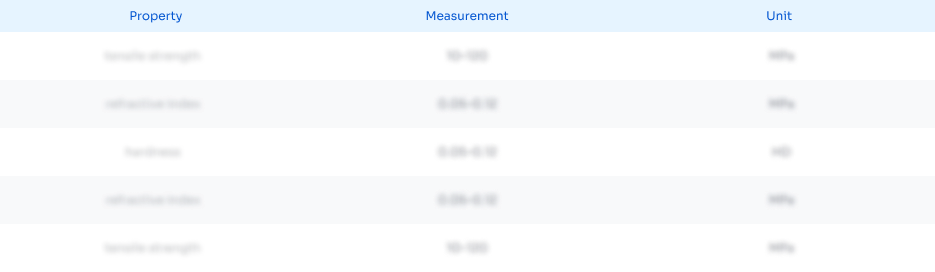
Abstract
Description
Claims
Application Information

- R&D
- Intellectual Property
- Life Sciences
- Materials
- Tech Scout
- Unparalleled Data Quality
- Higher Quality Content
- 60% Fewer Hallucinations
Browse by: Latest US Patents, China's latest patents, Technical Efficacy Thesaurus, Application Domain, Technology Topic, Popular Technical Reports.
© 2025 PatSnap. All rights reserved.Legal|Privacy policy|Modern Slavery Act Transparency Statement|Sitemap|About US| Contact US: help@patsnap.com