Pretreatment technology for indium and germanium extraction
A technology with a process and purpose, which is applied in the field of pretreatment technology for indium and germanium extraction, can solve the problems of high equipment temperature, operator poisoning and death, casualties, etc., and achieves safe and reliable operation, high recovery efficiency, and good safety effects.
- Summary
- Abstract
- Description
- Claims
- Application Information
AI Technical Summary
Problems solved by technology
Method used
Image
Examples
specific Embodiment approach
[0037] Below the present invention is described in further detail:
[0038] The present invention comprises the following steps:
[0039] 1. Melting, the material containing In and Ge is placed in the melting pool to be heated and melted into a liquid state; the heating temperature in the melting pool varies with the composition of the material containing In and Ge. In practice, by increasing the superheating temperature of the material, the liquid state can be made The surface tension and viscosity of the material are reduced at the same time, which is conducive to the formation of fine materials; at the same time, in order to prevent the material from being oxidized by germanium, it is best to be in a negative pressure state in the melting pool.
[0040] 2. Diversion, the molten liquid material is introduced into the atomization chamber through the conduit. In order to keep the temperature of the liquid material and reduce its surface tension and viscosity, it is best to con...
Embodiment 1
[0047] Weigh 1000g of In and Ge-containing material and place it in the melting pool and heat it to 1260°C to melt into a liquid state. The liquid material at a temperature of 1260°C is introduced into the atomization chamber through a conduit for atomization, and compressed nitrogen gas with a pressure of 1.2 MPa is introduced. A solid powder is obtained, and the powder is collected and recovered by sieving. The mesh numbers of the obtained samples are shown in Table 1. Chemical analysis of the sample shows In3.989% and Ge5.991%, and the loss rate is 0.275% and 0.1%. Compared with the traditional ball milling and Raymond milling methods, In and Ge loss of 2%, In and Ge loss less. Extracting In and Ge from the sample after acid leaching reduces the cost by about 2,000 yuan per ton of material compared with traditional ball milling and Raymond milling methods. , it is necessary to add an oxidizing agent to help it dissolve, and the cost is greatly increased.
[0048] Table 1...
Embodiment 2
[0051] Weigh 1000g of the material containing 4%In and 6%Ge, place it in the melting pool and heat it to 1260°C to melt into a liquid state, and the liquid material at a temperature of 1240°C is introduced into the atomization chamber through the catheter for atomization, and the inlet pressure is 1.4MPa The compressed nitrogen gas is used to obtain solid powder, and the powder is collected and recovered by sieving. The mesh numbers of the obtained samples are shown in Table 2. The chemical analysis of the sample shows that it contains 3.99% In, 5.992% Ge, and the loss rate is 0.25% and 0.133%, while the traditional ball milling and Raymond milling methods lose 2% of In and Ge. The cost of extracting In and Ge after acid leaching of atomized materials will be reduced.
[0052] Table 2 The mass and percentage of samples in different meshes
[0053]
PUM
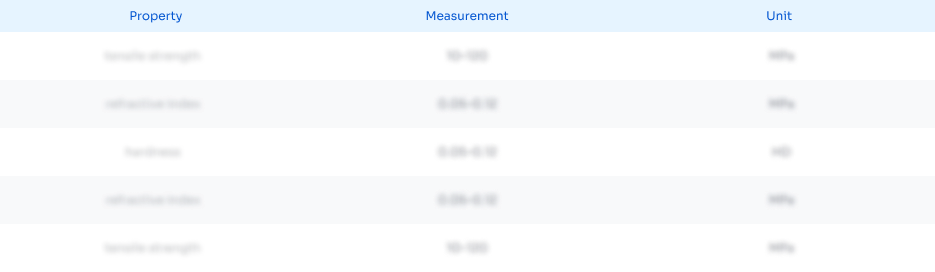
Abstract
Description
Claims
Application Information

- Generate Ideas
- Intellectual Property
- Life Sciences
- Materials
- Tech Scout
- Unparalleled Data Quality
- Higher Quality Content
- 60% Fewer Hallucinations
Browse by: Latest US Patents, China's latest patents, Technical Efficacy Thesaurus, Application Domain, Technology Topic, Popular Technical Reports.
© 2025 PatSnap. All rights reserved.Legal|Privacy policy|Modern Slavery Act Transparency Statement|Sitemap|About US| Contact US: help@patsnap.com