Manufacturing method for die-casting machine injection punch
A technology of injection punch and manufacturing method, which is applied in the field of parts for die casting, can solve the problems affecting the production efficiency and production cost of die casting machines, the service life of injection punches of die casting machines is low, and the manufacturing process is complicated, etc., to achieve improvement Stability and solid solution strengthening ability, improved service life and die casting production efficiency, and improved stability
- Summary
- Abstract
- Description
- Claims
- Application Information
AI Technical Summary
Problems solved by technology
Method used
Image
Examples
Embodiment 1
[0031] The first step, raw material configuration:
[0032] According to the weight percentage of raw material elements: 3.8% C, 2.6% Si, 0.8% Mn, 1.2% Cr, 0.2% Mo, 0.1% V, 0.06% P, 0.02% S and the rest are Fe, weigh the required amount of raw materials : pig iron, steel scrap, ferrosilicon, ferromanganese, ferrochrome, ferromolybdenum and ferrovanadium;
[0033] The second step, the smelting of raw materials:
[0034] Put the raw materials configured in the first step into an intermediate frequency induction furnace for smelting until all the raw materials are melted and the temperature of the molten iron is raised to 1500°C;
[0035] The third step, spheroidization treatment and inoculation treatment:
[0036] Weigh the rare earth magnesium ferrosilicon nodulizer which accounts for 1.2% by weight of the molten iron in the second step and the silicon-barium alloy inoculant which accounts for 0.8% by weight of the molten iron in the second step, and add them together to the ...
Embodiment 2
[0042] The first step, raw material configuration:
[0043] According to the weight percentage of raw material elements: 3.6% C, 2.7% Si, 1.0% Mn, 1.0% Cr, 0.3% Mo, 0.3% V, 0.05% P, 0.015% S and the rest are Fe, weigh the required amount of raw materials : pig iron, steel scrap, ferrosilicon, ferromanganese, ferrochrome, ferromolybdenum and ferrovanadium;
[0044] The second step, the smelting of raw materials:
[0045] Put the raw materials configured in the first step into an intermediate frequency induction furnace for melting until all the raw materials are melted and the temperature of the molten iron is raised to 1530°C;
[0046] The third step, spheroidization treatment and inoculation treatment:
[0047] Weigh the rare earth magnesium ferrosilicon nodulizer which accounts for 1.3% by weight of the molten iron in the second step and the silicon-barium alloy inoculant which accounts for 0.6% by weight of the molten iron in the second step, and add them together to the ...
Embodiment 3
[0053] The first step, raw material configuration:
[0054] According to the weight percentage of raw material elements: 3.5% C, 2.8% Si, 1.2% Mn, 0.7% Cr, 0.4% Mo, 0.2% V, 0.03% P, 0.01% S and the rest is Fe, weigh the required amount of raw materials : pig iron, steel scrap, ferrosilicon, ferromanganese, ferrochrome, ferromolybdenum and ferrovanadium;
[0055] The second step, the smelting of raw materials:
[0056] Put the raw materials prepared in the first step into an intermediate frequency induction furnace for smelting until all the raw materials are melted and the temperature of the molten iron is raised to 1550°C;
[0057] The third step, spheroidization treatment and inoculation treatment:
[0058] Weigh the rare earth magnesium ferrosilicon nodulizer which accounts for 1.6% by weight of the molten iron in the second step and the silicon-barium alloy inoculant which accounts for 0.4% by weight of the molten iron in the second step, and add them together to the sph...
PUM
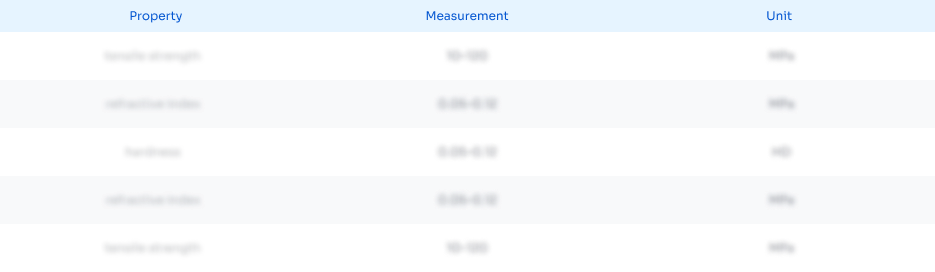
Abstract
Description
Claims
Application Information

- R&D Engineer
- R&D Manager
- IP Professional
- Industry Leading Data Capabilities
- Powerful AI technology
- Patent DNA Extraction
Browse by: Latest US Patents, China's latest patents, Technical Efficacy Thesaurus, Application Domain, Technology Topic, Popular Technical Reports.
© 2024 PatSnap. All rights reserved.Legal|Privacy policy|Modern Slavery Act Transparency Statement|Sitemap|About US| Contact US: help@patsnap.com