Inorganic anti-radiation coating for lining of radiation chamber of ethylene cracking furnace and preparation method of inorganic anti-radiation coating
An ethylene cracking furnace, inorganic coating technology, applied in the direction of reflection/signal coatings, coatings, sustainable manufacturing/processing, etc., can solve the problem that the application of ethylene cracking furnace is not successful, the use effect and service life are affected, and the energy utilization rate is low. and other problems, to achieve the effects of considerable social and economic benefits, excellent thermal shock resistance, and improved utilization.
- Summary
- Abstract
- Description
- Claims
- Application Information
AI Technical Summary
Problems solved by technology
Method used
Examples
Embodiment 1
[0024] Coating composition ratio:
[0025] 18 parts of cobalt oxide, 7 parts of zirconia, 9 parts of alumina, 2.5 parts of silicon powder, 10 parts of silicon carbide, 4 parts of chromium oxide, 3.5 parts of manganese oxide, 3 parts of corundum, 6 parts of sodium silicate, 7.5 parts of aluminum dihydrogen phosphate Parts, 3 parts of quartz powder, 3 parts of feldspar powder, 13 parts of phosphorus pentoxide, 3 parts of chromite, 1 part of zircon sand, 1 part of cerium oxide, 2 parts of graphite, 0.5 part of boron oxide, 0.2 part of clay, each The particle size of the solid component is not less than 350 mesh.
[0026] Preparation:
[0027] The ingredients are listed according to the above formula ratio, and the coating product is obtained through grinding, soaking, heating reaction, stirring, mixing, filtering and barreling.
[0028] After testing, the physical properties of the coating product are as follows:
[0029] Thermal shock stability: according to JB / T3648.1-1994 s...
Embodiment 2
[0034] Coating composition ratio:
[0035] 19 parts of cobalt oxide, 4 parts of zirconia, 5 parts of aluminum oxide, 3 parts of silicon powder, 12 parts of silicon carbide, 6 parts of chromium oxide, 4 parts of manganese oxide, 4 parts of corundum, 5 parts of sodium silicate, 5 parts of aluminum dihydrogen phosphate parts, 4 parts of quartz powder, 3 parts of feldspar powder, 16 parts of phosphorus pentoxide, 2 parts of chromite, 0.6 parts of zircon sand, 0.6 parts of cerium oxide, 3.5 parts of graphite, 0.7 parts of boron oxide, 0.3 parts of clay, each The particle size of the solid component is not less than 350 mesh.
[0036] The ingredients are listed according to the above formula ratio, and the coating product is obtained through grinding, soaking, heating reaction, stirring, mixing, filtering and barreling.
[0037] After testing, the physical properties of the coating product are as follows:
[0038] Thermal shock stability: According to the JB / T3648.1-1994 standard,...
PUM
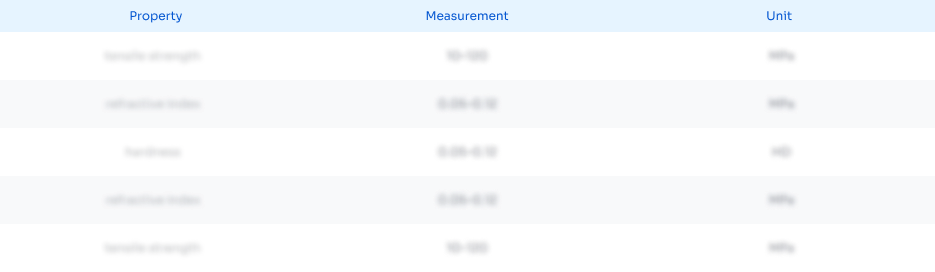
Abstract
Description
Claims
Application Information

- Generate Ideas
- Intellectual Property
- Life Sciences
- Materials
- Tech Scout
- Unparalleled Data Quality
- Higher Quality Content
- 60% Fewer Hallucinations
Browse by: Latest US Patents, China's latest patents, Technical Efficacy Thesaurus, Application Domain, Technology Topic, Popular Technical Reports.
© 2025 PatSnap. All rights reserved.Legal|Privacy policy|Modern Slavery Act Transparency Statement|Sitemap|About US| Contact US: help@patsnap.com