Method for producing nickel-iron particles by using coal-based reducing agent to directly reduce laterite nickel ore
A laterite nickel ore and direct technology, applied in the field of metallurgy and chemical industry, can solve the problems of uneven mixing of materials, difficulty in implementation, and low grade of ferronickel products, so as to improve the degree of mixing and combination, improve the reduction efficiency, and the recovery rate of ferronickel is high Effect
- Summary
- Abstract
- Description
- Claims
- Application Information
AI Technical Summary
Problems solved by technology
Method used
Image
Examples
Embodiment 1
[0031] (1) Raw ore: laterite nickel ore, its chemical composition: nickel 1.86%, iron 11.8%, magnesium oxide 24.7%, aluminum oxide 0.9%, silicon dioxide 42.5%, chromium oxide 1.0%;
[0032] (2) Process steps: Dry the laterite nickel raw ore, add 5.5% coal powder and 3% lime, mix and dry grind together to 200 mesh, accounting for 90%, press balls, the size of the pellets is 15mm, and the pellets are sent to preheat device, the preheating temperature is 350°C, and the time is 1.2h. After preheating, the pellets directly enter the rotary kiln for reduction and calcination. The temperature in the kiln is controlled at 1250-1300°C for 1 hour. The materials exiting the kiln are immediately water-quenched, crushed and ground to 2-3mm, and then enter the jig machine after screening to obtain Nickel-iron alloy grains. Under this process condition, the nickel-iron alloy contains 16.3% nickel, the recovery rate of nickel is 93.6%, and the recovery rate of iron is 91.8%.
Embodiment 2
[0034] (1) Raw ore: laterite nickel ore, its chemical composition: nickel 1.7%, iron 12.0%, magnesium oxide 25.2%, aluminum oxide 0.95%, silicon dioxide 43.2%, chromium oxide 0.8%;
[0035] (2) Process steps: Dry the laterite nickel raw ore, add 5% coal powder and 3.5% lime, mix and dry grind together to 200 mesh, accounting for 90%, press balls, the size of the pellets is 15mm, and the pellets are sent to preheat device, the preheating temperature is 370°C, and the time is 50 minutes. After preheating, the pellets directly enter the rotary kiln for reduction and calcination. The temperature in the kiln is controlled at 1300~1350°C for 1 hour. The materials exiting the kiln are immediately water-quenched, crushed and ground to 2~3mm, and then enter the jig machine after screening to obtain Nickel-iron alloy grains. Under this process condition, the nickel-iron alloy contains 15.7% nickel, the recovery rate of nickel is 95.4%, and the recovery rate of iron is 92.3%.
Embodiment 3
[0037] (1) Raw ore: laterite nickel ore, its chemical composition: nickel 1.86%, iron 11.8%, magnesium oxide 24.7%, aluminum oxide 0.9%, silicon dioxide 42.5%, chromium oxide 1.0%; by weight percentage
[0038] (2) Process steps: Dry the laterite nickel raw ore, add 5.5% coal powder and 3% lime, mix and dry grind together to 200 mesh, accounting for 90%, press balls, the size of the pellets is 15mm, and the pellets are sent to preheat The device is preheated at 400°C for 50 minutes. After preheating, the pellets directly enter the rotary kiln for reduction and calcination. The temperature in the kiln is controlled at 1300~1350°C for 1 hour. The materials exiting the kiln are immediately water-quenched, crushed and ground to 2~3mm, and then enter the jig machine after screening to obtain Nickel-iron alloy grains. Under this process condition, the nickel-iron alloy contains 16.0% nickel, the recovery rate of nickel is 93%, and the recovery rate of iron is 93%.
PUM
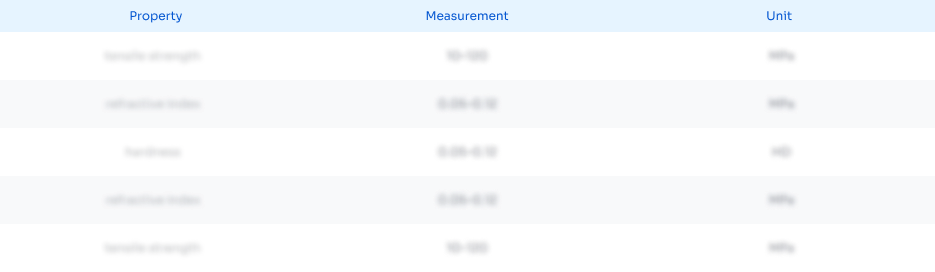
Abstract
Description
Claims
Application Information

- R&D
- Intellectual Property
- Life Sciences
- Materials
- Tech Scout
- Unparalleled Data Quality
- Higher Quality Content
- 60% Fewer Hallucinations
Browse by: Latest US Patents, China's latest patents, Technical Efficacy Thesaurus, Application Domain, Technology Topic, Popular Technical Reports.
© 2025 PatSnap. All rights reserved.Legal|Privacy policy|Modern Slavery Act Transparency Statement|Sitemap|About US| Contact US: help@patsnap.com