Powdered water-based polyurethane and preparation method thereof
A water-based polyurethane and powder technology, applied in the field of water-based polyurethane, can solve problems such as complex processes, and achieve the effects of simple equipment requirements, simple production process, and simple synthesis process.
- Summary
- Abstract
- Description
- Claims
- Application Information
AI Technical Summary
Problems solved by technology
Method used
Image
Examples
Embodiment 1
[0022] 14.8g (0.1mol) of dimethylolpropionic acid was dissolved in 50g of acetone, and 10.1g (0.1mol) of triethylamine was added for neutralization reaction. After 10min, the acetone was removed in vacuum to obtain an ionized hydrophilic chain extender , add 100g (0.1mol) molecular weight again and be the polyethylene glycol of 1000, 100g (0.05mol) molecular weight is the polyoxypropylene ether glycol of 2000, butanediol 10g (0.11mol), catalyst dibutyltin dilaurate 0.1 g, mixed evenly, vacuum dehydrated, added 80.2 g (0.36 mol) of isophorone diisocyanate (IPDI), heated at 60°C for 90 minutes, and crushed the solid to obtain water-based polyurethane powder.
[0023] Add the water-based polyurethane powder into tap water and stir to obtain the water-based polyurethane emulsion. Add 100 parts by mass of an emulsion with a solid content of 30% to 3 parts by mass of a water-based polyurethane curing agent to form an adhesive film. The properties are shown in Table 1.
Embodiment 2
[0025] Dissolve 14.8g of dimethylolpropionic acid in 50g of acetone, add 10.1g of triethylamine for neutralization reaction, after 10min, remove the acetone in vacuum to obtain an ionized hydrophilic chain extender, then add 100g (0.05mol) Molecular weight is the polyethylene glycol of 2000, and 100g molecular weight is the polyoxypropylene ether glycol of 2000, butanediol 10g, catalyst dibutyltin dilaurate 0.1g, mix homogeneously, vacuum dehydration, add toluene diisocyanate (TDI) 53.9 g (0.31mol), heated at 60°C for 90 minutes, and pulverized the solid to obtain water-based polyurethane powder.
[0026] The obtained powder is added into tap water and stirred to obtain a water-based polyurethane emulsion. Add 100 parts by mass of an emulsion with a solid content of 30% to 3 parts by mass of a water-based polyurethane curing agent to form an adhesive film. The properties are shown in Table 1.
Embodiment 3
[0028] 7.4g (0.05mol) of dimethylolbutyric acid was dissolved in 50g of acetone, and 5.05g (0.05mol) of triethylamine was added for neutralization reaction. After 10min, the acetone was removed in vacuum to obtain an ionized hydrophilic chain extender , add 100g molecular weight again and be the polyethylene glycol of 1000, 100g molecular weight is the polyoxypropylene ether glycol of 2000, catalyst dibutyltin dilaurate 0.1g, mix homogeneously, vacuum dehydration, add isophorone diisocyanate (IPDI ) 44.4g (0.20mol), heated at 60°C for 90min, and pulverized the solid to obtain water-based polyurethane powder.
[0029] Add the water-based polyurethane powder into tap water and stir to obtain the water-based polyurethane emulsion. Add 100 parts by mass of an emulsion with a solid content of 30% to 3 parts by mass of a water-based polyurethane curing agent to form an adhesive film. The properties are shown in Table 1.
PUM
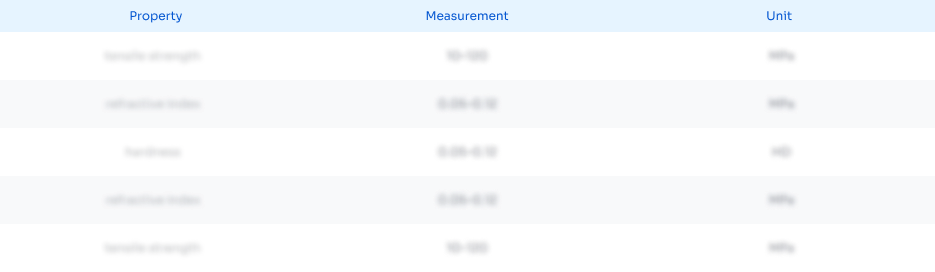
Abstract
Description
Claims
Application Information

- R&D Engineer
- R&D Manager
- IP Professional
- Industry Leading Data Capabilities
- Powerful AI technology
- Patent DNA Extraction
Browse by: Latest US Patents, China's latest patents, Technical Efficacy Thesaurus, Application Domain, Technology Topic, Popular Technical Reports.
© 2024 PatSnap. All rights reserved.Legal|Privacy policy|Modern Slavery Act Transparency Statement|Sitemap|About US| Contact US: help@patsnap.com