Drag reducer and preparation method thereof
A technology of drag reducer and release agent, which is applied in mechanical equipment, gas/liquid distribution and storage, pipeline system, etc. It can solve the problems of high viscosity of the system, cumbersome operation process, high reaction heat, etc., so as to slow down the agglomeration, The effect of simplifying the production process and slowing down the rise of polymer particles
- Summary
- Abstract
- Description
- Claims
- Application Information
AI Technical Summary
Problems solved by technology
Method used
Image
Examples
Embodiment 1
[0038] This example is used to illustrate the stabilizing effect of surfactants on the suspension system.
[0039] In the embodiment, agent 1 is Tween 40; agent 2 is Span 60; agent 3 is octylphenol polyoxyethylene ether (4); agent 4 is isooctylphenol polyoxyethylene ether (7); agent 5 is Disodium fatty alcohol polyoxyethylene ether sulfosuccinate; agent 6 is cocamidopropyl betaine; agent 7 is sodium α-alkenyl sulfonate (18); agent 8 is nonylphenol ethoxylate phosphate ; Agent 9 is sodium petroleum sulfonate.
[0040] Take 0.8g of calcium stearate powder (with a particle size of 80 mesh to 100 mesh), add it to 20g of simethicone oil (300cst), add 0.4g of surfactant, stir evenly with a glass rod, pour it into a test tube and let it stand for observation . At the same time, the blank test without adding surfactant was used, and the test results are shown in Table 1. As can be seen from Table 1, adding surfactants can greatly delay the sedimentation of calcium stearate in silic...
Embodiment 2
[0044] This example is used to illustrate the stabilizing effect of the surfactant on the drag reducer suspension system.
[0045] In the embodiment, agent 1 is sodium petroleum sulfonate; agent 2 is cocamidopropyl betaine; agent 3 is sodium α-alkenyl sulfonate (18).
[0046] Take 10 g of the bulk polymerized rubbery drag reducer polymer, mix it with 5 g of calcium stearate, and grind it into powder with a low-temperature pulverizer. Take 1g of the pulverized powder, add it to 20g of simethicone oil (300cst) containing 0.4g of surfactant, stir it evenly and let it stand for observation. Simultaneously, the test without surfactant was used as a blank test, and the test results are shown in Table 2. It can be seen from Table 2 that adding a surfactant can greatly reduce the precipitation rate within a specified time and enhance the stability of the system. Among them, the effect of sodium petroleum sulfonate is better.
[0047] Table 2 Stability comparison of drag reducer sus...
Embodiment 3
[0050] This example is used to illustrate the preparation method of polyalphaolefin / simethicone oil slurry.
[0051] The polymerization catalyst used is prepared according to the following method: add 2.0 grams of ethoxymagnesium particle carrier (particle diameter is 40-50 microns), toluene 30ml into the reaction bottle and disperse evenly, lower the temperature to -10°C, add 10ml (6.0mol )TiCl 4 , stay for 0..5 hours, heat up to 80°C, add 0.6ml (0.39mol) diisobutyl phthalate, heat up to 110°C, react for 2 hours, settle, filter, wash with toluene twice (20ml each time) , secondary loading titanium, add 5ml (3.0mmol) TiCl 4 React with 30ml of toluene for 1 hour, settle, filter, wash with hexane four times, and dry at 72°C to obtain a catalyst solid component. The mass percent content of titanium in the catalyst is 2.87%.
[0052] Mix 35g of 1-octene refined by molecular sieves (purchased from ACROS Reagent Company) with 65g of dimethicone oil refined by molecular sieves (pu...
PUM
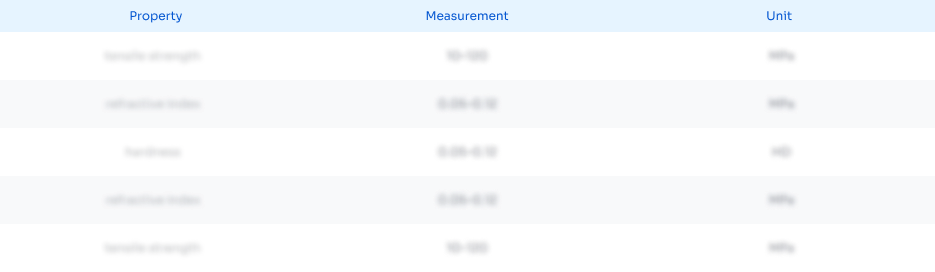
Abstract
Description
Claims
Application Information

- R&D Engineer
- R&D Manager
- IP Professional
- Industry Leading Data Capabilities
- Powerful AI technology
- Patent DNA Extraction
Browse by: Latest US Patents, China's latest patents, Technical Efficacy Thesaurus, Application Domain, Technology Topic, Popular Technical Reports.
© 2024 PatSnap. All rights reserved.Legal|Privacy policy|Modern Slavery Act Transparency Statement|Sitemap|About US| Contact US: help@patsnap.com