Low acid consumption anti-corrosion hot-replacing-cold product production method
A production method and corrosion-resistant technology, applied in workpiece surface treatment equipment, metal rolling, manufacturing tools, etc., can solve the problems of deteriorating product performance, increasing energy consumption and brightness in the production process, and improving the shape and thickness accuracy, Eliminate the effects of Ludes band defects and low surface residues
- Summary
- Abstract
- Description
- Claims
- Application Information
AI Technical Summary
Problems solved by technology
Method used
Image
Examples
Embodiment Construction
[0036] The specific embodiments of the present invention will be further described in detail below in conjunction with the accompanying drawings.
[0037] Such as Figure 4 and Figure 5 As shown, in order to achieve the above object, the technical solution of the present invention is realized in the following way: a method for producing products with low acid consumption and corrosion resistance, replacing heat with heat, specifically includes the following steps:
[0038] A. Uncoiler 1 uncoils;
[0039] B. The tempering machine 11 crushes and peels off the oxide 8 on the surface of the steel strip 7;
[0040] C. multi-roll leveler 12 further breaks and peels off the oxides on the surface of strip steel 7;
[0041]D. the scrubbing roller 16 in the scrubbing device 15 removes the oxide 8 that comes off and loosens on the strip surface;
[0042] E. Pickling 4 and rinsing 30 the strip steel 7 after smoothing, straightening and scrubbing;
[0043] F. Entering the strip steel...
PUM
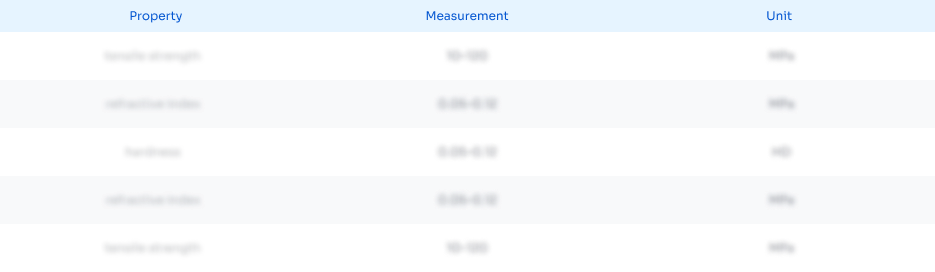
Abstract
Description
Claims
Application Information

- Generate Ideas
- Intellectual Property
- Life Sciences
- Materials
- Tech Scout
- Unparalleled Data Quality
- Higher Quality Content
- 60% Fewer Hallucinations
Browse by: Latest US Patents, China's latest patents, Technical Efficacy Thesaurus, Application Domain, Technology Topic, Popular Technical Reports.
© 2025 PatSnap. All rights reserved.Legal|Privacy policy|Modern Slavery Act Transparency Statement|Sitemap|About US| Contact US: help@patsnap.com