Coking-resistant hydrocarbon cracking furnace pipe and preparation method thereof
A technology of hydrocarbon cracking furnace tube and cracking furnace tube, which is applied in the field of hydrocarbon cracking furnace tube and its preparation, can solve the problems of reducing the stability of manganese-chromium spinel, and weakening the ability of anti-coking and anti-carburization, etc., to achieve The effect of small particles, good stability and strong binding force
- Summary
- Abstract
- Description
- Claims
- Application Information
AI Technical Summary
Problems solved by technology
Method used
Image
Examples
Embodiment 1
[0038] A new furnace tube with the same size and material as that of Comparative Example 1 was adopted, and the coating was prepared according to the method of the present invention for the furnace tube. The furnace tube is first heated at 99.97%H on the device described in Comparative Example 1 2 -0.03%H 2 O(H 2 with H 2 The molar ratio of O is 3332:1) in an atmosphere of 1000°C for 20 hours, and then in 50%Ar-49.7%H 2 -0.3%H 2 O(H 2 with H 2 The molar ratio of O is 166:1) in the atmosphere at 1000°C for 10 hours. After cooling, the composition of the inner surface of the furnace tube was analyzed by X-ray energy dispersive spectrometer (EDS). The results are shown in Table 2.
[0039] Using the cracking conditions of Comparative Example 1, the furnace tube was subjected to 5 cycles of cracking and charring tests, and the coking amounts of different cracking times are shown in Table 3.
[0040] Table 2
[0041]
[0042] table 3
[0043]
[0044] From Table 2, w...
Embodiment 2
[0051] The material of the furnace tube in Example 1 was changed to HP40, and other conditions remained unchanged.
[0052] Table 4
[0053]
[0054] table 5
[0055]
[0056] From Table 4, we can find that the content of Cr and Mn elements on the surface of the furnace tube of Example 2 increases, while the elements of Fe and Ni with catalytic coking activity are greatly reduced. Compared with Comparative Example 2 (US6436202), the Cr content is low and Mn The content is high, which makes it easier for manganese-chromium spinel to maintain its spinel structure, and the stability is better.
[0057] From Table 5, we can find that the amount of coking in the 5th pyrolysis in Comparative Example 3 (blank value) is about 1.5 grams; the amount of coking in the first time in Comparative Example 4 (US6436202) is very low, which is reduced by more than 90% compared with the blank value , but with the increase of cracking and burning times, the amount of coking gradually incre...
PUM
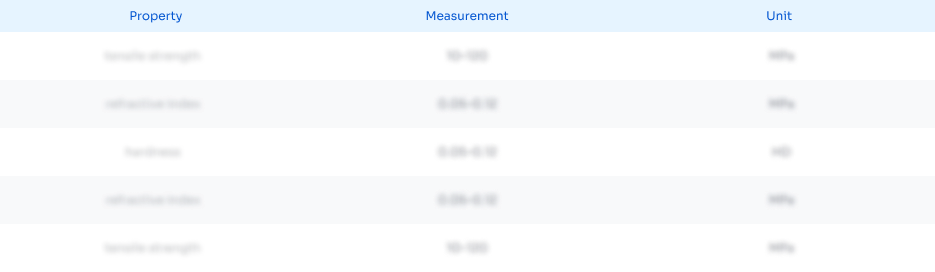
Abstract
Description
Claims
Application Information

- Generate Ideas
- Intellectual Property
- Life Sciences
- Materials
- Tech Scout
- Unparalleled Data Quality
- Higher Quality Content
- 60% Fewer Hallucinations
Browse by: Latest US Patents, China's latest patents, Technical Efficacy Thesaurus, Application Domain, Technology Topic, Popular Technical Reports.
© 2025 PatSnap. All rights reserved.Legal|Privacy policy|Modern Slavery Act Transparency Statement|Sitemap|About US| Contact US: help@patsnap.com