Preparation method of high-purity superfine spherical cobalt carbonate
A cobalt carbonate and spherical technology, which is applied in the field of preparation of high-purity ultrafine spherical cobalt carbonate, can solve problems such as difficulty in producing ultrafine spherical cobalt carbonate, uneven distribution of product particles, increased particle and particle agglomeration, etc., to avoid local concentration Too high, the production method is simple and easy to control, and the effect of reducing the dosage
- Summary
- Abstract
- Description
- Claims
- Application Information
AI Technical Summary
Problems solved by technology
Method used
Image
Examples
Embodiment 1
[0037] (1) Take 100g of high-purity cobalt metal sheet as a raw material, dissolve and purify it with nitric acid, then extract and remove impurities with p204 and p507 solutions to obtain a cobalt nitrate solution with a concentration of 100g / L; add 10g of ammonia water to the above cobalt nitrate solution The complexing agent is stirred and fully mixed to obtain a complexed cobalt salt solution; the pH value of the above-mentioned complexed cobalt salt solution is adjusted to 4.0 with nitric acid solution;
[0038] (2) Take 50g of ammonium carbonate and 50g of urea. Prepare a precipitant solution with a concentration of 100g / L; add 0.05g of dispersant PVP to the above precipitant solution, dissolve and stir evenly;
[0039] (3) Take 0.5L of the above-mentioned complexed cobalt salt solution and 0.75L of the precipitating agent solution, and add them to the reactor by the co-current feeding method according to the volume ratio of 1:1.5. 7.9, the stirring speed is 120rpm;
...
Embodiment 2
[0042] (1) Take 100g of high-purity cobalt metal sheet as raw material, dissolve and purify it with hydrochloric acid, then extract and remove impurities with p204 and p507 solutions to obtain a cobalt chloride solution with a concentration of 150g / L; add 0.5g complexing agent citric acid is prepared complexed cobalt salt solution, stirs and fully mixes, and the pH value of complexed cobalt salt solution is adjusted to 2.0 with hydrochloric acid;
[0043] (2) Take 150g of ammonium bicarbonate and 50g of urea to prepare a precipitant solution with a concentration of 200g / L;
[0044] Add 20g of dispersant ethanol to the above precipitant solution, dissolve and stir evenly;
[0045] (3) Take 0.1L of the above-mentioned complexed cobalt salt solution and 0.35L of the precipitating agent solution, and add them to the reactor with the co-current feeding method according to the volume ratio of 1:3.5, and control the synthesis reaction temperature to 50°C, and the reaction pH to be 8....
Embodiment 3
[0048] (1) Take 100g of high-purity cobalt metal sheet as a raw material, dissolve and purify it with nitric acid, then extract and remove impurities with p204 and p507 solutions to obtain a cobalt nitrate solution with a concentration of 60g / L; add 2.5g of cobalt nitrate to the above cobalt nitrate solution Polyacrylamide complexing agent and 2.5g ethylenediamine complexing agent, generate complexed cobalt salt solution, stir and fully mix; Regulate complexed cobalt salt solution pH value 2.0 with hydrochloric acid;
[0049] (2) Take 50g of ammonium bicarbonate and 50g of urea to prepare a precipitant solution with a concentration of 100g / L;
[0050] Add 0.1g dispersant PAA, 0.1g dispersant butanol and 0.1g dispersant acetone to the precipitant solution, stir and mix evenly;
[0051] (3) Take 0.1L of the above-mentioned complexed cobalt salt solution and 0.5L of the precipitating agent solution, and add them to the reactor by the co-current feeding method according to the volum...
PUM
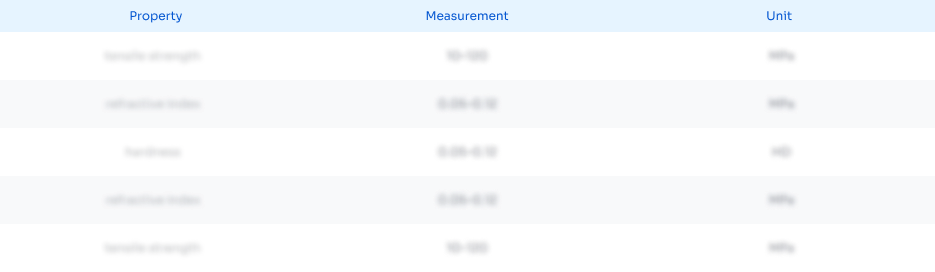
Abstract
Description
Claims
Application Information

- Generate Ideas
- Intellectual Property
- Life Sciences
- Materials
- Tech Scout
- Unparalleled Data Quality
- Higher Quality Content
- 60% Fewer Hallucinations
Browse by: Latest US Patents, China's latest patents, Technical Efficacy Thesaurus, Application Domain, Technology Topic, Popular Technical Reports.
© 2025 PatSnap. All rights reserved.Legal|Privacy policy|Modern Slavery Act Transparency Statement|Sitemap|About US| Contact US: help@patsnap.com