Carbon solid acid and aluminic acid ester doped ferric fluoride anode material with titanium-phosphate-lithium three-component surface modification, and preparation method of anode material
A technology of acid aluminate and lithium titanium phosphate, applied in battery electrodes, electrochemical generators, electrical components, etc., can solve the problems of high reaction activation energy, high conversion reaction, high voltage difference, etc., to improve ion conductivity and electronic conductivity, strong activity, and the effect of improving electrochemical performance
- Summary
- Abstract
- Description
- Claims
- Application Information
AI Technical Summary
Problems solved by technology
Method used
Image
Examples
Embodiment 1
[0019] Embodiment 1: Al 2 o 3 : SiO 2 : TiO 2 : NH 4 h 2 PO 4 : Li 2 CO 3 Mix evenly at a ratio of 0.05:0.2:1.9:2.8:0.65 (molar ratio), add 3.5% of 95% ethanol, and ball mill in a ball mill at a speed of 110 rpm for 12 hours. After ball milling, the pressure is 15Pa at 65°C Dry in a vacuum oven for 2.5 hours, take it out and re-grind it in an agate mortar for 15 minutes. The ground powder is heated to 650°C at a rate of 6°C / min and kept for 6 hours to make Li 1.3 Al 0.1 Ti 1.9 Si 0.2 P 2.8 o 12 Solid electrolyte powder. Place 5g of glucose in an oven at 90°C to dry for 5 hours, then carbonize at a constant temperature of 700°C in a muffle furnace for 6 hours, place it in a crucible after cooling, add 12mL of concentrated sulfuric acid and sulfonate it in an oven at 150°C for 1 hour to obtain carbon solid acid; the Fe(NO 3 ) 3 9H 2 O and ammonium fluoride (1.0:3.1 molar ratio) with 3.2% by weight Li 1.3 Al 0.1 Ti 1.9 Si 0.2 P 2.8 o 12 Solid electrolyte po...
Embodiment 2
[0020] Embodiment 2: Al 2 o 3 : SiO 2 : TiO 2 : NH 4 h 2 PO 4 : Li 2 CO 3 Mix evenly at a ratio of 0.05:0.2:1.9:2.8:0.65 (molar ratio), add 8% of 95% ethanol, and ball mill in a ball mill at a speed of 450 rpm for 45 hours. After ball milling, the pressure is 80Pa at 75°C Dry it in a vacuum oven for 8 hours, take it out and re-grind it in an agate mortar for 25 minutes, and heat the ground powder to 900°C at a rate of 25°C / min for 15 hours to make Li 1.3 Al 0.1 Ti 1.9 Si 0.2 P 2.8 o 12 Solid electrolyte powder. Place 20g of glucose in an oven at 120°C to dry for 10 hours, then carbonize at a constant temperature of 900°C in a muffle furnace for 10 hours, place it in a crucible after cooling, add 15mL of concentrated sulfuric acid, and sulfonate it in an oven at 190°C for 5 hours to obtain carbon Solid acid; FeCl 3 ·6H 2 O and ammonium fluoride (1.0:3.6 molar ratio) with 13% by weight Li 1.3 Al 0.1 Ti 1.9 Si 0.2 P 2.8 o 12 Solid electrolyte powder, 15% by ...
Embodiment 3
[0021] Embodiment 3: Al 2 o 3 : SiO 2 : TiO 2 : NH 4 h 2 PO 4 : Li 2 CO 3 Mix evenly at a ratio of 0.05:0.2:1.9:2.8:0.65 (molar ratio), add 5% of 95% ethanol, and ball mill in a ball mill at a speed of 200 rpm for 25 hours. After ball milling, the pressure is 60Pa at 70°C Dry it in a vacuum oven for 7 hours, take it out and re-grind it in an agate mortar for 20 minutes. The ground powder is heated to 750°C at a rate of 20°C / min and kept for 12 hours to make Li 1.3 Al 0.1 Ti 1.9 Si 0.2 P 2.8 o 12 Solid electrolyte powder. Place 10g of glucose in an oven at 100°C to dry for 7 hours, then carbonize at a constant temperature of 800°C in a muffle furnace for 7 hours, place it in a crucible after cooling, add 12mL of concentrated sulfuric acid, and sulfonate it in an oven at 170°C for 3 hours to obtain carbon solid acid; the Fe 2 (SO 4 ) 3 9H 2 O and ammonium fluoride (molar ratio 1.0:3.5) with 7% by weight Li 1.3 Al 0.1 Ti 1.9 Si 0.2 P 2.8 o 12 Solid electro...
PUM
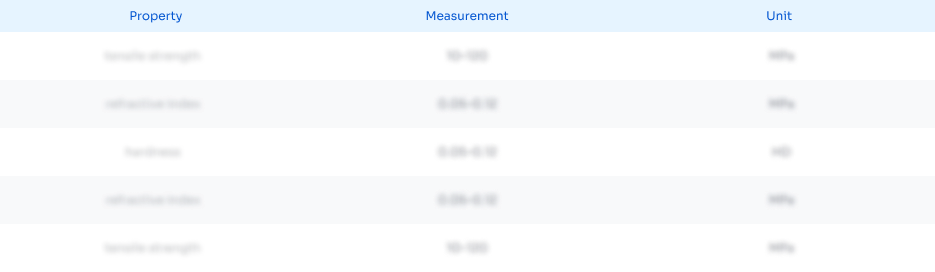
Abstract
Description
Claims
Application Information

- R&D
- Intellectual Property
- Life Sciences
- Materials
- Tech Scout
- Unparalleled Data Quality
- Higher Quality Content
- 60% Fewer Hallucinations
Browse by: Latest US Patents, China's latest patents, Technical Efficacy Thesaurus, Application Domain, Technology Topic, Popular Technical Reports.
© 2025 PatSnap. All rights reserved.Legal|Privacy policy|Modern Slavery Act Transparency Statement|Sitemap|About US| Contact US: help@patsnap.com