Carpentry cutter body manufacturing process
A manufacturing process and tool body technology, applied in the field of woodworking tool body manufacturing process, can solve the problems of processing efficiency and surface finish limitations, high manufacturing cost, high material cost, saving machine tool equipment and processing time, and saving metal raw materials , the effect of high dimensional accuracy
- Summary
- Abstract
- Description
- Claims
- Application Information
AI Technical Summary
Problems solved by technology
Method used
Image
Examples
Embodiment Construction
[0058] The specific embodiments of the present invention will be described in further detail below in conjunction with the accompanying drawings.
[0059] The invention provides a manufacturing process for a woodworking tool cutter body, the process comprising the following steps:
[0060] S01: Press the wax model of the knife body;
[0061] Take out the wax cylinder from the heat preservation tank, install the wax cylinder on the double-station hydraulic wax mold injection machine, remove the air and hard wax in the wax cylinder before pressing; The hydraulic wax mold injection machine is positioned, the wax mold of the knife body is aligned with the wax injection nozzle of the double station hydraulic wax mold injection machine, and the core of the wax mold of the knife body is in the center of the wax mold of the knife body ;
[0062] Before the double-station hydraulic wax mold injection machine works, a layer of parting agent is sprayed inside the wax mold of the cutter...
PUM
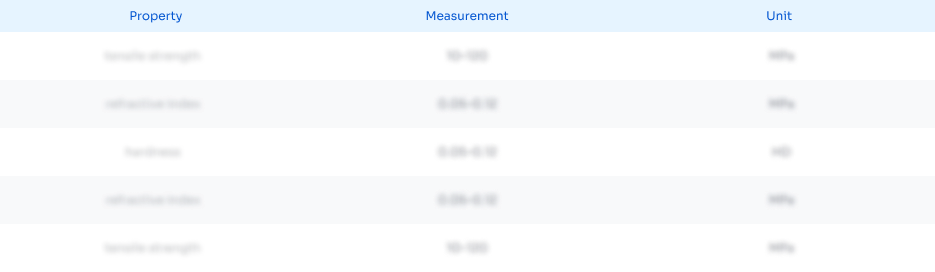
Abstract
Description
Claims
Application Information

- Generate Ideas
- Intellectual Property
- Life Sciences
- Materials
- Tech Scout
- Unparalleled Data Quality
- Higher Quality Content
- 60% Fewer Hallucinations
Browse by: Latest US Patents, China's latest patents, Technical Efficacy Thesaurus, Application Domain, Technology Topic, Popular Technical Reports.
© 2025 PatSnap. All rights reserved.Legal|Privacy policy|Modern Slavery Act Transparency Statement|Sitemap|About US| Contact US: help@patsnap.com