Continuous carbon nanotube-titanium dioxide composite membrane/fiber for electrode material
A technology of titanium dioxide and carbon nanotubes, applied in battery electrodes, hybrid capacitor electrodes, circuits, etc., can solve the problems of poor mechanical properties of carbon nanotube films, low yield of composite films, many uncontrollable factors, etc., and achieve electrochemical performance Excellent, high yield and highly controllable parameters
- Summary
- Abstract
- Description
- Claims
- Application Information
AI Technical Summary
Problems solved by technology
Method used
Image
Examples
Embodiment 1
[0029] (1) Dosing according to the mass percentage of raw materials: carbon source (ethanol) 80.05%, titanium dioxide precursor (butyl titanate) 17.78%, catalyst (ferrocene) 1.44%, accelerator (thiophene) 0.73%;
[0030] (2) Put the raw materials in step (1) into ultrasonic dispersion for 30 minutes to form a uniform reaction solution;
[0031] (3) The raw material obtained in step (2) was injected into a vertical resistance furnace heated to 1100°C at a rate of 6ml / h, and a continuous carbon nanotube-titanium dioxide composite film was formed under the action of a hydrogen flow with a flow rate of 800sccm, mechanically continuous spinning;
[0032] (4) The composite film obtained in step (3) was dried at 80°C for 12 hours, and then compacted with a pressure of 3 MPa to obtain an electrode sheet.
[0033] figure 1 It is the cycle-capacity curve diagram of the carbon nanotube-titanium dioxide composite film product prepared in Example 1, and the cycle performance curve of dis...
Embodiment 2
[0036] (1) Dosing according to the mass percentage of raw materials: carbon source (ethanol) 80.05%, titanium dioxide precursor (titanium isopropoxide) 17.78%, catalyst (ferrocene) 1.44%, accelerator (thiophene) 0.73%;
[0037] (2) Put the raw materials in step (1) into ultrasonic dispersion for 30 minutes to prepare a uniform reaction solution;
[0038] (3) The raw material obtained in step (2) is injected into a vertical resistance furnace heated to 1100°C at a rate of 6ml / h, and a continuous carbon nanotube / titanium dioxide composite film is formed under the action of a hydrogen flow with a flow rate of 800 sccm and undergoes water densification The action forms continuous fibers, which are continuously spun mechanically;
[0039] (4) Dry the composite fiber obtained in step (3) at 80°C for 12 hours, cut it into short sections with a length of 10mm, lay it flat into a rectangle of 10mm×10mm, with a thickness of about 1mm, and compact it on the stainless steel with a pressur...
Embodiment 3
[0042] (1) Dosing according to the mass percentage of raw materials: carbon source (ethanol + acetone) 80.05%, titanium dioxide precursor (titanium isopropoxide) 17.78%, catalyst (ferrocene) 1.44%, accelerator (thiophene) 0.73%;
[0043] (2) Put the raw materials in step (1) into ultrasonic dispersion for 30 minutes to form a uniform reaction solution;
[0044] (3) Inject the raw materials obtained in step (2) into a vertical resistance furnace heated to 1100°C at a rate of 6ml / h, and form a continuous carbon nanotube-titanium dioxide composite film under the action of a hydrogen flow with a flow rate of 800 sccm to be mechanically continuous spin out;
[0045] (4) After drying the composite film obtained in step (3) at 80°C for 12h, heat treatment at 400°C for 0.5h to remove amorphous carbon impurities, and then compact it with a pressure of 3MPa to obtain an electrode sheet.
PUM
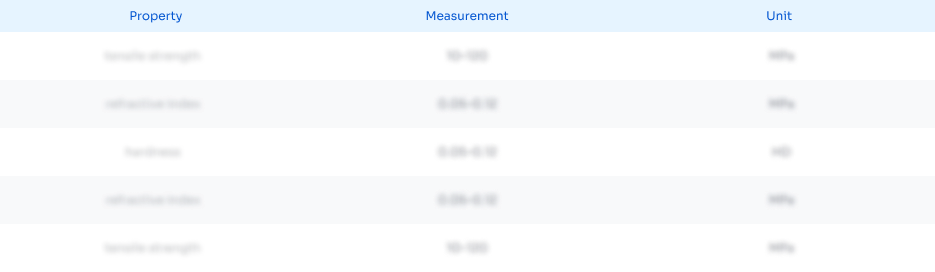
Abstract
Description
Claims
Application Information

- Generate Ideas
- Intellectual Property
- Life Sciences
- Materials
- Tech Scout
- Unparalleled Data Quality
- Higher Quality Content
- 60% Fewer Hallucinations
Browse by: Latest US Patents, China's latest patents, Technical Efficacy Thesaurus, Application Domain, Technology Topic, Popular Technical Reports.
© 2025 PatSnap. All rights reserved.Legal|Privacy policy|Modern Slavery Act Transparency Statement|Sitemap|About US| Contact US: help@patsnap.com