Resin rough grinding wheel and preparation method thereof
A grinding wheel and coarse grinding technology, which is applied in the direction of grinding/polishing equipment, abrasive materials, grinding devices, etc., can solve the problem of poor air permeability, toughness, and low safety, and the wear resistance, strength, and self-sharpening of resin grinding wheels are not ideal. and other problems, to achieve the effect of not easy to burn the workpiece, high grinding efficiency of the grinding wheel, and good air permeability
- Summary
- Abstract
- Description
- Claims
- Application Information
AI Technical Summary
Problems solved by technology
Method used
Image
Examples
Embodiment 1
[0051] Such as figure 1 As shown, first weigh 30 parts of microcrystalline corundum, 80 parts of zirconium corundum, 5 parts of garnet, 5 parts of phenolic resin solution, 25 parts of phenolic resin powder, 9 parts of pyrite, 1 part of cryolite, and 1 part of iron oxide. 1 part of quicklime, 3 parts of fluorite, 0.5 part of naphthalene grains. Then, put the abrasives such as microcrystalline corundum, zirconium corundum and garnet into the phenolic resin solution for soaking, and stir sufficiently to make the particle surface of the abrasive fully adhere to the phenolic resin solution. After sufficient infiltration, mix phenolic resin powder, quicklime powder, pyrite powder, iron oxide powder, cryolite, fluorite, naphthalene particles, plastic particles, hollow alumina and abrasives, and continue to stir until the various raw materials are fully mixed and uniform .
[0052] The mixed raw material granules are screened once through a 12-36 mesh sieve, and the granules that pa...
Embodiment 2
[0055] Such as figure 1 As shown, first weigh 35 parts of microcrystalline corundum, 90 parts of zirconium corundum, 8 parts of garnet, 10 parts of phenolic resin solution, 30 parts of phenolic resin powder, 15 parts of pyrite, 2 parts of cryolite, and 2 parts of iron oxide. 2 parts of quicklime, 4 parts of fluorite, and 1 part of plastic particles. Then, put the abrasives such as microcrystalline corundum, zirconium corundum and garnet into the phenolic resin solution for soaking, and stir sufficiently to make the particle surface of the abrasive fully adhere to the phenolic resin solution. After sufficient infiltration, mix phenolic resin powder, quicklime powder, pyrite powder, iron oxide powder, cryolite, fluorite, naphthalene particles, plastic particles, hollow alumina and abrasives, and continue to stir until the various raw materials are fully mixed and uniform .
[0056] The mixed raw material granules are screened once through a 12-36 mesh sieve, and the granules t...
Embodiment 3
[0059] Such as figure 1 As shown, first weigh 40 parts of microcrystalline corundum, 100 parts of zirconium corundum, 10 parts of garnet, 15 parts of phenolic resin solution, 45 parts of phenolic resin powder, 21 parts of pyrite, 3 parts of cryolite, and 3 parts of iron oxide. 3 parts of quicklime, 5 parts of fluorite, and 2 parts of hollow alumina. Then, put the abrasives such as microcrystalline corundum, zirconium corundum and garnet into the phenolic resin solution for soaking, and stir sufficiently to make the particle surface of the abrasive fully adhere to the phenolic resin solution. After sufficient infiltration, mix phenolic resin powder, quicklime powder, pyrite powder, iron oxide powder, cryolite, fluorite, naphthalene particles, plastic particles, hollow alumina and abrasives, and continue to stir until the various raw materials are fully mixed and uniform .
[0060] The mixed raw material granules are screened twice through a 12-36 mesh sieve, and the granules ...
PUM
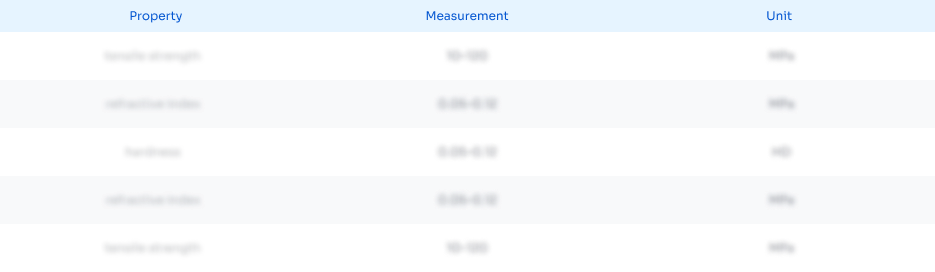
Abstract
Description
Claims
Application Information

- R&D
- Intellectual Property
- Life Sciences
- Materials
- Tech Scout
- Unparalleled Data Quality
- Higher Quality Content
- 60% Fewer Hallucinations
Browse by: Latest US Patents, China's latest patents, Technical Efficacy Thesaurus, Application Domain, Technology Topic, Popular Technical Reports.
© 2025 PatSnap. All rights reserved.Legal|Privacy policy|Modern Slavery Act Transparency Statement|Sitemap|About US| Contact US: help@patsnap.com