Magnetic separation device and method for reducing hematite-containing material by utilizing microwave
A magnetic separation device and technology for iron minerals, applied in chemical instruments and methods, magnetic separation, solid separation, etc., can solve the problems of equipment structure and related technologies failing to pass the standard, poor reduction and roasting quality, and large dust content in exhaust gas. Achieve the effect of shortening the reaction time, improving the magnetic separation efficiency, and large processing capacity
- Summary
- Abstract
- Description
- Claims
- Application Information
AI Technical Summary
Problems solved by technology
Method used
Image
Examples
Embodiment 1
[0034] Embodiment one: see Figure 1-Figure 3 , a magnetic separation device for microwave reduction of materials containing hematite, including a silo 1, a screw feeder 2, a star feeder 3, a preheating reaction furnace 5 and a microwave magnetic separator 6; the upper part of the microwave magnetic separator 6 , and the bottom are respectively provided with a discharge port 13 and a discharge port 12; the bottom of the preheating reaction furnace 5 communicates with the combustion chamber 4, and the gas in the gas storage tank 9 is mixed with the air blown in by the blower 10 and burns through the burner 11 The chamber 4 is combusted, and the CO high-temperature gas produced after combustion enters from the bottom of the preheating reaction furnace 5 .
[0035]Microwave magnetic separator 6 includes: reactor shell 6-1, reactor inner cavity 6-2, air inlet pipe 6-4, air outlet pipe 6-5, ore discharge pipe 6-6, microwave source 7, magnetic system 8. The air inlet pipe 6-4 commu...
Embodiment 2
[0037] Embodiment two: see Figure 4 , using the magnetic separation device of Example 1 to magnetically separate hematite (Fe 2 o 3 ) method for materials, including the following steps:
[0038] Crush the hematite-containing material to 80-100 mesh powder, add it to the silo 1, the powder enters the preheating reaction furnace 5 through the screw feeder 2 and the star feeder 3 for preheating, and the preheated powder Enter the microwave magnetic separator 6 through the air inlet pipe 6-4 for microwave heat treatment and magnetic separation; the products after magnetic separation are discharged from the discharge port 12 through the ore discharge pipe 6-6, and other materials are discharged from the discharge port 12 through the air outlet pipe 6-5. Discharge from the material port 13; or first go through dust removal and then discharge from the discharge port.
[0039] The materials containing hematite can be steel slag, low-grade limonite, iron ore and other ores.
[00...
Embodiment 3
[0042] Embodiment three: see Figure 4 , utilize the method for magnetically separating steel slag of magnetic separation device, the magnetic separation device that adopts is as described in example one, and this method comprises the following steps:
[0043] Crush steel slag into 80-100 mesh powder, measure 100kg of powder and add it to silo 1, the powder in silo 1 goes through screw feeder 2 and star feeder 3, and enters preheating reaction furnace 5 for preheating ;
[0044] Adjust the gas in the gas storage tank 9 and the air blown in by the blower 10, and burn in the combustion chamber 4 after being mixed by the burner 11, and the CO high-temperature gas produced after combustion enters from the bottom of the preheating reaction furnace 5 to preheat the material;
[0045] After the preheated material reaches 300°C, it enters the microwave magnetic separator 6 through the air inlet pipe 6-4 for microwave heat treatment. The microwave power is 15KW. Adjust the microwave o...
PUM
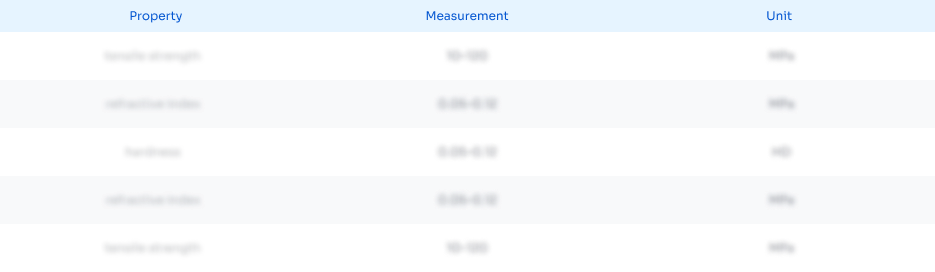
Abstract
Description
Claims
Application Information

- R&D
- Intellectual Property
- Life Sciences
- Materials
- Tech Scout
- Unparalleled Data Quality
- Higher Quality Content
- 60% Fewer Hallucinations
Browse by: Latest US Patents, China's latest patents, Technical Efficacy Thesaurus, Application Domain, Technology Topic, Popular Technical Reports.
© 2025 PatSnap. All rights reserved.Legal|Privacy policy|Modern Slavery Act Transparency Statement|Sitemap|About US| Contact US: help@patsnap.com