Method for purifying and preparing silicon carbide powder from crystalline silicon cutting waste mortar
A technology of crystal silicon cutting and waste mortar, which is applied in the direction of silicon carbide and carbide, can solve the problems of low recovery rate, difficult recovery, and reduction of silicon carbide output, and achieve the effect of simplifying the process and reducing environmental pollution
- Summary
- Abstract
- Description
- Claims
- Application Information
AI Technical Summary
Problems solved by technology
Method used
Image
Examples
specific Embodiment approach
[0028] The specific implementation method comprises the following steps:
[0029] (1) Weigh a certain amount of crystalline silicon cutting waste mortar, add a sufficient amount of organic solvent, and stir at room temperature to fully dissolve polyethylene glycol and organic solvent in the waste mortar to obtain a mixed solution.
[0030] (2) Filtrating the mixed solution to obtain a cutting waste slurry (mainly including trace metal elements, silicon and silicon carbide) from which polyethylene glycol, water and organic solvents have been removed.
[0031] (3) Add excess dilute acid to the obtained waste and stir in a water bath to fully react the dilute acid and metal elements to obtain a mixed solution containing metal salt, acid, silicon and silicon carbide.
[0032] (4) In order to wash away the metal salt and excess acid in the mixed solution, add enough deionized water to the mixed solution, stir, filter, put the filter cake in an oven to dry, and obtain a mixture of s...
Embodiment 1
[0037] Take 20g of cutting waste mortar, add 220ml of absolute ethanol, and stir for 0.5h. The resulting mixture was filtered, and the filter cake was taken in a beaker. Add 10% hydrochloric acid, stir in a water bath (85° C.) for 1.5 h, and filter to get the filter cake. The filter cake was placed in a drying oven and dried at 80°C for 2 hours. To obtain 13.4g of a mixture of silicon and silicon carbide, add 50g of glucose, take 400g of balls, and grind for 10h with a planetary ball. After ball milling, take the material and place it in a vacuum sintering furnace, and vacuumize it to 7.0×10 -3 After Pa, the temperature was raised to 1100°C at a rate of 15°C / min, held for 3 hours, and finally cooled down to room temperature naturally with the furnace, and decarbonized at 650°C to obtain 12.42g of high-purity silicon carbide.
Embodiment 2
[0039] Take 40g of cutting waste mortar, add 410ml of absolute ethanol, and stir for 0.5h. The resulting mixture was filtered, and the filter cake was taken in a beaker. Add 20% hydrochloric acid, stir in a water bath (75° C.) for 1 h, and filter to get the filter cake. The filter cake was dried in a drying oven at 95°C for 2 hours. To obtain 28g of silicon and silicon carbide mixture, add 8g of activated carbon, take 360g of balls, and stir ball mill for 15h. After ball milling, take the material and place it in a vacuum sintering furnace, and vacuumize it to 2.0×10 -2 After Pa, the temperature was raised to 1300°C at a rate of 15°C / min, kept for 2 hours, and finally cooled to room temperature naturally with the furnace, and carbon removal was carried out at 700°C to obtain 26.73g of high-purity silicon carbide.
PUM
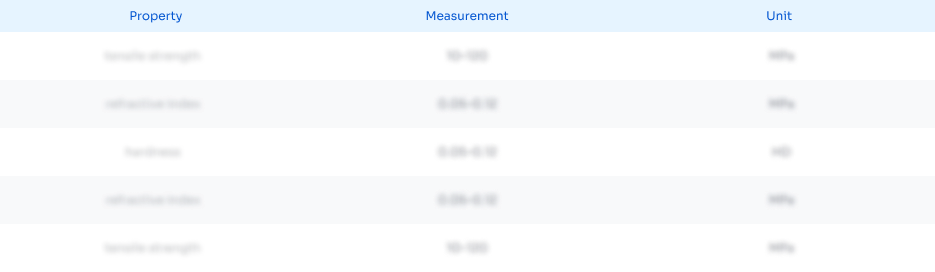
Abstract
Description
Claims
Application Information

- R&D
- Intellectual Property
- Life Sciences
- Materials
- Tech Scout
- Unparalleled Data Quality
- Higher Quality Content
- 60% Fewer Hallucinations
Browse by: Latest US Patents, China's latest patents, Technical Efficacy Thesaurus, Application Domain, Technology Topic, Popular Technical Reports.
© 2025 PatSnap. All rights reserved.Legal|Privacy policy|Modern Slavery Act Transparency Statement|Sitemap|About US| Contact US: help@patsnap.com