Alumina type high-temperature resistant corrosion resisting high strength alloy steel and preparation method thereof
A technology of aluminum oxide and high temperature resistance, which is applied in the field of austenitic alloy steel, can solve problems such as heat exchanger tube explosion accidents, difficult substrate steel protection, and easy failure, so as to prevent oxidation and corrosion, improve high temperature resistance, and good The effect of welding performance
- Summary
- Abstract
- Description
- Claims
- Application Information
AI Technical Summary
Problems solved by technology
Method used
Image
Examples
specific Embodiment approach 1
[0022] 1. According to the weight ratio of the elements in the product, the composition is C0.03-0.08%, Cr18-24%, Ni8-16%, Mn0.5-1%, Mo1-2%, W1-5%, Co0.05-0.5 %, Al3-8%, Nd0.1-2%, S≤0.007%, P≤0.02% and the balance of Fe are ready for alloying elements.
[0023] 2. Carry out chemical analysis of each element before smelting to ensure the accuracy of element content.
[0024] 3. Put the selected charge into the electric arc furnace for smelting, and wait for 10 minutes when the temperature of the furnace rises to 1680. Then transfer to ladle refining furnace (LF furnace) + vacuum argon-oxygen decarburization refining furnace (VOD furnace) for further refining, and complete the decarburization and degassing of alloy steel in this process. to obtain a clean slab.
[0025] The production process of the present invention adopts an electric arc furnace + a ladle refining furnace (LF furnace) + a vacuum argon-oxygen decarburization refining furnace (VOD furnace), and realizes the fo...
specific Embodiment approach 2
[0028] 1. According to the weight ratio of the elements in the product, the composition is C0.05-0.06%, Cr20-22%, Ni10-14%, Mn0.7-0.9%, Mo1.2-1.8%, W2-4%, Co0.1 The ratio of -0.4%, Al5-7%, Nd0.5-1.5%, S≤0.007%, P≤0.02% and the balance of Fe is ready for alloying elements.
[0029] 2. Carry out chemical analysis of each element before smelting to ensure the accuracy of element content.
[0030] 3. Put the selected charge into the electric arc furnace for smelting, and wait for 10 minutes when the temperature of the furnace rises to 1680. Then transfer to the ladle refining furnace (LF furnace) + vacuum argon oxygen decarburization refining furnace (VOD furnace) for further refining and then tap the steel.
specific Embodiment approach 3
[0031] 1. According to the weight ratio of the elements in the product, the composition is C0.06%, Cr21%, Ni12%, Mn0.8%, Mo1.6%, W3%, Co0.3%, Al7%, Nd1.2%, S≤ The ratio of 0.007%, P≤0.02% and the balance of Fe is ready for alloying elements.
[0032] 2. Carry out chemical analysis of each element before smelting to ensure the accuracy of element content.
[0033] 3. Put the selected charge into the electric arc furnace for smelting, and wait for 10 minutes when the temperature of the furnace rises to 1680. Then transfer to the ladle refining furnace (LF furnace) + vacuum argon oxygen decarburization refining furnace (VOD furnace) for further refining and then tap the steel.
PUM
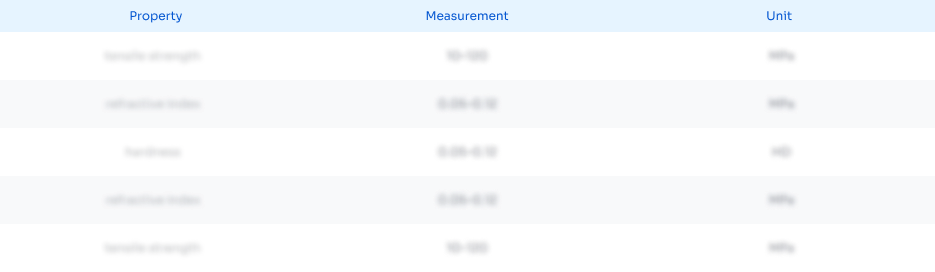
Abstract
Description
Claims
Application Information

- R&D Engineer
- R&D Manager
- IP Professional
- Industry Leading Data Capabilities
- Powerful AI technology
- Patent DNA Extraction
Browse by: Latest US Patents, China's latest patents, Technical Efficacy Thesaurus, Application Domain, Technology Topic, Popular Technical Reports.
© 2024 PatSnap. All rights reserved.Legal|Privacy policy|Modern Slavery Act Transparency Statement|Sitemap|About US| Contact US: help@patsnap.com