Reactive pressure-sensitive adhesive having performance of structural adhesive after being cured, and preparation method thereof
A pressure-sensitive adhesive, reactive technology, applied in the direction of adhesives, film/sheet adhesives, adhesive types, etc., can solve the problem that the bonding strength cannot reach the bonding level of structural adhesives and the existence of storage and other issues, to achieve the effect of good storage stability
- Summary
- Abstract
- Description
- Claims
- Application Information
AI Technical Summary
Problems solved by technology
Method used
Image
Examples
Embodiment 1
[0030] 60 parts of butyl acrylate, 12 parts of styrene, 9 parts of methacrylic acid and 19 parts of methyl methacrylate were subjected to free radical polymerization and discharged. That is component a.
[0031] Take 50 parts of component a and dissolve in 50 parts of ethanol, and add 40 parts of bisphenol A epoxy resin E51 and 4 parts of latent curing agent dicyandiamide for epoxy resin.
[0032] Stir until completely dissolved.
[0033] The solvent-based pressure-sensitive adhesive was coated on a substrate made of clean 25 μm polyethylene terephthalate without inert treatment and a 25 μm polyethylene terephthalate coated with a release agent. ester, and then placed at room temperature for 2 hours, all covered with a 25 μm polyethylene terephthalate substrate coated with a release agent. Thereafter, it was cut into widths of 25 mm to make single-sided adhesive tapes and double-sided adhesive tapes with a thermosetting pressure-sensitive adhesive layer thickness of 30 μm. ...
Embodiment 2
[0035] 68 parts of butyl acrylate, 8 parts of styrene, 12 parts of methacrylic acid and 12 parts of methyl methacrylate were subjected to free radical polymerization and discharged. That is component a.
[0036] Take 50 parts of component a and dissolve in 60 parts of acetone, and add 46 parts of bisphenol A epoxy resin E51 and 2.6 parts of latent curing agent 2-methylimidazole for epoxy resin.
[0037] Stir until completely dissolved.
[0038] The solvent-based pressure-sensitive adhesive was coated on a substrate made of clean 25 μm polyethylene terephthalate without inert treatment and a 25 μm polyethylene terephthalate coated with a release agent. ester, and then placed at room temperature for 2 hours, all covered with a 25 μm polyethylene terephthalate substrate coated with a release agent. Thereafter, it was cut into widths of 25 mm to make single-sided adhesive tapes and double-sided adhesive tapes with a thermosetting pressure-sensitive adhesive layer thickness of 30...
Embodiment 3
[0040] 71 parts of butyl acrylate, 7 parts of styrene, 5 parts of methacrylic acid and 17 parts of methyl methacrylate were polymerized and discharged. That is component a.
[0041] Take 50 parts of component a and dissolve in 70 parts of toluene, and add 54 parts of bisphenol A epoxy resin E51 and 3 parts of latent curing agent 2-ethylimidazole for epoxy resin.
[0042] Stir until completely dissolved.
[0043] The solvent-based pressure-sensitive adhesive was coated on a substrate made of clean 25 μm polyethylene terephthalate without inert treatment and a 25 μm polyethylene terephthalate coated with a release agent. ester, and then placed at room temperature for 2 hours, all covered with a 25 μm polyethylene terephthalate substrate coated with a release agent. Thereafter, it was cut into widths of 25 mm to make single-sided adhesive tapes and double-sided adhesive tapes with a thermosetting pressure-sensitive adhesive layer thickness of 30 μm.
PUM
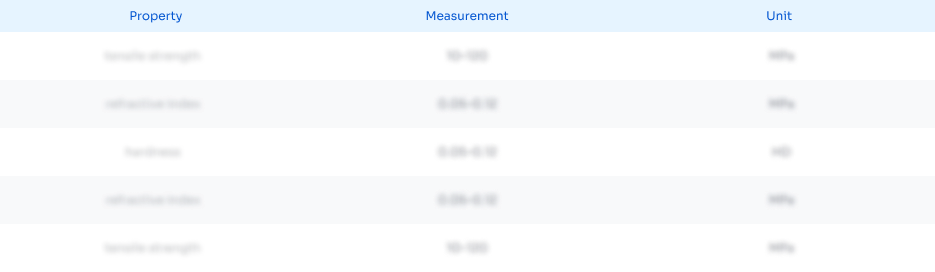
Abstract
Description
Claims
Application Information

- R&D Engineer
- R&D Manager
- IP Professional
- Industry Leading Data Capabilities
- Powerful AI technology
- Patent DNA Extraction
Browse by: Latest US Patents, China's latest patents, Technical Efficacy Thesaurus, Application Domain, Technology Topic, Popular Technical Reports.
© 2024 PatSnap. All rights reserved.Legal|Privacy policy|Modern Slavery Act Transparency Statement|Sitemap|About US| Contact US: help@patsnap.com