Method for cladding TiC enhanced Ni3Al based composite coating on surface of aluminum alloy
A technology of aluminum alloy surface and composite coating, applied in metal material coating technology, coating, metal processing equipment, etc., can solve problems such as inability to wear aluminum alloy, limited wear resistance, etc., achieve high production efficiency, Good wear resistance, uniform TiC distribution and dispersion effect
- Summary
- Abstract
- Description
- Claims
- Application Information
AI Technical Summary
Problems solved by technology
Method used
Examples
Embodiment 1
[0020] (2) A Ni-Cr-B-Si-based alloy and TiC powder are uniformly mixed as the coating material; the TiC content is 10 (wt)%, and the chemical composition Cr of Ni-Cr-B-Si is 7.5 (wt) %, B is 2.5 (wt)%, Si is 4.0 (wt)%, and Ni is the balance.
[0021] (3) The laser beam is used to form a molten pool on the metal surface of the aluminum alloy base; the laser treatment process parameters are laser spot diameter 6mm, power 1.2kW, and beam scanning speed 8mm / s.
[0022] (4) Send the coating material into the molten pool to form a metallurgical bond with the base metal, use the chemical exothermic reaction between Ni and Al, and form TiC to strengthen Ni after the reaction 3 Al-based composite coating.
[0023] The element distribution at the interface of the sample after cladding was analyzed, and the concentration of Al, Ni, Cr, Si, and B elements at the interface showed a slow transition trend, which indicated that a chemical metallurgical bond was formed between the nickel-base...
Embodiment 2
[0025] (2) Ni-Cr-B-Si-based alloy and TiC powder are uniformly mixed as the coating material; the TiC content is 12 (wt)%, and the chemical composition Cr of Ni-Cr-B-Si is 7.5 (wt)% , B is 2.5 (wt)%, Si is 4.0 (wt)%, and Ni is the balance.
[0026] (3) The laser beam is used to form a molten pool on the metal surface of the aluminum alloy substrate; the laser treatment process parameters are laser spot diameter 8mm, power 1.5kW, and beam scanning speed 10mm / s.
[0027] (4) Send the coating material into the molten pool to form a metallurgical bond with the base metal, use the chemical exothermic reaction between Ni and Al, and form TiC to strengthen Ni after the reaction 3 Al-based composite coating.
[0028] Example 3: A kind of aluminum alloy surface cladding TiC reinforced Ni 3 The method for an Al-based composite coating comprises the following steps: (1) cleaning the metal surface of an aluminum alloy base to remove oil stains and oxide layers; (2) uniformly mixing a Ni...
Embodiment 3
[0029] The laser treatment process parameters are laser spot diameter 4-8mm, power 1.2-2kW, beam scanning speed 3-10mm / s.
PUM
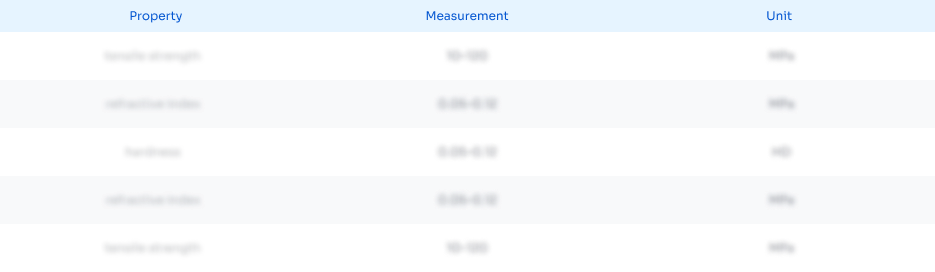
Abstract
Description
Claims
Application Information

- R&D
- Intellectual Property
- Life Sciences
- Materials
- Tech Scout
- Unparalleled Data Quality
- Higher Quality Content
- 60% Fewer Hallucinations
Browse by: Latest US Patents, China's latest patents, Technical Efficacy Thesaurus, Application Domain, Technology Topic, Popular Technical Reports.
© 2025 PatSnap. All rights reserved.Legal|Privacy policy|Modern Slavery Act Transparency Statement|Sitemap|About US| Contact US: help@patsnap.com