Efficient reburning denitrification device and technical method
A denitrification and high-efficiency technology, applied in the direction of improving energy efficiency, process efficiency, furnace, etc., can solve the problems of failing to meet nitrogen oxide emission standards, affecting the decomposition efficiency of raw materials, and high operating costs, so as to reduce denitrification Effects of operating costs, enhancing market competitiveness, and reducing denitrification costs
- Summary
- Abstract
- Description
- Claims
- Application Information
AI Technical Summary
Problems solved by technology
Method used
Image
Examples
Embodiment Construction
[0020] Such as figure 1 As shown, the raw meal enters the multi-stage cyclone preheater (not shown in the figure) after preparation and grinding, and enters the calciner 19 from the raw meal inlet 4 for decomposition, and the coal powder in the coal powder bin 1 is measured by the rotor scale 2 Then enter the main combustion zone from the low-nitrogen main burner 3 of the calciner 19, and contact with the high-temperature secondary air from the cement rotary kiln 8 (the high-temperature secondary air enters the main combustion zone from the secondary air inlet 7 at the bottom of the calciner 19) Afterwards, it begins to burn to release heat, and the main combustion zone needs a large amount of oxygen. Therefore, the tertiary air is taken from the cooler 8A position of the cement rotary kiln 8 and enters the main combustion zone from the tertiary air inlet 6 to ensure sufficient combustion (the tertiary air drawn from the cement rotary kiln 8 The wind provides oxygen for the co...
PUM
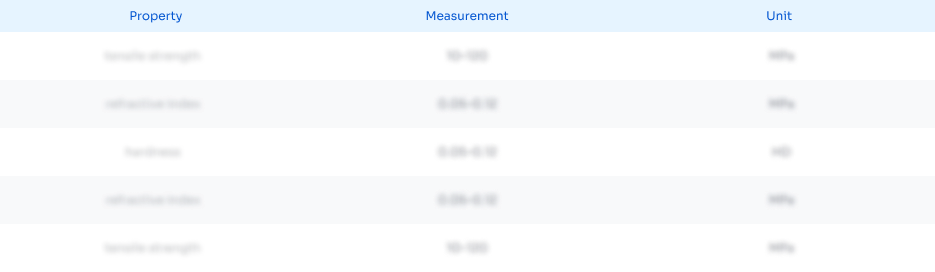
Abstract
Description
Claims
Application Information

- R&D
- Intellectual Property
- Life Sciences
- Materials
- Tech Scout
- Unparalleled Data Quality
- Higher Quality Content
- 60% Fewer Hallucinations
Browse by: Latest US Patents, China's latest patents, Technical Efficacy Thesaurus, Application Domain, Technology Topic, Popular Technical Reports.
© 2025 PatSnap. All rights reserved.Legal|Privacy policy|Modern Slavery Act Transparency Statement|Sitemap|About US| Contact US: help@patsnap.com