Polymethyl methacrylate (PMMA) continuous production process for long-time operation without accumulation
A long-term operation and production process technology, which is applied in the preparation of polymers and PMMA continuous production process, can solve the problems that the reaction cannot continue continuously, the product contains foreign matter, polymer accumulation, etc., and achieves the goal of ensuring long-term continuous and stable operation Effect
- Summary
- Abstract
- Description
- Claims
- Application Information
AI Technical Summary
Problems solved by technology
Method used
Examples
Embodiment 1
[0025] A kind of PMMA continuous production technique that long-term operation does not accumulate material, steps are as follows by weight:
[0026] (1) Pre-polymerization: Take 80 parts of methyl methacrylate as the main monomer, 20 parts of butyl acrylate as the comonomer, 10 parts of toluene as the solvent, and 98×10 tert-butyl peracetic acid as the first initiator -4 Parts, 0.3 parts of chain transfer agent tert-dodecyl mercaptan, 0.1-0.3 parts of n-dodecyl alcohol as release agent, stir well until they are evenly mixed, add them into the polymerization kettle, control the reaction temperature at 150°C, pressure at 1MPa, at 30r Stirring reaction 3h under the rotating speed of / min;
[0027] The polymerization kettle adopts the form of entering from the bottom and exiting from the top. During normal production, the polymerization kettle is kept fully filled and the pressure is kept stable. The inner wall of the polymerization kettle is chrome-plated or polished, and a ribb...
Embodiment 2
[0035] A kind of PMMA continuous production technique that long-term operation does not accumulate material, steps are as follows by weight:
[0036] (1) Pre-polymerization: Take 90 parts of methyl methacrylate as the main monomer, 10 parts of butyl acrylate as the comonomer, 15 parts of ethylbenzene as the solvent, and 98×10 tert-butyl peracetic acid as the first initiator -4 part, 0.3 part of chain transfer agent tert-dodecyl mercaptan, 0.1 part of mold release agent n-dodecyl alcohol, stir well until they are evenly mixed, add them into the polymerization kettle, control the reaction temperature at 160°C, pressure at 0.8MPa, at 80r / The reaction was stirred for 1 h at a speed of 1 min;
[0037] The polymerization kettle adopts the form of entering from the bottom and exiting from the top. During normal production, the polymerization kettle is kept fully filled and the pressure is kept stable. The inner wall of the polymerization kettle is chrome-plated or polished, and a ri...
Embodiment 3
[0060] A kind of PMMA continuous production technique that long-term operation does not accumulate material, steps are as follows by weight:
[0061] (1) Pre-polymerization: Take 100 parts of methyl methacrylate as the main monomer, 25 parts of comonomer, 5 parts of solvent, and 110×10 first initiator -4 Parts, 0.5 parts of chain transfer agent, 0.3 parts of release agent, fully stirred until they are evenly mixed, added to the polymerization kettle, controlled reaction temperature 140 ° C, pressure 1.2 MPa, stirred and reacted at a speed of 70 r / min for 1 h;
[0062] The polymerization kettle adopts the form of entering from the bottom and exiting from the top. During normal production, the polymerization kettle is kept fully filled and the pressure is kept stable. The inner wall of the polymerization kettle is chrome-plated or polished, and a ribbon stirrer is used;
[0063] (2) Secondary polymerization: The mixture obtained in step (1) is continuously transported to the sti...
PUM
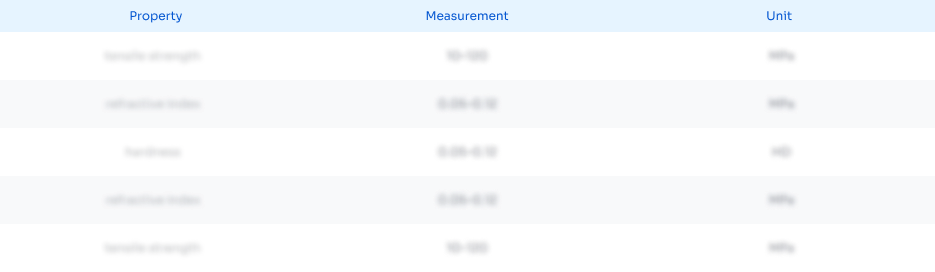
Abstract
Description
Claims
Application Information

- R&D
- Intellectual Property
- Life Sciences
- Materials
- Tech Scout
- Unparalleled Data Quality
- Higher Quality Content
- 60% Fewer Hallucinations
Browse by: Latest US Patents, China's latest patents, Technical Efficacy Thesaurus, Application Domain, Technology Topic, Popular Technical Reports.
© 2025 PatSnap. All rights reserved.Legal|Privacy policy|Modern Slavery Act Transparency Statement|Sitemap|About US| Contact US: help@patsnap.com