PC and copolyester blend and preparation method thereof
A copolyester and blend technology, which is applied in the field of PC and copolyester blends and their preparation, can solve problems such as poor PC processing fluidity, and achieve the effects of improving fluidity, reducing processing and molding temperature, and expanding the scope of use.
- Summary
- Abstract
- Description
- Claims
- Application Information
AI Technical Summary
Problems solved by technology
Method used
Image
Examples
preparation example Construction
[0015] The method for preparing PC and copolyester blend that the embodiment of the present invention provides comprises the following steps:
[0016] Weigh each component respectively according to above-mentioned PC and copolyester blend formula;
[0017] Mix all components evenly;
[0018] Each component is melted and then extruded into granules.
[0019] The PC resin described in the embodiment of the present invention is preferably bisphenol A aromatic polycarbonate with a molecular weight of 25,000-30,000, and PC IR2200 from Idemitsu is selected here. Described copolyester is preferably polyethylene terephthalate-1,4-cyclohexanedimethanol ester, here selects polyethylene terephthalate-1 developed and produced by American Eastman, 4-Cyclohexanedimethanol ester. Wherein, the polyethylene terephthalate-1,4-cyclohexanedimethanol is prepared from three monomers of terephthalic acid, ethylene glycol and 1,4-cyclohexanedimethanol by transesterification The polycondensation p...
Embodiment 1
[0031] The PC and copolyester blend provided in this example is prepared by the following components by weight percentage: 90 parts of PC resin, 5 parts of copolyester PETG, 3 parts of toughening agent SIM, 1 part of compatibilizer T55-GMA, anti 10760.3 parts of oxygen agent, 1680.2 parts of antioxidant, 0.5 part of lubricant EBS.
[0032] Dry 90 parts of PC resin first, then mix it with the copolyester, toughener, compatibilizer, antioxidant and lubricant in the mixing tank, and extrude it through a twin-screw extruder Granulate, cool and cut into pellets. The process parameters of the twin-screw extruder are: the temperature of the first zone is 160-210°C, the temperature of the second zone is 190-220°C, the temperature of the third zone is 210-230°C, the temperature of the fourth zone is 220-230°C, the temperature of the fifth zone is 225-235°C, The temperature of the sixth zone is 220-230°C, the temperature of the seventh zone is 210-230°C, the temperature of the eighth z...
Embodiment 2
[0037] The blend of PC and copolyester provided in this example is formulated by weight percentage from the following components: 82.3 parts of PC resin, 10 parts of copolyester PETG, 5 parts of toughening agent SIM, 2 parts of compatibilizer T55-GMA, anti 10760.2 parts of oxygen agent, 1680.3 parts of antioxidant, 0.2 part of lubricant EBS.
[0038] Here, dry 82.3 parts of PC resin first, then mix with the copolyester, toughening agent, compatibilizer, antioxidant and lubricant in the mixing tank with the above ratio, and extrude through the twin-screw extruder Granulate, cool and cut into pellets. The process parameters of the twin-screw extruder are: the temperature of the first zone is 160-210°C, the temperature of the second zone is 190-220°C, the temperature of the third zone is 210-230°C, the temperature of the fourth zone is 220-230°C, the temperature of the fifth zone is 225-235°C, The temperature of the sixth zone is 220-230°C, the temperature of the seventh zone is...
PUM
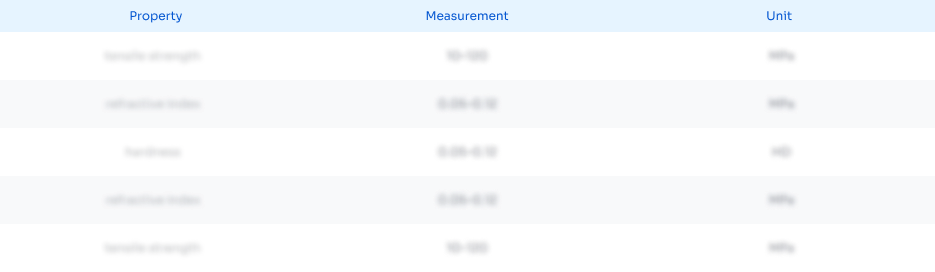
Abstract
Description
Claims
Application Information

- R&D Engineer
- R&D Manager
- IP Professional
- Industry Leading Data Capabilities
- Powerful AI technology
- Patent DNA Extraction
Browse by: Latest US Patents, China's latest patents, Technical Efficacy Thesaurus, Application Domain, Technology Topic, Popular Technical Reports.
© 2024 PatSnap. All rights reserved.Legal|Privacy policy|Modern Slavery Act Transparency Statement|Sitemap|About US| Contact US: help@patsnap.com