Polypropylene composite material with high strength and high elongation at break and preparation method thereof
A composite material, polypropylene technology, applied in polypropylene composite materials, polypropylene composite materials with high elongation at break, high strength field, can solve the problem of high ductility, increased material cost, loss of bending resistance, etc. problems, achieve high impact toughness, improve performance, and reduce dosage
- Summary
- Abstract
- Description
- Claims
- Application Information
AI Technical Summary
Problems solved by technology
Method used
Image
Examples
Embodiment 1
[0034] Weigh 94.5% of polypropylene, 5% of superfine calcium carbonate, 0.1% of Irganox 1010, 0.1% of Igrafos 168, and 0.3% of Negonox DSTP by weight, and dry mix them in a high-speed mixer for 5 minutes, then add the Melting extrusion granulation in the extruder, where the temperature inside the screw barrel is: 200°C in the first zone, 210°C in the second zone, 210°C in the third zone, 210°C in the fourth zone, 220°C in the head, and the speed of the twin-screw extruder is 400 rpm / Minute. After the particles are dried, they are injection molded on an injection molding machine to prepare samples.
Embodiment 2
[0036] Weigh 79.5% of polypropylene, 20% of superfine calcium carbonate, 0.1% of Irganox 1010, 0.1% of Igrafos 168, and 0.3% of Negonox DSTP by weight, and dry mix them in a high-speed mixer for 5 minutes, then add the Melting extrusion granulation in the extruder, where the temperature inside the screw barrel is: 200°C in the first zone, 210°C in the second zone, 210°C in the third zone, 210°C in the fourth zone, 220°C in the head, and the speed of the twin-screw extruder is 400 rpm / Minute. After the particles are dried, they are injection molded on an injection molding machine to prepare samples.
Embodiment 3
[0038] Weigh 69.5% of polypropylene, 30% of superfine calcium carbonate, 0.1% of Irganox 1010, 0.1% of Igrafos 168, and 0.3% of Negonox DSTP by weight, dry mix them in a high-speed mixer for 5 minutes, and then add Melting extrusion granulation in the extruder, where the temperature inside the screw barrel is: 200°C in the first zone, 210°C in the second zone, 210°C in the third zone, 210°C in the fourth zone, 220°C in the head, and the speed of the twin-screw extruder is 400 rpm / Minute. After the particles are dried, they are injection molded on an injection molding machine to prepare samples.
PUM
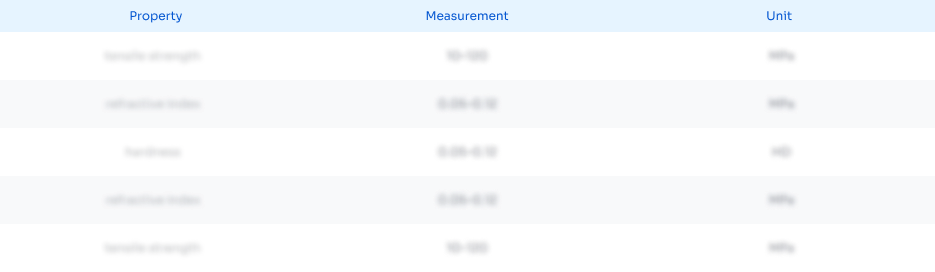
Abstract
Description
Claims
Application Information

- R&D
- Intellectual Property
- Life Sciences
- Materials
- Tech Scout
- Unparalleled Data Quality
- Higher Quality Content
- 60% Fewer Hallucinations
Browse by: Latest US Patents, China's latest patents, Technical Efficacy Thesaurus, Application Domain, Technology Topic, Popular Technical Reports.
© 2025 PatSnap. All rights reserved.Legal|Privacy policy|Modern Slavery Act Transparency Statement|Sitemap|About US| Contact US: help@patsnap.com