Corrosion-resisting ferroalloy material for fastener and preparation method thereof
A ferroalloy and fastener technology, which is applied in the field of corrosion-resistant ferrous alloy materials for fasteners and its preparation, can solve the problems of poor cold pier and punching performance, broken bolts, low elongation, etc., and achieves refining grains and improving strength. , improve the uniform effect
- Summary
- Abstract
- Description
- Claims
- Application Information
AI Technical Summary
Problems solved by technology
Method used
Examples
Embodiment 1
[0033] A corrosion-resistant iron alloy material for fasteners, its composition is by weight percentage, 0.08% carbon, 15% manganese, 0.3% silicon, 14.5% chromium, 0.03% molybdenum, 0.5% nickel, 0.03% vanadium, 0.1% titanium, 0.01% zirconium, 0.01% boron, 0.3% copper, 0.15% nitrogen, 0.001% lanthanum, and the balance is iron.
[0034] Described preparation method is:
[0035] Ingredients, by weight percentage, 0.08% carbon, 15% manganese, 0.3% silicon, 14.5% chromium, 0.03% molybdenum, 0.5% nickel, 0.03% vanadium, 0.1% titanium, 0.01% Zirconium, 0.01% boron, 0.3% copper, 0.15% nitrogen, 0.001% lanthanum, and the balance is iron for batching;
[0036] For smelting, put half of the calculated amount of iron and carbon, manganese, silicon, chromium, molybdenum, nickel, vanadium, and zirconium into the smelting furnace for melting. After melting into liquid, add titanium, iron lanthanum and the remaining iron, and Carry out refining at 1250-1350°C for 1.5 hours, and feed 0.5MPa ...
Embodiment 2
[0043] A corrosion-resistant iron alloy material for fasteners, its composition is by weight percentage, 0.10% carbon, 15.5% manganese, 0.6% silicon, 15.0% chromium, 0.05% molybdenum, 1.0% nickel, 0.05% vanadium, 0.3% titanium, 0.03% zirconium, 0.03% boron, 0.5% copper, 0.25% nitrogen, 0.002% lanthanum, and the balance is iron.
[0044] Described preparation method is:
[0045] Ingredients, by weight percentage, 0.10% carbon, 15.5% manganese, 0.6% silicon, 15.0% chromium, 0.05% molybdenum, 1.0% nickel, 0.05% vanadium, 0.3% titanium, 0.03% Zirconium, 0.03% boron, 0.5% copper, 0.25% nitrogen, 0.002% lanthanum, and the balance is iron for batching;
[0046]For smelting, put half of the calculated amount of iron and carbon, manganese, silicon, chromium, molybdenum, nickel, vanadium, and zirconium into the smelting furnace for melting. After melting into liquid, add titanium, iron lanthanum and the remaining iron, and Carry out refining at 1250-1350°C for 2 hours, and feed 1.0MPa...
Embodiment 3
[0053] A corrosion-resistant iron alloy material for fasteners, its composition is by weight percentage, 0.09% carbon, 15.2% manganese, 0.5% silicon, 14.8% chromium, 0.04% molybdenum, 0.8% nickel, 0.035% vanadium, 0.2% titanium, 0.02% zirconium, 0.025% boron, 0.45% copper, 0.20% nitrogen, 0.0015% lanthanum, 0.015% niobium, and the balance is iron.
[0054] Described preparation method is:
[0055] Ingredients, by weight percentage, 0.09% carbon, 15.2% manganese, 0.5% silicon, 14.8% chromium, 0.04% molybdenum, 0.8% nickel, 0.035% vanadium, 0.2% titanium, 0.02% Zirconium, 0.025% boron, 0.45% copper, 0.20% nitrogen, 0.0015% lanthanum, 0.015% niobium, and the balance is iron for batching;
[0056] For smelting, put half of the calculated amount of iron and carbon, manganese, silicon, chromium, molybdenum, nickel, vanadium, and zirconium into the smelting furnace for melting. After melting into liquid, add titanium, ferrolanthanum, ferroniobium and the rest Iron, and refining at ...
PUM
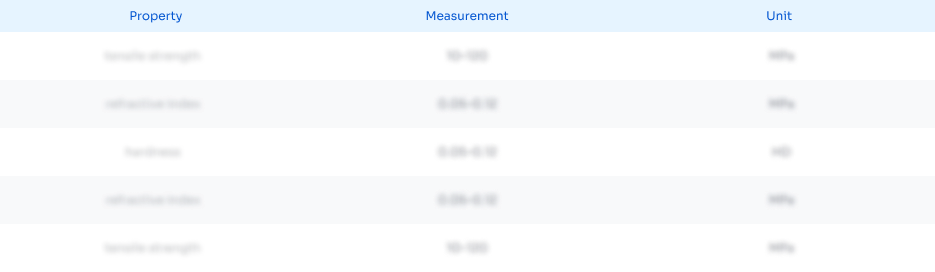
Abstract
Description
Claims
Application Information

- Generate Ideas
- Intellectual Property
- Life Sciences
- Materials
- Tech Scout
- Unparalleled Data Quality
- Higher Quality Content
- 60% Fewer Hallucinations
Browse by: Latest US Patents, China's latest patents, Technical Efficacy Thesaurus, Application Domain, Technology Topic, Popular Technical Reports.
© 2025 PatSnap. All rights reserved.Legal|Privacy policy|Modern Slavery Act Transparency Statement|Sitemap|About US| Contact US: help@patsnap.com