Special wood modifier and preparation method thereof
A modifier and wood technology, applied in the direction of impregnating wood, wood impregnation, wood processing equipment, etc., can solve the problems of unsatisfactory material of fast-growing forest, easy deformation, effective effect, etc., to achieve improved corrosion resistance and water solubility. Good, low viscosity effect
- Summary
- Abstract
- Description
- Claims
- Application Information
AI Technical Summary
Problems solved by technology
Method used
Image
Examples
Embodiment 1
[0018] Accurately weigh the following weights of the raw material components:
[0019] 720 parts of formaldehyde solution with a mass concentration of 35%, 20 parts of urea, 250 parts of phenol, 200 parts of methyl silanol, 15 parts of sodium hydroxide, and 20 parts of barium chloride.
[0020] Add melted phenol into the reaction kettle, start stirring, then add 1 / 3 weight of formaldehyde solution, and slowly add 1 / 2 weight of alkaline catalyst sodium hydroxide, and then raise the temperature of the kettle to 45 ° C ~ 50 ° C Stop heating. At this time, the temperature of the kettle continues to rise, and the temperature of the kettle is controlled not to exceed 60°C. After the temperature rise is completed, it is kept at 50°C for 1 hour. The temperature of the kettle is raised to 85°C-90°C, kept for 1 hour, added urea and additives, kept stirred for 30 minutes, and then cooled down to 30°C to obtain a reddish-brown viscous liquid, which is the wood modifier of the present inve...
Embodiment 2
[0022] Accurately weigh the following weights of the raw material components:
[0023] 350 parts of formaldehyde solution with a mass concentration of 36%, 10 parts of urea, 130 parts of xylenol, 110 parts of methyl silanol, 10 parts of barium hydroxide, and 10 parts of barium chloride.
[0024] Add melted phenol into the reaction kettle, start stirring, then add 1 / 3 weight of formaldehyde solution, and slowly add 1 / 2 weight of basic catalyst barium hydroxide, and then raise the temperature of the kettle to 45 ° C ~ 50 ° C Stop heating. At this time, the temperature of the kettle continues to rise, and the temperature of the kettle is controlled not to exceed 60°C. After the temperature rise is completed, it is kept at 50°C for 1 hour. The temperature of the kettle is raised to 85°C-90°C, kept for 1 hour, added urea and additives, kept stirred for 30 minutes, and then cooled down to 30°C to obtain a reddish-brown viscous liquid, which is the wood modifier of the present invent...
Embodiment 3
[0026] Accurately weigh the following weights of the raw material components:
[0027] 540 parts of formaldehyde solution with a mass concentration of 36%, 20 parts of urea, 200 parts of phenol, 165 parts of ethyl silanol, 15 parts of sodium hydroxide, and 15 parts of aluminum chloride.
[0028] Add melted phenol into the reaction kettle, start stirring, then add 1 / 3 weight of formaldehyde solution, and slowly add 1 / 2 weight of basic catalyst, then raise the temperature of the kettle to 45°C to 50°C and stop heating. At this time, the temperature of the kettle continues to rise, and the temperature of the kettle is controlled not to exceed 60°C. After the temperature rise is completed, it is kept at 50°C for 1 hour. After the heat preservation is completed, the remaining formaldehyde solution and organic silicon are added, and the remaining alkaline catalyst sodium hydroxide is slowly added. The temperature of the kettle is raised to 85°C-90°C, kept for 1 hour, added urea and ...
PUM
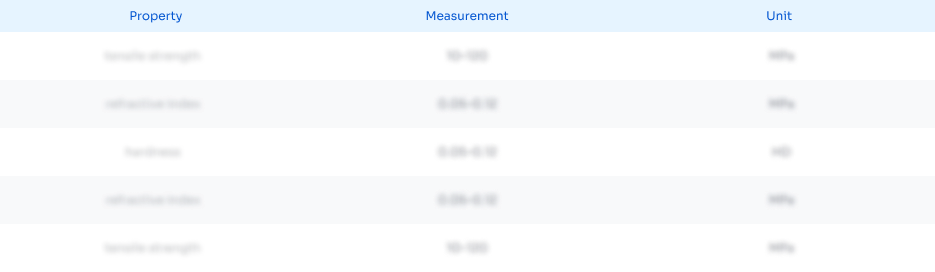
Abstract
Description
Claims
Application Information

- R&D
- Intellectual Property
- Life Sciences
- Materials
- Tech Scout
- Unparalleled Data Quality
- Higher Quality Content
- 60% Fewer Hallucinations
Browse by: Latest US Patents, China's latest patents, Technical Efficacy Thesaurus, Application Domain, Technology Topic, Popular Technical Reports.
© 2025 PatSnap. All rights reserved.Legal|Privacy policy|Modern Slavery Act Transparency Statement|Sitemap|About US| Contact US: help@patsnap.com