Graphene compounded with stibine cobalt base skutterudite thermoelectric material and preparation method of material
A technology for compounding cobalt antimonide-based and thermoelectric materials, which is applied in the direction of thermoelectric device node lead-out materials, thermoelectric device manufacturing/processing, etc., and can solve the problems of long preparation cycle, high energy consumption, and unsuitability for industrialized large-scale production. , to achieve the effect of short preparation time, good repeatability and good industrialization prospects
- Summary
- Abstract
- Description
- Claims
- Application Information
AI Technical Summary
Problems solved by technology
Method used
Image
Examples
Embodiment 1
[0026] Using high-purity (>99%) granular metal elemental ytterbium (Yb) powder, cobalt (Co) powder, and antimony (Sb) powder as initial raw materials, according to the chemical formula M x co 4 Sb 12 (M=Yb; X=0.35) is Yb 0.35 co 4 Sb 12 The stoichiometric ratio batching, weighs the powder that total amount is about 12g.
[0027] Put the above powder and 0.05g of carbon nanotubes into a stainless steel ball mill jar, and add three kinds of stainless steel balls with different diameters (the mass ratio of grinding balls to powder is 13:1), vacuumize and pass Ar inert gas protection in the glove box Finally, seal it, and then put the ball mill jar into a high-energy ball mill for ball milling at a speed of 350 rpm for 18 hours to obtain alloy powder.
[0028] The obtained alloy powder is loaded into a graphite mold, and then put into a spark plasma sintering device for sintering under an Ar atmosphere. The sintering temperature is 550° C., the holding time is 5 minutes, the...
Embodiment 2
[0033] Using high-purity (>99%) granular metallic elemental barium (Ba) powder, cobalt (Co) powder, and antimony (Sb) powder as initial raw materials, according to the chemical formula Ba x co 4 Sb 12 (M=Ba; X=0.8) that is Ba 0.8 co 4 Sb 12 The stoichiometric ratio batching, weighs the powder that total amount is about 12g.
[0034] Put the above powder and 0.1g carbon nanotubes into a stainless steel ball mill jar, and add three kinds of stainless steel balls with different diameters (mass ratio of grinding ball to powder is 13:1), vacuumize and pass Ar inert gas protection in the glove box Finally, seal it, then put the ball mill jar into a high-energy ball mill for ball milling, and ball mill it for 12 hours at a speed of 350 rpm to obtain alloy powder.
[0035] The obtained alloy powder is loaded into a graphite mold, and then put into a spark plasma sintering device for sintering under an Ar atmosphere. The sintering temperature is 600° C., the holding time is 5 min...
Embodiment 3
[0038] Using high-purity (>99%) granular metal elemental lithium (Li) powder, cobalt (Co) powder, and antimony (Sb) powder as initial raw materials, according to the chemical formula M x co 4 Sb 12 (M=Li; X=0.4) namely Li 0.4 co 4 Sb 12 The stoichiometric ratio batching, weighs the powder that total amount is about 12g.
[0039] Put the above powder and 0.05g of carbon nanotubes into a stainless steel ball mill jar, and add three kinds of stainless steel balls with different diameters (the mass ratio of grinding balls to powder is 13:1), vacuumize and pass Ar inert gas protection in the glove box Finally, seal it, and then put the ball mill jar into a high-energy ball mill for ball milling, and ball mill it for 9 hours at a speed of 350 rpm to obtain alloy powder.
[0040]The obtained alloy powder is loaded into a graphite mold, and then put into a spark plasma sintering device for sintering under an Ar atmosphere. The sintering temperature is 650° C., the holding time i...
PUM
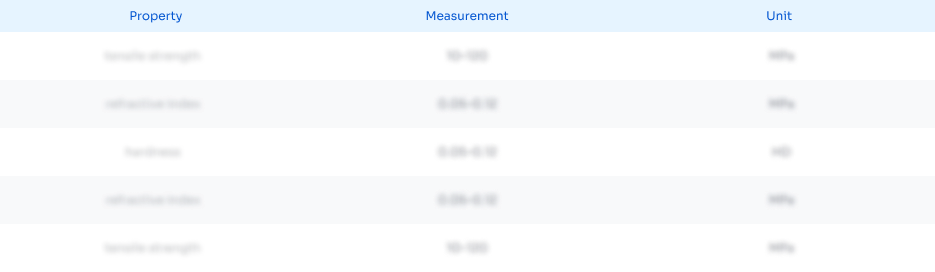
Abstract
Description
Claims
Application Information

- Generate Ideas
- Intellectual Property
- Life Sciences
- Materials
- Tech Scout
- Unparalleled Data Quality
- Higher Quality Content
- 60% Fewer Hallucinations
Browse by: Latest US Patents, China's latest patents, Technical Efficacy Thesaurus, Application Domain, Technology Topic, Popular Technical Reports.
© 2025 PatSnap. All rights reserved.Legal|Privacy policy|Modern Slavery Act Transparency Statement|Sitemap|About US| Contact US: help@patsnap.com