Brushed high-strength abrasion-resistant anticorrosive coating and preparation method
An anti-corrosion coating and high-strength technology, applied in the field of polymers, can solve problems such as increased friction coefficient, shortened service life, and decreased pump efficiency, and achieve low odor, excellent wear resistance, and less human injury.
- Summary
- Abstract
- Description
- Claims
- Application Information
AI Technical Summary
Problems solved by technology
Method used
Image
Examples
Embodiment 1
[0033] A component is made up of the following components by weight:
[0034] 40 parts of bisphenol A epoxy resin, 40 parts of novolak epoxy resin, 10 parts of toughening agent, 5 parts of thinner, 60 parts of ceramic powder, 5 parts of quartz powder, 20 parts of titanium dioxide, 5 parts of fumed silica, 0.1 part of foaming agent, 0.1 part of leveling agent, 0.1 part of wetting and dispersing agent;
[0035] B component is made up of the component of following parts by weight:
[0036] 40 parts of mixed amine curing agent, 2 parts of epoxy accelerator, 2 parts of silane coupling agent;
Embodiment 2
[0038] A component is made up of the following components by weight:
[0039] 60 parts of bisphenol A epoxy resin, 40 parts of novolak epoxy resin, 15 parts of toughening agent, 10 parts of diluent, 100 parts of ceramic powder, 10 parts of quartz powder, 30 parts of titanium dioxide, 10 parts of fumed silica, 0.5 parts of foaming agent, 0.5 parts of leveling agent, 0.5 parts of wetting and dispersing agent;
[0040] B component is made up of the component of following parts by weight:
[0041] Mixed amine curing agent 50 parts, epoxy accelerator 5 parts, silane coupling agent 5 parts;
Embodiment 3
[0043] A component is made up of the following components by weight:
[0044] 40 parts of bisphenol A epoxy resin, 60 parts of novolac epoxy resin, 12 parts of toughening agent, 8 parts of thinner, 80 parts of ceramic powder, 8 parts of quartz powder, 30 parts of titanium dioxide, 10 parts of fumed silica;
[0045] B component is made up of the component of following parts by weight:
[0046] 45 parts of mixed amine curing agent, 3 parts of epoxy accelerator, 3 parts of silane coupling agent;
PUM
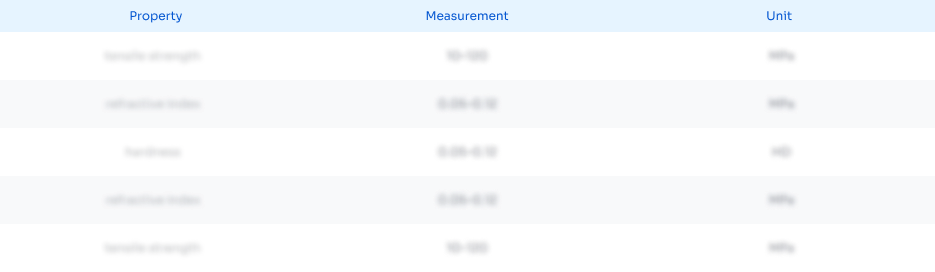
Abstract
Description
Claims
Application Information

- R&D Engineer
- R&D Manager
- IP Professional
- Industry Leading Data Capabilities
- Powerful AI technology
- Patent DNA Extraction
Browse by: Latest US Patents, China's latest patents, Technical Efficacy Thesaurus, Application Domain, Technology Topic, Popular Technical Reports.
© 2024 PatSnap. All rights reserved.Legal|Privacy policy|Modern Slavery Act Transparency Statement|Sitemap|About US| Contact US: help@patsnap.com