Silicon carbide particle reinforced aluminum matrix composite and preparation method thereof
A technology of silicon carbide particles and composite materials, which is applied in the field of silicon carbide particle reinforced aluminum-based composite materials and its preparation, can solve the problems of easy precipitation of coarse grains, reduced mechanical properties and thermal conductivity of composite materials, and extremely high atmosphere requirements. The effect of improving mechanical properties and thermal conductivity, improving metallographic structure and improving mechanical properties
- Summary
- Abstract
- Description
- Claims
- Application Information
AI Technical Summary
Problems solved by technology
Method used
Image
Examples
preparation example Construction
[0016] The present invention also provides a method for preparing a silicon carbide particle-reinforced aluminum-based composite material, the method comprising the following steps:
[0017] S1 mixes silicon carbide micropowder and paraffin-based binder, and adopts hot die-casting to form a SiC skeleton prepared after debinding and sintering;
[0018] S2 Accurately weigh aluminum, magnesium, silicon, and rare earth, and prepare aluminum alloy blocks of appropriate shape and size by vacuum induction melting, gravity casting or rolling;
[0019] S3 put the aluminum alloy block on the silicon carbide skeleton and put them together into the atmosphere furnace for pressureless impregnation, pass through nitrogen protection, heat up to 850-950°C, take it out after keeping it for 1-4h, and cool it to room temperature with nitrogen to obtain composite material.
[0020] The paraffin-based binder is a mixture formed by dissolving the binder in paraffin.
[0021] The more specific ste...
Embodiment 1
[0028] (1) Weigh silicon carbide micropowder and paraffin-based binder, pour the two into a blender and mix for 2 hours at 130°C;
[0029] (2) Pour the uniformly mixed slurry into a hot die-casting machine for hot die-casting at a hot die-casting temperature of 150°C, then water-cool the mold and demould to obtain a green body of SiC and paraffin;
[0030] (3) Place the demoulded SiC and paraffin body on a porous alumina plate, and carry out debinding and sintering in the debinding furnace. Specifically, the furnace temperature is first raised to 200°C, and the paraffin is removed by keeping the temperature for 1 hour, and then Raise the furnace temperature to 600°C, keep the temperature for 1 hour to remove the adhesive, and finally raise the temperature to 1200°C, keep the temperature for 1 hour for sintering. Finally, after cooling with the furnace, the required SiC skeleton is obtained;
[0031] (4) Weigh aluminum: 88.5 parts by weight, silicon: 8.0 parts by weight, magne...
Embodiment 2
[0034] (1) Weigh silicon carbide micropowder and paraffin-based binder, pour the two into a blender and mix for 2 hours at 130°C;
[0035](2) Pour the uniformly mixed slurry into a hot die-casting machine for hot die-casting at a hot die-casting temperature of 150°C, then water-cool the mold and demould to obtain a green body of SiC and paraffin;
[0036] (3) Place the demoulded SiC and paraffin body on a porous alumina plate, and carry out debinding and sintering in the debinding furnace. Specifically, the furnace temperature is first raised to 200°C, and the paraffin is removed by keeping the temperature for 1 hour, and then Raise the furnace temperature to 600°C, keep the temperature for 1 hour to remove the adhesive, and finally raise the temperature to 1200°C, keep the temperature for 1 hour for sintering. Finally, after cooling with the furnace, the required SiC skeleton is obtained;
[0037] (4) Weighing aluminum: 88.5 parts by weight, silicon: 8.0 parts by weight, mag...
PUM
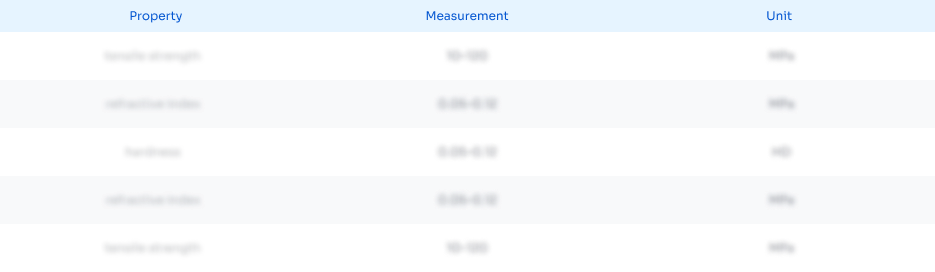
Abstract
Description
Claims
Application Information

- R&D Engineer
- R&D Manager
- IP Professional
- Industry Leading Data Capabilities
- Powerful AI technology
- Patent DNA Extraction
Browse by: Latest US Patents, China's latest patents, Technical Efficacy Thesaurus, Application Domain, Technology Topic, Popular Technical Reports.
© 2024 PatSnap. All rights reserved.Legal|Privacy policy|Modern Slavery Act Transparency Statement|Sitemap|About US| Contact US: help@patsnap.com