Method for controlling center porosity defect of bearing steel
A technology of center loosening and control method, which is applied in the direction of rolling mill control devices, metal rolling, manufacturing tools, etc., can solve the problems affecting the internal quality and service performance of bearing steel, high cooling intensity, large interface temperature gradient, etc., to improve the internal Effects of quality and performance, improvement of quality pass rate, and improvement of quality level
- Summary
- Abstract
- Description
- Claims
- Application Information
AI Technical Summary
Problems solved by technology
Method used
Examples
Embodiment 1
[0028] 1. Continuous casting process control:
[0029] The secondary cooling water of continuous casting adopts a weak cooling system, and the specific water volume is controlled at 15m 3 / Ton of steel, the amount of compressed air and water allocated in each area is:
[0030] area Cooling water distribution ratio (%)Air supply (m 3 / h) Mold foot roller26100 Support the upper part of the guide23.5100 Support the lower part of the guide position16100 Arc section21.5200 Two arcs 13100
[0031] Using low superheat and low drawing speed, considering that low superheat and low drawing speed are prone to flocculation accidents, which is not conducive to continuous casting of multiple furnaces, so the superheat is controlled at 12℃ and the drawing speed is controlled at 0.54m / min.
[0032] 2. Tundish baking system:
[0033] The tundish is baked on a low fire for 5 hours and then automatically baked for 2 hours, and the maximum baking temperature reaches 1450°C.
[0034] 3. Electromagn...
Embodiment 2
[0043] 1. Continuous casting process control:
[0044] The secondary cooling water of continuous casting adopts a weak cooling system, and the specific water volume is controlled at 15m 3 Per ton of steel, the distribution amount of compressed air and water in each area is:
[0045] area Cooling water distribution ratio (%)Air supply (m 3 / h) Mold foot roller26100 Support the upper part of the guide23.5100 Support the lower part of the guide position16100 Arc section21.5200 Two arcs 13100
[0046] Using low superheat and low drawing speed, considering that low superheat and low drawing speed are prone to flocculation accidents, which is not conducive to continuous casting of multiple furnaces, so the superheat is controlled at 18℃ and the drawing speed is controlled at 0.56m / min.
[0047] 2. Tundish baking system:
[0048] The tundish is baked on a low fire for 3.5 hours and then automatically baked for 2.5 hours. The maximum baking temperature reaches 1460°C.
[0049] 3. Elect...
PUM
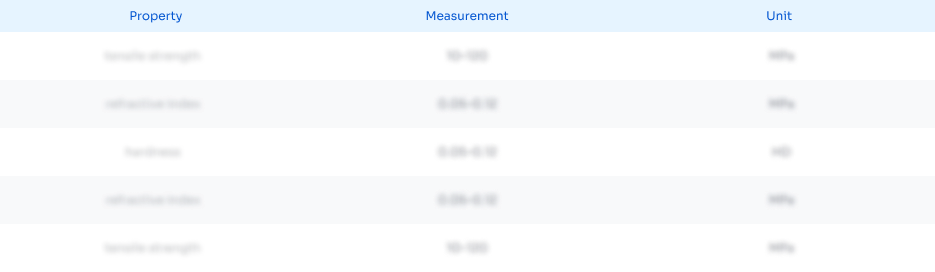
Abstract
Description
Claims
Application Information

- R&D
- Intellectual Property
- Life Sciences
- Materials
- Tech Scout
- Unparalleled Data Quality
- Higher Quality Content
- 60% Fewer Hallucinations
Browse by: Latest US Patents, China's latest patents, Technical Efficacy Thesaurus, Application Domain, Technology Topic, Popular Technical Reports.
© 2025 PatSnap. All rights reserved.Legal|Privacy policy|Modern Slavery Act Transparency Statement|Sitemap|About US| Contact US: help@patsnap.com