Ceramic light insulation decorative exterior wall tile and productive process
A production process and lightweight technology, applied in thermal insulation, ceramic products, building components, etc., can solve the problems of aggravating the risk of falling off, easy falling off, high density of ceramic exterior wall bricks, etc., to reduce construction procedures and construction time, excellent Insulation performance, wide application effect
- Summary
- Abstract
- Description
- Claims
- Application Information
AI Technical Summary
Problems solved by technology
Method used
Examples
Embodiment 1
[0027] Green body formula: 20 parts of clay, 22 parts of quartz sand tailings, 22 parts of low-temperature porcelain sand, 35 parts of lithium porcelain stone, 5 parts of talc, 5 parts of green silicon carbide powder (SiC content ≥ 90 parts), 2 parts of dark red material , 33 parts of water. Among them, the ore and clay are calculated on a dry basis and actually contain water, so the water content of the mud after ball milling can still be controlled to 33-35%. Of course, it can also be adjusted by adding or subtracting water, the same below.
[0028] Production steps: a. All raw materials are mixed evenly according to the ratio, ball milled to 3% on a 250-mesh sieve, and the moisture content of the mud is controlled at 33%; b. Drying to obtain a powder with a moisture content of 6%; c. The molding machine is pressed and formed, and the setting The working pressure is 16MPa; d, drying until the moisture content of the green body is lower than 1%; e, firing; the maximum firing ...
Embodiment 2
[0030] Green body formula: 18 parts of clay, 20 parts of quartz sand tailings, 20 parts of low-temperature porcelain sand, 33 parts of lithium porcelain stone, 3 parts of talc, 3 parts of green silicon carbide powder (SiC content ≥ 90 parts), 3 parts of yellow pigment , 34 parts of water.
[0031] Production steps: a. All raw materials are mixed evenly according to the ratio, ball milled to 1% on a 250 mesh sieve, and the moisture content of the mud is controlled at 33%; b. Drying to obtain a powder with a moisture content of 6%; c. The molding machine is pressed and formed, and the setting The working pressure is 16MPa; d, drying until the moisture content of the green body is lower than 1%; e, firing; the maximum firing temperature is 1170°C, and the firing cycle is 40 minutes. Product 2 was obtained.
Embodiment 3
[0033] Green body formula: 15 parts of clay, 22 parts of quartz sand tailings, 15 parts of low-temperature porcelain sand, 30 parts of lithium porcelain stone, 3 parts of talc, 4 parts of green silicon carbide powder (SiC content ≥ 90 parts), 3 parts of gray pigment , 35 parts of water.
[0034] Production steps: a. All raw materials are mixed evenly according to the ratio, ball milled to 250 mesh sieve to account for 2%, and the moisture content of the mud is controlled at 35%; b. Drying to obtain powder with a moisture content of 6.5%; c. Forming machine pressing and molding, setting The working pressure is 20MPa; d, drying until the moisture content of the green body is lower than 1%; e, firing; the maximum firing temperature is 1220°C, and the firing cycle is 45 minutes. Product 3 was obtained.
PUM
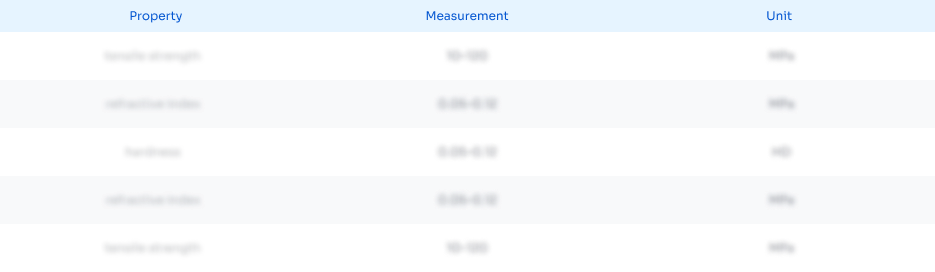
Abstract
Description
Claims
Application Information

- R&D
- Intellectual Property
- Life Sciences
- Materials
- Tech Scout
- Unparalleled Data Quality
- Higher Quality Content
- 60% Fewer Hallucinations
Browse by: Latest US Patents, China's latest patents, Technical Efficacy Thesaurus, Application Domain, Technology Topic, Popular Technical Reports.
© 2025 PatSnap. All rights reserved.Legal|Privacy policy|Modern Slavery Act Transparency Statement|Sitemap|About US| Contact US: help@patsnap.com