Preparation method of Si-C-N ceramic precursor
A technology of ceramic precursor and si-c-n, which is applied in the synthesis field of Si-C-N ceramic precursor, can solve the problems of increasing reaction procedures, difficulty in purifying polysilazane, inevitable by-product chloramine salt, etc., and achieves reaction efficiency High, diverse raw material compounds, high product purity effect
- Summary
- Abstract
- Description
- Claims
- Application Information
AI Technical Summary
Problems solved by technology
Method used
Image
Examples
Embodiment 1
[0022] Dissolve 13.2g of dimethyldichlorosilane in 100mL of n-hexane to obtain oil phase solution I, dissolve 6g of ethylenediamine in 100 ml of 80g / L NaOH aqueous solution to obtain water phase solution II, drop water phase solution II to the oil In phase solution I, react at -25°C for 4 hours, heat up to 40°C, react for 8 hours, separate the liquid, and rotate the oil phase at 70°C for 1 hour to obtain 6.8 g of low-viscosity liquid polysilazane with a yield of 93%. The polysilazane was heat-treated at 50° C. for 72 hours in a vacuum atmosphere to obtain a solid precursor.
[0023] The FT-IR spectra of polysilazane and precursor are as follows figure 1 Curves a and b in. 3380-3330cm in map a -1 The absorption peak at shows that the ammonolysis of chlorosilane occurs, and the product is polysilazane.
Embodiment 2
[0025] 6.6g of dimethyldichlorosilane and 7.25g of methylvinyldichlorosilane were dissolved in 100mL of dichloromethane to obtain oil phase solution I, 13.6g of NH 3 Dissolve in 100ml of 160g / L NaOH aqueous solution to obtain water phase solution II, drop water phase solution II into oil phase solution I, react at 0°C for 4 hours, heat up to 20°C, react for 8 hours, separate liquid, rotate at 70°C The oil phase was evaporated for 1 hour to obtain 7.2 g of low-viscosity liquid polysilazane with a yield of 91%. The polysilazane in N 2 Protective heat treatment at 250°C for 12 hours to obtain a solid precursor.
[0026] The infrared spectra of polysilazane and precursor are as follows figure 2 Curves a and b in.
Embodiment 3
[0028] 14.45g of methylvinyldichlorosilane was dissolved in 100mL of xylene to obtain oil phase solution I, 15.0g of tetramethyldisilazane was dissolved in 100 ml of 112g / L KOH aqueous solution to obtain water phase solution II, and water was added dropwise Phase solution II was transferred to oil phase solution I, reacted at 0°C for 4 hours, then heated to 20°C, reacted for 8 hours, separated the liquid, and evaporated the oil phase at 100°C for 1 hour to obtain 15.7 g of viscous liquid polysilazane. Yield 90%. The polysilazane was heat-treated at 170° C. for 24 hours under the protection of Ar to obtain a solid precursor.
[0029] The infrared spectra of polysilazane and precursor are as follows image 3 Curves a and b in.
PUM
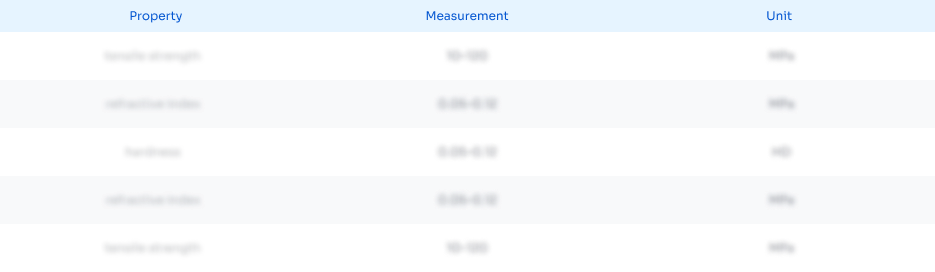
Abstract
Description
Claims
Application Information

- R&D
- Intellectual Property
- Life Sciences
- Materials
- Tech Scout
- Unparalleled Data Quality
- Higher Quality Content
- 60% Fewer Hallucinations
Browse by: Latest US Patents, China's latest patents, Technical Efficacy Thesaurus, Application Domain, Technology Topic, Popular Technical Reports.
© 2025 PatSnap. All rights reserved.Legal|Privacy policy|Modern Slavery Act Transparency Statement|Sitemap|About US| Contact US: help@patsnap.com