Method for preparing ethyl alcohol by hydrogenation of acetate
A technology of acetate and methyl acetate, which is applied in the field of hydrogenation of acetate to prepare ethanol, can solve the problems of no catalyst preparation method and reduced hydrogenation activity, and achieve the avoidance of separation and purification, promotion of hydrogenation reaction, and preparation process simple effect
- Summary
- Abstract
- Description
- Claims
- Application Information
AI Technical Summary
Problems solved by technology
Method used
Image
Examples
Embodiment 1
[0038] Dissolve 6.8g of crystalline copper nitrate and 57ml of water in a three-necked flask, stir evenly at room temperature, and then drop in 20% NaOH aqueous solution until pH=12 to form a slurry.
[0039] 4.18g SiO 2 Add the powder to the above slurry, stir evenly, then heat up to 80-90°C, age for 4 hours, filter, and wash. Dry at 120°C for 12h, and bake at 450°C for 3h. Obtain the CuO whose Cu oxide mass accounts for 35wt% of the total mass of the catalyst x / SiO 2 Catalyst, abbreviated as 35Cu / SiO 2 .
Embodiment 2
[0041] 1.37g manganese nitrate aqueous solution (manganese nitrate mass percentage composition 50%) is dissolved in the beaker with 25ml water, adds 4g SiO 2 Stir the powder evenly, and when the solution is volatilized and nearly dry, transfer it to an oven for 12 hours at 120°C to obtain MnO y / SiO 2 sample.
[0042] Dissolve 6.8g of crystalline copper nitrate and 57ml of water in a three-necked flask, stir evenly at room temperature, and then drop in 20% NaOH aqueous solution until pH=12 to form a slurry.
[0043] 4.18 g of MnO prepared above y / SiO 2 Add the powder to the above slurry, stir evenly, then heat up to 80-90°C, age for 4 hours, filter, and wash. Dry at 120°C for 12h, and bake at 450°C for 3h to obtain CuO x -MnO y / SiO 2 catalyst. Wherein the Cu oxide mass accounts for 35wt% of the total mass of the catalyst, and the additive manganese oxide MnO y The mass accounts for 5wt% of the total mass of the catalyst, abbreviated as 35Cu-5Mn / SiO 2 .
Embodiment 3
[0045] 1.05g crystalline zinc nitrate (Zn(NO 3 ) 2 ·6H 2 O) dissolve in the beaker with 20ml water, add 4g SiO 2 Stir the powder evenly, and when the solution is volatilized and nearly dry, transfer it to an oven and bake at 120°C for 12 hours to obtain ZnO y / SiO 2 sample.
[0046] Dissolve 6.8g of crystalline copper nitrate and 57ml of water in a three-necked flask, stir evenly at room temperature, and then drop in 20% NaOH aqueous solution until pH=12 to form a slurry.
[0047] 4.3 g ZnO prepared above y / SiO 2 Add the powder to the above slurry, stir evenly, then heat up to 80-90°C, age for 4 hours, filter, and wash. Dry at 120°C for 12h, and bake at 450°C for 3h to obtain CuO x -ZnO y / SiO 2 catalyst. Among them, the mass of Cu oxide accounts for 35wt% of the total mass of the catalyst, and the mass of zinc oxide as an auxiliary agent accounts for 4wt% of the total mass of the catalyst, which is abbreviated as 35Cu-4Zn / SiO 2 .
PUM
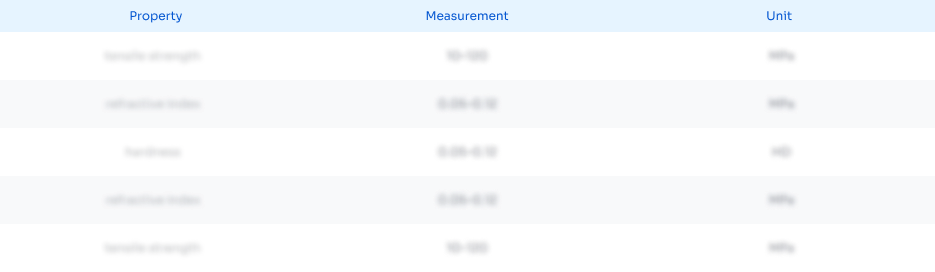
Abstract
Description
Claims
Application Information

- R&D
- Intellectual Property
- Life Sciences
- Materials
- Tech Scout
- Unparalleled Data Quality
- Higher Quality Content
- 60% Fewer Hallucinations
Browse by: Latest US Patents, China's latest patents, Technical Efficacy Thesaurus, Application Domain, Technology Topic, Popular Technical Reports.
© 2025 PatSnap. All rights reserved.Legal|Privacy policy|Modern Slavery Act Transparency Statement|Sitemap|About US| Contact US: help@patsnap.com