Low-temperature preparation method of oxidapatite-structure lanthanum germanium acid electrolyte material powder body
An electrolyte material and oxyapatite technology are applied in the field of medium temperature solid oxide fuel cell electrolyte material preparation to achieve the effects of less energy consumption, low preparation temperature and simple preparation process
- Summary
- Abstract
- Description
- Claims
- Application Information
AI Technical Summary
Problems solved by technology
Method used
Image
Examples
Embodiment 1
[0028] 5.8463g lanthanum oxide (La 2 o 3 ) and 2.4136g germanium oxide (GeO 2 ) (molar ratio is 9.33: 12) is put into 250ml agate ball mill jar, then 24.7797g sodium chloride (NaCl) (initial reaction raw material total mass and sodium chloride mass ratio is 1: 3) is put into agate ball mill jar , and inject an appropriate amount of absolute ethanol; the mixture is ball-milled with a planetary ball mill, the speed of the ball mill is 400 rpm, and the time is 8 hours; the mixture of the ball-milled raw material and molten salt is imported into a 250ml beaker and put into a drying box Drying inside, the drying temperature is 110°C, and the drying time is 24 hours; the mixture of dried raw materials and molten salt is placed in a muffle furnace with a crucible, and sintered at a temperature of 900°C for 4 hours; sintering After La 9.33 Ge 6 o 26 Electrolyte powder and sodium chloride mixture, use deionized water to wash La 9.33 Ge 6 o 26 The sodium chloride mixed in the el...
Embodiment 2
[0030] 5.9716g lanthanum oxide (La 2 o 3 ) and 2.4136g germanium oxide (GeO 2 ) (mol ratio is 9.53: 12) is put into 250ml agate ball mill jar, then 25.1556g sodium chloride (NaCl) (raw material total mass and sodium chloride mass ratio is 1: 3) is put into agate ball mill jar, and Inject an appropriate amount of absolute ethanol; use a planetary ball mill to carry out ball milling on the mixture, the speed of ball milling is 400 rpm, and the time is 8 hours; the mixture of ball milled raw materials and molten salt is imported into a 250ml beaker, and put into a drying oven for drying dry, the drying temperature is 110°C, and the drying time is 24 hours; the mixture of dried raw materials and molten salt is placed in a muffle furnace with a crucible, and sintered at a temperature of 900°C for 4 hours; the sintered La 9.53 Ge 6 o 26.3 Electrolyte powder and sodium chloride mixture, use deionized water to wash La 9.53 Ge 6 o 26.3 The sodium chloride mixed in the electroly...
Embodiment 3
[0032] 5.8463g lanthanum oxide (La 2 o 3 ) and 2.4136g germanium oxide (GeO 2 ) (mol ratio is 9.33: 12) is put into 250ml agate ball mill jar, then 24.7797g sodium chloride (NaCl) (raw material total mass and sodium chloride mass ratio is 1: 3) is put into agate ball mill jar, and Inject an appropriate amount of absolute ethanol; use a planetary ball mill to carry out ball milling on the mixture, the speed of ball milling is 400 rpm, and the time is 8 hours; the mixture of ball milled raw materials and molten salt is imported into a 250ml beaker, and put into a drying oven for drying dry, the drying temperature is 110°C, and the drying time is 24 hours; the mixture of dried raw materials and molten salt is put into a muffle furnace with a crucible, and sintered at a temperature of 1000°C for 4 hours; the sintered La 9.33 Ge 6 o 26 Electrolyte powder and sodium chloride mixture, use deionized water to wash La 9.33 Ge 6 o 26 The sodium chloride mixed in the electrolyte p...
PUM
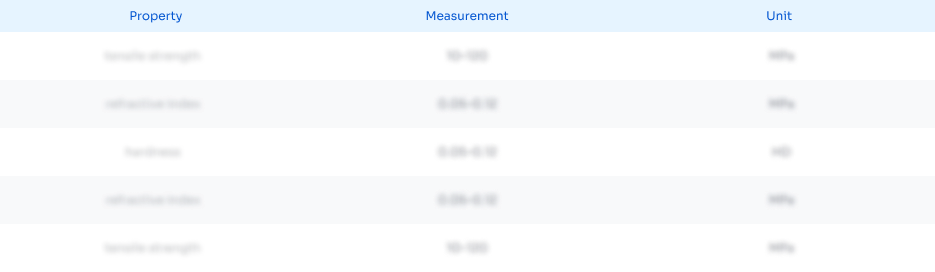
Abstract
Description
Claims
Application Information

- Generate Ideas
- Intellectual Property
- Life Sciences
- Materials
- Tech Scout
- Unparalleled Data Quality
- Higher Quality Content
- 60% Fewer Hallucinations
Browse by: Latest US Patents, China's latest patents, Technical Efficacy Thesaurus, Application Domain, Technology Topic, Popular Technical Reports.
© 2025 PatSnap. All rights reserved.Legal|Privacy policy|Modern Slavery Act Transparency Statement|Sitemap|About US| Contact US: help@patsnap.com