Foam metal carrier with high specific surface area and preparation process thereof
A high specific surface area, foam metal technology, applied in catalyst carriers, physical/chemical process catalysts, chemical instruments and methods, etc., can solve the problem of reduced strength, no patent application same as this patent, and calciner cost process materials High cost problem, to achieve the effect of optimizing material cost, good covering ability, and high practical value
- Summary
- Abstract
- Description
- Claims
- Application Information
AI Technical Summary
Problems solved by technology
Method used
Image
Examples
Embodiment 1
[0019] Take a square metal foam sample made by iron-nickel electrodeposition with a porosity of 10ppi (the number of pores per inch, the same below), a size of 100×100mm, and a thickness of 25mm. Dissolve 100g of asphalt in 200g of kerosene, then weigh 50g of industrial nano-titanium dioxide powder with an average particle size of 100nm and add it to the mixed solution, and finally add 650g of kerosene to dilute and start stirring. After 60 minutes, stir the foam metal sample in the mixed solution Dip coating at the same time, take out after 5~10min and remove the excess mixture, make it dry and repeat the dip coating twice; put the dried and completely coated foam metal sample into a high temperature furnace and pass in argon as a protection atmosphere, the furnace was heated to 550°C for calcination, the temperature was kept for 240 minutes, then the heating was stopped and the furnace was cooled to room temperature to obtain a metal foam sample with a hard carbon film on the...
Embodiment 2
[0021] Take a square metal foam sample with a porosity of 10ppi, a size of 100×100mm, and a thickness of 25mm made by iron-nickel electrodeposition. Dissolve 150g of asphalt in 300g of kerosene, then weigh 50g of industrial nano-titanium dioxide powder with an average particle size of 100nm and add it to the mixed solution, and finally add 500g of kerosene to dilute and start stirring. After 60 minutes, stir the foam metal sample in the mixed solution dip-coating at the same time, take out after 5~10min and remove the excess mixture, make it dry and repeat the dip-coating 3 times; put the dried and completely coated foam metal sample into a high-temperature furnace and pass in argon as a protection atmosphere, the furnace was heated to 550°C for calcination, the temperature was kept for 240 minutes, then the heating was stopped and the furnace was cooled to room temperature to obtain a metal foam sample with a hard carbon film on the surface. Free fall on the concrete floor at...
Embodiment 3
[0023] Take a square metal foam sample with a porosity of 10ppi, a size of 100×100mm, and a thickness of 25mm made by iron-nickel electrodeposition. Dissolve 100g of asphalt in 200g of kerosene, then weigh 100g of industrial nano-titanium dioxide powder with an average particle size of 100nm and add it to the mixed solution, and finally add 600g of kerosene to dilute and start stirring. After 60 minutes, stir the foam metal sample in the mixed solution dip-coating at the same time, take out after 5~10min and remove the excess mixture, make it dry and repeat the dip-coating 4 times; put the dried and completely coated foam metal sample into a high-temperature furnace and pass in argon as a protection atmosphere, the furnace was heated to 550°C for calcination, the temperature was kept for 240 minutes, then the heating was stopped and the furnace was cooled to room temperature to obtain a metal foam sample with a hard carbon film on the surface. Free fall on the concrete floor a...
PUM
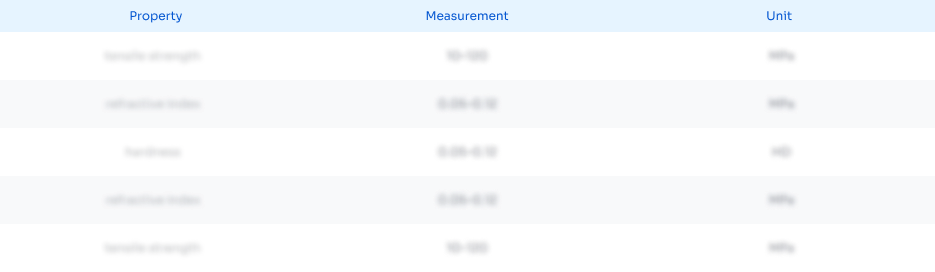
Abstract
Description
Claims
Application Information

- Generate Ideas
- Intellectual Property
- Life Sciences
- Materials
- Tech Scout
- Unparalleled Data Quality
- Higher Quality Content
- 60% Fewer Hallucinations
Browse by: Latest US Patents, China's latest patents, Technical Efficacy Thesaurus, Application Domain, Technology Topic, Popular Technical Reports.
© 2025 PatSnap. All rights reserved.Legal|Privacy policy|Modern Slavery Act Transparency Statement|Sitemap|About US| Contact US: help@patsnap.com