Process for producing fuel alcohol by adopting straw lignocellulose as raw material
A technology of lignocellulose and fuel ethanol, applied in biofuels, methods based on microorganisms, microorganisms, etc., can solve the problems of hydrolysis and saccharification technology with many by-products, increased process complexity and cost, and long time required for hydrolysis of concentrated sulfuric acid. , to achieve good pretreatment effect, high utilization rate of raw materials, and increase the effect of surface area
- Summary
- Abstract
- Description
- Claims
- Application Information
AI Technical Summary
Problems solved by technology
Method used
Image
Examples
Embodiment 1
[0031] (1) Crushing of wheat straw
[0032] Use a crusher to crush the wheat straw to 80 meshes, and dry and store at 55°C;
[0033] (2) 1.0% NaOH solution pretreatment
[0034] Weigh 200 g of crushed and dried wheat straw powder, add 4 L of NaOH solution with a mass fraction of 1.0% to it, control the solid-liquid ratio to 1:20, stir evenly; and keep the temperature at 121 ° C and a pressure of 0.2 MPa for 50 min, After cooling to room temperature, add an appropriate amount of distilled water for centrifugation, set the speed of the centrifuge to 4000r / min, and centrifuge for 15min each time. The supernatant after this centrifugation can be reused after adding an appropriate amount of NaOH. The precipitate was washed with distilled water until the centrifuged supernatant was neutral; the centrifuged wheat straw precipitate was dried at 105°C. After drying, use a crusher to crush to 80 mesh, and store at 55°C until use.
[0035] The changes of lignin, hemicellulose and cel...
Embodiment 2
[0042] (1) Crushing of straw straw
[0043] Use a crusher to crush the straw-like lignocellulose to 80 meshes, and dry and store at 55°C;
[0044] (2) 1.0% NaOH solution pretreatment
[0045] Weigh 2.4Kg of crushed and dried rice straw powder, add 48L of NaOH solution with a mass fraction of 1.0% to it, control the solid-liquid ratio to 1:20, stir evenly; and keep at 121°C and a pressure of 0.2MPa for 50min , after cooling to room temperature, add an appropriate amount of distilled water to centrifuge, set the speed of the centrifuge to 4000r / min, and centrifuge for 15min each time. The supernatant after this centrifugation can be reused after adding an appropriate amount of NaOH. The precipitate was washed with distilled water until the centrifuged supernatant was neutral; the centrifuged rice straw precipitate was dried at 105°C. After drying, use a crusher to crush to 80 mesh, and store at 55°C until use.
[0046] The changes of lignin, hemicellulose and cellulose compo...
PUM
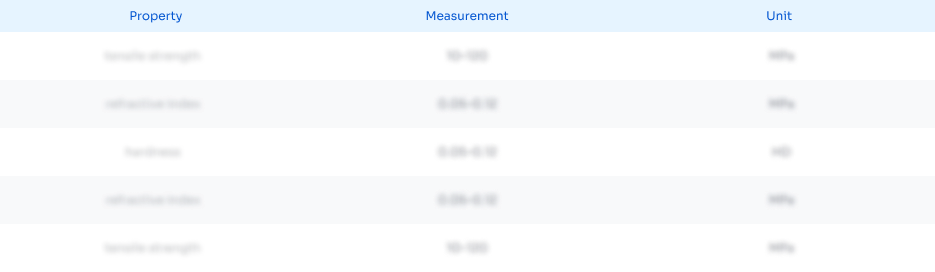
Abstract
Description
Claims
Application Information

- R&D
- Intellectual Property
- Life Sciences
- Materials
- Tech Scout
- Unparalleled Data Quality
- Higher Quality Content
- 60% Fewer Hallucinations
Browse by: Latest US Patents, China's latest patents, Technical Efficacy Thesaurus, Application Domain, Technology Topic, Popular Technical Reports.
© 2025 PatSnap. All rights reserved.Legal|Privacy policy|Modern Slavery Act Transparency Statement|Sitemap|About US| Contact US: help@patsnap.com