Amorphous indium zinc oxide/carbon nanotube composite film transistor and preparation method thereof
A carbon nanotube composite and thin-film transistor technology, which is applied in the direction of transistors, semiconductor/solid-state device manufacturing, semiconductor devices, etc., can solve the problems of large-area preparation of high-mobility polysilicon materials, large off-state current of TFT, and gap in flexibility. , to achieve excellent mechanical stability, high mobility, and low cost
- Summary
- Abstract
- Description
- Claims
- Application Information
AI Technical Summary
Problems solved by technology
Method used
Image
Examples
Embodiment 1
[0029] (1) Dissolve 0.285 g of indium nitrate tetrahydrate and 0.165 g of zinc acetate dihydrate in 50 mL of ethylene glycol methyl ether, and add 0.46 mL of ethanolamine as a stabilizer, stir for 2 h, and have a thickness of 300 nm for pre-grown SiO 2 The highly doped Si sheet of the insulating layer was ultrasonically cleaned, and then spin-coated with a spin coater at a speed of 2400 rpm, and then baked at 200 °C for 10 min in the atmosphere, and then spin-coated on the basis of the previous layer. layer to obtain a composite film with a thickness of 60 nm, and finally thermally annealed at 400 °C for 40 min in the atmosphere to obtain a composite film material; (2) using ultraviolet lithography technology, through the first mask, using wet etching (10 wt% dilute hydrochloric acid) for 2 min, the film was divided into small pieces with an area size of 1 mm × 1 mm to reduce the parasitic capacitance and leakage current introduced during the transistor fabrication process. T...
Embodiment 2
[0031] (1) Dissolve 9 mg of carbon nanotubes (CNTs) in 100 mL of ethylene glycol methyl ether by sonication, and suspend them evenly for 4 h to serve as mother liquor for later use. Then 0.285 g of indium nitrate tetrahydrate and 0.165 g of zinc acetate dihydrate were dissolved in 50 mL of ethylene glycol methyl ether, and 0.46 mL of ethanolamine was added as a stabilizer, stirred for 2 h, and 50 mL of carbon nanotube mother liquor was added and ultrasonicated Disperse for 30 min, and then spin-coat at 2400 rpm on pre-grown SiO with a thickness of 300 nm 2 On the insulating layer, after baking at 200 °C for 10 min in the atmosphere, spin-coat another layer on the basis of the previous layer to obtain a composite film with a thickness of 60 nm, and finally thermally anneal at 400 °C for 40 min in the atmosphere to obtain IZO / CNT composite film material; (2) Using ultraviolet lithography technology, through the first mask, using wet etching (10 wt% dilute hydrochloric acid as e...
Embodiment 3
[0035] (1) Dissolve 9 mg of carbon nanotubes (CNTs) in 100 mL of ethylene glycol methyl ether by sonication, and suspend them evenly for 4 h to serve as mother liquor for later use. Then 0.285 g of indium nitrate tetrahydrate and 0.165 g of zinc acetate dihydrate were dissolved in 50 mL of ethylene glycol methyl ether, and 0.46 mL of ethanolamine was added as a stabilizer, stirred for 2 h, 50 mL of carbon nanotube mother liquor was added and Ultrasonic dispersion was performed for 30 min, and then spin-coated on pre-grown SiO with a thickness of 300 nm at a speed of 2400 rpm. 2 On the insulating layer, after baking at 200 °C for 10 min in the atmosphere, spin-coat another layer on the basis of the previous layer to obtain a composite film with a thickness of 60 nm, and finally thermally anneal at 300 °C for 40 min in the atmosphere to obtain IZO / CNT composite film material; (2) Using ultraviolet lithography technology, through the first mask, using wet etching (10 wt% dilute ...
PUM
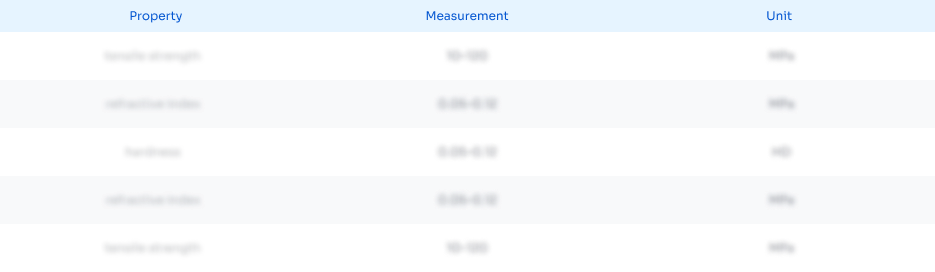
Abstract
Description
Claims
Application Information

- Generate Ideas
- Intellectual Property
- Life Sciences
- Materials
- Tech Scout
- Unparalleled Data Quality
- Higher Quality Content
- 60% Fewer Hallucinations
Browse by: Latest US Patents, China's latest patents, Technical Efficacy Thesaurus, Application Domain, Technology Topic, Popular Technical Reports.
© 2025 PatSnap. All rights reserved.Legal|Privacy policy|Modern Slavery Act Transparency Statement|Sitemap|About US| Contact US: help@patsnap.com