Phosphorous catalyst for synthesizing methyl mercaptan and preparation method thereof
A technology of methyl mercaptan and catalyst, which is applied in the field of catalysts, can solve the problems of increasing post-treatment procedures, difficult removal, low selectivity, etc., and achieve the effects of improving pore structure properties, high conversion rate, and reducing reaction temperature
- Summary
- Abstract
- Description
- Claims
- Application Information
AI Technical Summary
Problems solved by technology
Method used
Image
Examples
Embodiment 1
[0019] Embodiment 1: Take by weighing 73.68g aluminum nitrate nonahydrate, dissolve with 200.0ml distilled water, be made into the Al(NO of 0.5mol / L 3 ) 3 solution, heated to 70°C under constant stirring, and added 0.5mL PEG400 and 0.18g (NH 4 ) 2 HPO 4 , increase the stirring speed, add 25% ammonia water drop by drop to form a gel, adjust the pH value to 6.5, continue stirring for 1 hour, aging at room temperature for 24 hours, drying in an oven at 80°C for 24 hours, and calcining in a muffle furnace at 550°C for 3 hours. 1% phosphorus modified γ-Al 2 o 3 (A).
[0020] The activity evaluation of the catalyst was carried out on a fixed-bed reaction system. The loading amount of the catalyst was 1mL, the particle size was 30-60 mesh, and the molar ratio of hydrogen sulfide to methyl sulfide was 4; the space velocity of the reactant material was 1000h -1 , the reaction pressure of the reaction system is 0.5MPa, the reaction temperature is 320 and 360°C, the conversion rate...
Embodiment 2、3
[0023] Embodiment 2,3: the 0.18g (NH 4 ) 2 HPO 4 Respectively changed to 0.54g (NH 4 ) 2 HPO 4 and 0.90g (NH 4 ) 2 HPO 4 , the rest of the preparation method is the same as in Example 3 to obtain 3% phosphorus-modified γ-Al 2 o 3 and 5% phosphorus-modified γ-Al 2 o 3 (A). The activity evaluation of the catalyst is the same as in Example 1, and the results are shown in Table 1.
Embodiment 4
[0025] Embodiment 4: Weigh 47.28g aluminum chloride hexahydrate, dissolve with 200.0ml distilled water, and make 0.5mol / L AlCl 3 solution, heated to 70°C under constant stirring, and added 0.5mL PEG400 and 0.18g (NH 4 ) 2 HPO 4 , increase the stirring rate, add 25% ammonia water dropwise to form a gel, adjust the pH value to 6.5, continue stirring for 1 hour, aging at room temperature for 24 hours, drying in an oven at 80°C for 24 hours, and calcining at 500°C for 5 hours. 1% phosphorus modified γ-Al 2 o 3 (B). The activity evaluation of the catalyst is the same as in Example 1, and the results are shown in Table 2.
[0026] Catalyst composition and activity evaluation result of table 2 embodiment 4~8 and comparative example 2
[0027]
PUM
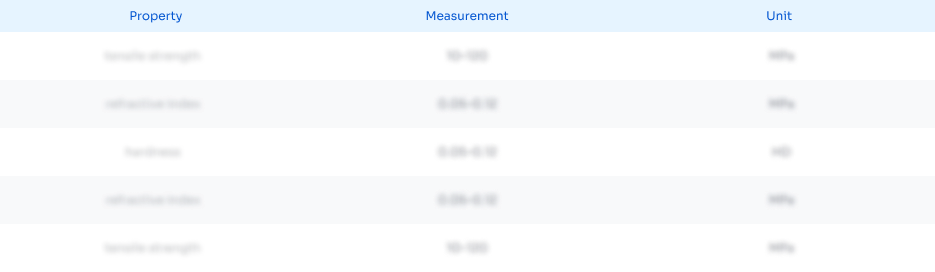
Abstract
Description
Claims
Application Information

- Generate Ideas
- Intellectual Property
- Life Sciences
- Materials
- Tech Scout
- Unparalleled Data Quality
- Higher Quality Content
- 60% Fewer Hallucinations
Browse by: Latest US Patents, China's latest patents, Technical Efficacy Thesaurus, Application Domain, Technology Topic, Popular Technical Reports.
© 2025 PatSnap. All rights reserved.Legal|Privacy policy|Modern Slavery Act Transparency Statement|Sitemap|About US| Contact US: help@patsnap.com