Smelting furnace
A furnace and hearth technology, which is applied in the field of kiln equipment and metallurgical equipment, can solve the problems of increasing raw material costs, inability to extract precious metals, and energy waste, so as to reduce environmental pollution and energy waste, realize the thorough utilization of resources, and reduce radiation. The effect of source pollution
- Summary
- Abstract
- Description
- Claims
- Application Information
AI Technical Summary
Problems solved by technology
Method used
Image
Examples
Embodiment Construction
[0026] The main structure of the present invention is: smelting furnace, including: refractory material 1, heat preservation material 2, fan 3, pipeline 4, valve 5, ignition device 6, fuel supply device 7 and temperature measuring device 8, furnace chamber 9 is provided with heating chamber 10 And the smelting chamber 11, the heating chamber 10 bottom communicates with the smelting chamber 11, the melting chamber 11 bottom is provided with a hearth 12, the furnace hearth 12 is provided with a hearth discharge port 13, the heating chamber 10 top is provided with a heating chamber feed port 14, and the heating chamber 10 top A gas outlet 15 in the heating chamber is provided, at least one fire passage 16 is provided around the inner wall of the smelting chamber 11 , and a plurality of air intake channels 17 are arranged on the side wall of the fire passage 16 , and the air intake passages 17 communicate with the fire passage 16 .
[0027] The inner cavity of the furnace chamber 9...
PUM
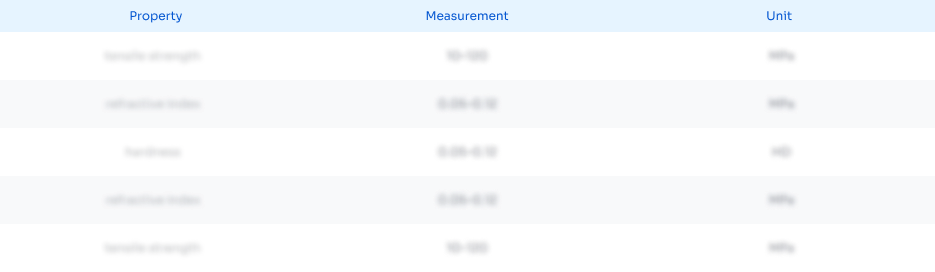
Abstract
Description
Claims
Application Information

- Generate Ideas
- Intellectual Property
- Life Sciences
- Materials
- Tech Scout
- Unparalleled Data Quality
- Higher Quality Content
- 60% Fewer Hallucinations
Browse by: Latest US Patents, China's latest patents, Technical Efficacy Thesaurus, Application Domain, Technology Topic, Popular Technical Reports.
© 2025 PatSnap. All rights reserved.Legal|Privacy policy|Modern Slavery Act Transparency Statement|Sitemap|About US| Contact US: help@patsnap.com