Improved soda lime sintering method for processing aluminum-containing raw material
A technology of soda lime and sintering method, which is applied in the direction of alumina/hydroxide, etc., can solve the problems of large consumption of limestone, large utilization of tailings, high sintering temperature, etc., and achieve high resource utilization efficiency, reduction of tailings, and high sintering temperature low effect
- Summary
- Abstract
- Description
- Claims
- Application Information
AI Technical Summary
Problems solved by technology
Method used
Image
Examples
Embodiment 1
[0025] Aluminum-containing raw material 1: Potassium-rich rock filter residue, the chemical composition is as follows (%):
[0026]
[0027] Among them, the A / S of potassium-rich rock potassium extraction filter residue is 0.75. Accurately take by weighing 1000g nepheline syenite potassium extraction filter residue, 665.3g industrial soda ash (purity is 99%) and 554.7g limestone (purity is 98%), mix and ball mill 1h in experimental ball mill, obtain raw meal powder; The raw material powder is filled in an alumina crucible, and placed in an experimental electric furnace at a constant temperature of 1050 ° C for 2 hours. After the reaction, the clinker is cooled to room temperature with the furnace; the sintered clinker is crushed into a sintered clinker powder, which is required to pass 120 mesh standard sieve; experimentally measured Al in sintered clinker 2 o 3 The standard dissolution rate is 95.2%.
Embodiment 2
[0029] Aluminum-containing raw material 2: Potassium feldspar desiliconization filter cake, the chemical composition is as follows (%):
[0030]
[0031] Among them, the A / S of the potassium feldspar desiliconization filter cake is 0.70. Accurately weigh 1000g potassium feldspar desiliconization filter cake, 733.1g industrial soda ash (purity is 99%) and 572.3g limestone (purity is 98%), mix and ball mill 1h in experimental ball mill, obtain raw meal powder; The raw material powder is filled in an alumina crucible, and placed in an experimental electric furnace at a constant temperature of 1150 ° C for 2 hours. After the reaction, the clinker is cooled to room temperature with the furnace; Mesh standard sieve; experimentally measured Al in sintered clinker 2 o 3 The standard dissolution rate is 96.8%.
Embodiment 3
[0033] Aluminum-containing raw material 3: desiliconized fly ash, the chemical composition is as follows (%):
[0034]
[0035]Among them, the A / S of desiliconized fly ash is 1.68. Accurately weigh 1000g of desiliconized fly ash, 1162.0g of industrial soda ash (purity is 99%) and 571.2g of limestone (purity is 98%), and mix ball milling in experimental ball mill for 1h to obtain raw meal powder; The body is filled in an alumina crucible, and placed in an experimental electric furnace at a constant temperature of 1000 ° C for 2 hours. After the reaction, the clinker is cooled to room temperature with the furnace; sieve; experimentally measured Al in sintered clinker 2 o 3 The standard dissolution rate is 93.7%.
PUM
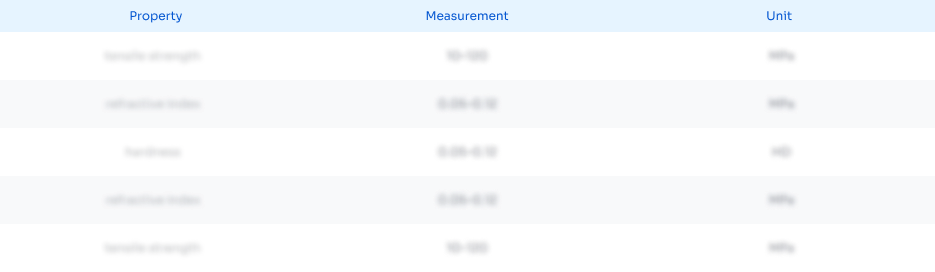
Abstract
Description
Claims
Application Information

- R&D Engineer
- R&D Manager
- IP Professional
- Industry Leading Data Capabilities
- Powerful AI technology
- Patent DNA Extraction
Browse by: Latest US Patents, China's latest patents, Technical Efficacy Thesaurus, Application Domain, Technology Topic, Popular Technical Reports.
© 2024 PatSnap. All rights reserved.Legal|Privacy policy|Modern Slavery Act Transparency Statement|Sitemap|About US| Contact US: help@patsnap.com