Heat-resisting high-dielectric constant inorganic/polymer composite film
A high dielectric constant and composite thin film technology, applied in the field of composite materials, can solve the problems of drastic changes, difficulty in controlling the amount of addition and dielectric constant, etc., and achieve the effect of overcoming drastic changes and excellent dielectric properties
- Summary
- Abstract
- Description
- Claims
- Application Information
AI Technical Summary
Problems solved by technology
Method used
Image
Examples
Embodiment 1
[0018] 1) Add 0.4063g of CCTO powder, 0.5006g of ODA and 10ml of DMAC into a three-necked flask, ultrasonicate for 10min, stir to disperse evenly, and add PMDA to the system in 3 times (the total amount is 0.5507g, and the time interval of addition is 10min ), reacted for 3h to obtain a mixed solution of calcium copper titanate / polyamic acid;
[0019] 2) After spreading the mixed solution of calcium copper titanate / polyamic acid on a glass plate, let it stand in vacuum for 25 minutes, then place it in a blast oven, and heat it at 80°C, 120°C, 180°C, 240°C, and 300°C in sequence. ℃ for 1 h to imidize, to obtain a composite film with a volume fraction of CCTO of 10 vol%.
Embodiment 2
[0021] 1) Add 0.9142g of CCTO powder, 0.5006g of ODA and 10ml of DMAC into a three-necked flask, ultrasonicate for 15min, stir to make it evenly dispersed, and add PMDA to the system in 3 times (the total amount is 0.5507g, and the time interval of addition is 10min ), reacted for 3h to obtain a mixed solution of calcium copper titanate / polyamic acid;
[0022] 2) After spreading the mixed solution of calcium copper titanate / polyamic acid on a glass plate, let it stand in vacuum for 20 minutes, and then place it in a blast oven, and heat it at 80°C, 120°C, 180°C, 240°C, and 300°C in sequence. °C for 1 h for imidization, to obtain a composite film with a volume fraction of CCTO of 20 vol%.
Embodiment 3
[0024] 1) Add 1.5673g of CCTO powder, 0.5006g of ODA and 10ml of DMAC into a three-necked flask, ultrasonicate for 15min, stir to make it evenly dispersed, and add PMDA to the system in 3 times (the total amount is 0.5507g, and the time interval of addition is 10min), reacted 3h, obtained the mixed solution of calcium copper titanate / polyamic acid;
[0025] 2) After spreading the mixed solution of calcium copper titanate / polyamic acid on a glass plate, let it stand in vacuum for 20 minutes, and then place it in a blast oven, and heat it at 80°C, 120°C, 180°C, 240°C, and 300°C in sequence. °C for 1 h for imidization, to obtain a composite film with a volume fraction of CCTO of 30 vol%.
PUM
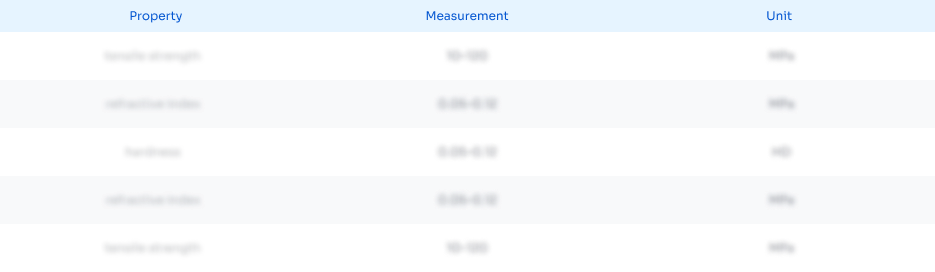
Abstract
Description
Claims
Application Information

- R&D
- Intellectual Property
- Life Sciences
- Materials
- Tech Scout
- Unparalleled Data Quality
- Higher Quality Content
- 60% Fewer Hallucinations
Browse by: Latest US Patents, China's latest patents, Technical Efficacy Thesaurus, Application Domain, Technology Topic, Popular Technical Reports.
© 2025 PatSnap. All rights reserved.Legal|Privacy policy|Modern Slavery Act Transparency Statement|Sitemap|About US| Contact US: help@patsnap.com