Method for high-value and non-waste utilization of cyanidation slag
A technology of high-value cyanidation tailings, applied in the direction of solid waste removal, etc., can solve the problem of not considering emission reduction and other problems, and achieve the effect of high product technical indicators and no waste discharge.
- Summary
- Abstract
- Description
- Claims
- Application Information
AI Technical Summary
Problems solved by technology
Method used
Image
Examples
Embodiment 1
[0039] The chemical composition of a gold mine cyanide tailings filter cake is as follows:
[0040] Table 1. Element content (%) of a gold mine cyanide tailings filter cake
[0041] the element
S
Fe
Cu
Zn
Pb
As
content
28.26
25.36
0.14
0.15
0.21
0.011
[0042] (1) Add water to the fine-grained refractory high-pollution cyanide tailings through the Cu, Zn, Pb multi-element recovery process and stir in the stirring tank for 10min, the pulp concentration is 30%, add 6wt% dilute sulfuric acid in the pulp and stir for 2min, adjust pH = 5, form A pulp, add 10wt% functional composite sol 500g / tt to A pulp and stir for 2min to form B pulp, first add 240g / t butyl xanthate to B pulp and stir for 2min, then add pinitol oil 20g / t and stirred for 2 minutes to form C pulp, fill the C pulp with air from the bottom of the stirring tank and continue to stir for 1 minute, conduct a rough separation for 10 minu...
Embodiment 2
[0056] The chemical composition of a gold mine cyanide tailings filter cake is as follows:
[0057] Table 3. Element content (%) of a gold mine cyanide tailings filter cake
[0058] the element
S
Fe
Cu
Zn
Pb
As
content
28.26
25.36
0.14
0.15
0.21
0.011
[0059] (1) Add water to the fine-grained refractory high-pollution cyanide tailings through Cu, Zn, Pb multi-element recovery process and stir in the stirring tank for 15min, the pulp concentration is 33%, add 6wt% dilute sulfuric acid in the pulp and stir for 6min, adjust pH = 6, form A pulp, add 10wt% functional composite sol 750g / t to A pulp and stir for 6 minutes to form B pulp, first add butyl xanthate 360g / t to B pulp and stir for 6 minutes, then add pinitol oil 40g / t and stirred for 6min to form C pulp, fill the C pulp with air from the bottom of the stirring tank and continue stirring for 1min, conduct a rough separation for 15min, scr...
Embodiment 3
[0073] The chemical composition of a gold mine cyanide tailings filter cake is as follows:
[0074] Table 5. Element content (%) of a gold mine cyanide tailings filter cake
[0075] the element
S
Fe
Cu
Zn
Pb
As
content
28.26
25.36
0.14
0.15
0.21
0.011
[0076] (1) Add water to the fine-grained refractory high-pollution cyanide tailings through Cu, Zn, Pb multi-element recovery process and stir in the stirring tank for 20min, the pulp concentration is 35%, add 6wt% dilute sulfuric acid in the pulp and stir for 10min, adjust pH=7, form A pulp, add 10wt% functional composite sol 1000g / t to A pulp and stir for 10min to form B pulp, first add 480g / t butyl xanthate to B pulp and stir for 10min, then add pinitol oil 60g / t and stirred for 10 minutes to form C pulp, fill the C pulp with air from the bottom of the stirring tank and continue to stir for 2 minutes, conduct a rough separation for 20 minut...
PUM
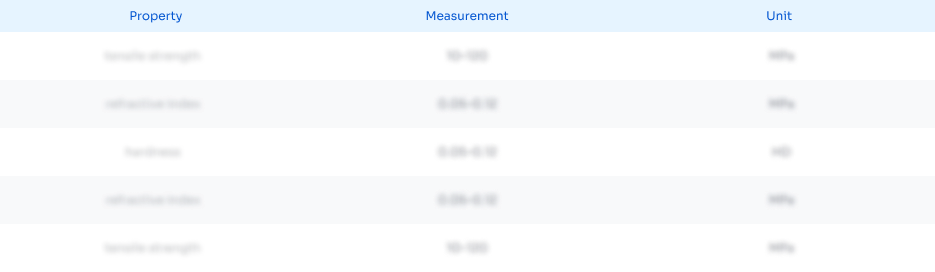
Abstract
Description
Claims
Application Information

- R&D Engineer
- R&D Manager
- IP Professional
- Industry Leading Data Capabilities
- Powerful AI technology
- Patent DNA Extraction
Browse by: Latest US Patents, China's latest patents, Technical Efficacy Thesaurus, Application Domain, Technology Topic, Popular Technical Reports.
© 2024 PatSnap. All rights reserved.Legal|Privacy policy|Modern Slavery Act Transparency Statement|Sitemap|About US| Contact US: help@patsnap.com