Novel planetary tube rolling mill and planetary rolling method for copper alloy tubes
A planetary pipe mill and copper alloy technology, applied in metal rolling, metal rolling, manufacturing tools, etc., can solve the problems affecting the machinability and pipe performance of the drawing process, the decrease of heat transfer performance, the deformation resistance at room temperature, and the processing Hardening and deformation stress increase, etc., to achieve excellent internal and external structure and surface quality, bright internal and external surfaces, and eliminate over-burning cracking effects
- Summary
- Abstract
- Description
- Claims
- Application Information
AI Technical Summary
Problems solved by technology
Method used
Image
Examples
Embodiment Construction
[0034] like figure 1 As shown, the present invention first proposes a novel planetary pipe rolling mill, which includes a feeding mechanism for conveying hollow billets, a planetary host 1 for casting and rolling hollow billets, and a roll group 11 and Rolling mold rapid cooling mechanism, an induction preheating mechanism 2 for preheating the hollow cast slab is provided between the discharge end of the feeding mechanism and the feed end of the planetary main machine 1, and the discharge end of the planetary main machine 1 is sequentially An induction soaking mechanism 3 and a slow cooling mechanism 4 are provided, and the rolled and rapidly cooled pipe is reheated by the induction soaking mechanism 3 and slowly cooled by the slow cooling mechanism 4 .
[0035] refer to figure 2 , image 3 , the induction preheating mechanism 2 is a closed whole formed by connecting four independent induction heaters 21 through supporting rollers 23, and the induction heater 21 is provided...
PUM
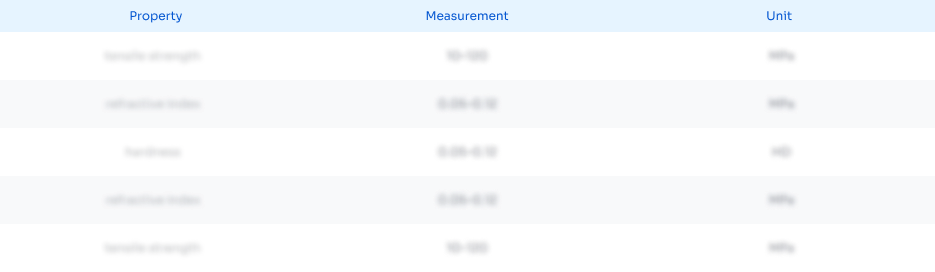
Abstract
Description
Claims
Application Information

- R&D
- Intellectual Property
- Life Sciences
- Materials
- Tech Scout
- Unparalleled Data Quality
- Higher Quality Content
- 60% Fewer Hallucinations
Browse by: Latest US Patents, China's latest patents, Technical Efficacy Thesaurus, Application Domain, Technology Topic, Popular Technical Reports.
© 2025 PatSnap. All rights reserved.Legal|Privacy policy|Modern Slavery Act Transparency Statement|Sitemap|About US| Contact US: help@patsnap.com