Method for producing electrolytic nickel by leaching chemically precipitated nickel sulfide with pure oxygen
A technology of chemical precipitation and nickel sulfide, applied in optics, improvement of process efficiency, photographic technology, etc., can solve problems such as unsuitable treatment of chemical composition nickel sulfide, equipment corrosion suitable for resource range, high operating cost, etc., and reach the scope of mineral resource utilization wide, small investment, low production cost effect
- Summary
- Abstract
- Description
- Claims
- Application Information
AI Technical Summary
Problems solved by technology
Method used
Image
Examples
Embodiment 1
[0032] A. At 30m 3 Add 20m 3 The second-stage high-pressure leaching filtrate, put in 2 tons of nickel sulfide, add sulfuric acid solution, control the concentration of sulfuric acid to 0.2mol / L, and stir and slurry for 30 minutes.
[0033] B. Transport the pulped material to the first stage of atmospheric pressure leaching tank for a stage of oxygen atmospheric pressure leaching, adjust with nickel carbonate and keep the pH value to 4.5, heat to 70 ° C, and the oxygen flow rate per hour is 20m 3 (Oxygen 1m per hour per square solution 3 ), oxygen purity ≥ 95%, and after stirring for 2 hours, filter to obtain a filter residue and filtrate. The filtrate is oxidized and neutralized with an oxidant to remove cobalt and then filtered to obtain cobalt removal slag and cobalt removal filtrate. Cobalt removal slag discharge system, cobalt removal filtrate electrolysis, Electrolytic nickel and anolyte are obtained, a part of the anolyte is added with sodium carbonate to precipitate ...
Embodiment 2
[0037] A. At 30m 3 Add 16m into the stirring tank 3 The second-stage high-pressure leaching filtrate, put in 2 tons of nickel sulfide, add sulfuric acid solution, control the concentration of sulfuric acid to 0.3mol / L, and stir and slurry for 30 minutes.
[0038] B. Transport the pulped material to the first stage of atmospheric pressure leaching tank for a stage of oxygen atmospheric pressure leaching, adjust with nickel carbonate and keep the pH value to 5.0, heat to 80 °C, and the oxygen flow rate per hour is 32m 3 (Oxygen 2m per hour per square solution 3 ), oxygen purity ≥ 95%, filtered after stirring for 3 hours to obtain a filter residue and filtrate, the filtrate was oxidized and neutralized with an oxidant to remove cobalt and then filtered to obtain cobalt-removed residue and cobalt-removed filtrate, cobalt-removed residue was discharged from the system, and cobalt-removed filtrate was electrolyzed , to obtain electrolytic nickel and anolyte, a part of the anolyte ...
Embodiment 3
[0042] A. At 30m 3 Add 18m into the stirring tank 3 The second-stage high-pressure leaching filtrate, put in 2 tons of nickel sulfide, add sulfuric acid solution, control the concentration of sulfuric acid to 0.25mol / L, and stir and slurry for 30 minutes.
[0043] B. Transport the pulped material to the first stage of atmospheric pressure leaching tank for a stage of oxygen atmospheric pressure leaching, adjust and maintain the pH value to 4.8 with nickel carbonate, heat to 75°C, and the oxygen flow rate per hour is 27m 3 (Oxygen 1.5m per hour per square solution 3), oxygen purity ≥ 95%, stirring for 2.5 hours and filtering to obtain a filter residue and filtrate, the filtrate is oxidized and neutralized with an oxidant to remove cobalt and then filtered to obtain cobalt removal residue and cobalt removal filtrate, cobalt removal residue discharge system, cobalt removal filtrate electrolysis, Electrolytic nickel and anolyte are obtained, a part of the anolyte is added with s...
PUM
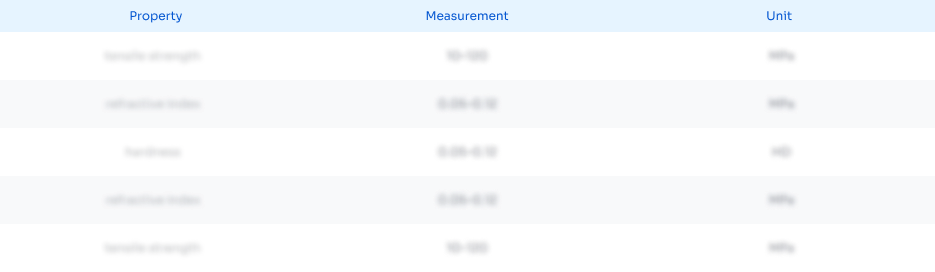
Abstract
Description
Claims
Application Information

- R&D
- Intellectual Property
- Life Sciences
- Materials
- Tech Scout
- Unparalleled Data Quality
- Higher Quality Content
- 60% Fewer Hallucinations
Browse by: Latest US Patents, China's latest patents, Technical Efficacy Thesaurus, Application Domain, Technology Topic, Popular Technical Reports.
© 2025 PatSnap. All rights reserved.Legal|Privacy policy|Modern Slavery Act Transparency Statement|Sitemap|About US| Contact US: help@patsnap.com