A kind of preparation method of directionally solidified high niobium titanium aluminum base alloy
A technology of directional solidification and high-niobium titanium-aluminum, applied in the field of metal material preparation, can solve problems such as directional solidification of titanium-aluminum-based alloys with high niobium content that have not been studied before, achieve universal applicability and promotion value, reduce impurity content, and simple equipment Effect
- Summary
- Abstract
- Description
- Claims
- Application Information
AI Technical Summary
Problems solved by technology
Method used
Image
Examples
Embodiment 1
[0030] Grind the surface of a cylindrical (Φ6×100mm) master alloy rod sample with a composition of 45Ti-45Al-9Nb-0.5W-0.25B-0.25Y (atomic percentage) to remove the oxide layer and impurities on the surface, and then put it into the coating In a high-purity alumina crucible with a size of Φ6×120 mm after the layer, the volume percentage of the coating composition is: 90% yttrium oxide + 3% sodium phosphate + 7% bentonite. Place the crucible upright on the base of the drawing rod in the melting and directional solidification system in the improved area, close the vacuum chamber and evacuate to 3×10 -3 After Pa, fill in high-purity argon to 380Pa; turn on the power, heat the alloy to 1950K at a heating rate of 18K / min and keep it warm for 15 minutes to ensure that the melt is fully melted and heated evenly; set the orientation in the PLC control panel The solidification speed is 100μm / s, keep the power supply constant and start pulling; after the sample is stretched 100mm, turn o...
Embodiment 2
[0032] Grind the surface of a cylindrical (Φ10×100mm) master alloy rod sample with a composition of 44.5Ti-46Al-8.5Nb-0.5Mn-0.25B-0.25Y (atomic percentage) to remove the oxide layer and impurities on the surface, and then install After being put into a high-purity alumina crucible with a size of Φ10×120 mm after coating, the volume percentage of the coating composition is: 87% yttrium oxide+3% sodium phosphate+10% bentonite. Place the crucible upright on the base of the drawing rod in the melting and directional solidification system in the improved area, close the vacuum chamber and evacuate to 3×10 -3 After Pa, refill high-purity argon to 380Pa; turn on the power, heat the alloy to 2410K at a heating rate of 18K / min and keep it warm for 15 minutes to ensure that the melt is fully melted and heated evenly; set the orientation in the PLC control panel The solidification speed is 2μm / s, keep the power supply constant and start pulling; after the sample is stretched 100mm, turn ...
Embodiment 3
[0034] A single crystal sample with a seed crystal of 54Ti-43Al-3Si (atomic percentage) was wire-cut into a rod with a cross-sectional diameter of Φ20 mm and a height of 20 mm as a seed crystal, which was welded to a 48.9Ti-45Al- The bottom end of a 6Nb-0.1B (atomic percent) cylinder (Φ20×100mm) master alloy rod-shaped sample. After the assembly is completed, the surface is polished to remove the oxide layer and impurities on the surface, and then coated with a size of Φ20 In a high-purity alumina crucible of ×120 mm, the volume percentage of the coating composition is: 92% yttrium oxide+2% sodium phosphate+6% bentonite. Place the crucible upright on the base of the drawing rod in the melting and directional solidification system in the improved area, adjust the position of the initial drawing rod so that the welding part of the seed crystal enters 5mm above the same level as the bottom of the graphite sleeve, close the vacuum chamber and evacuate to 3 ×10 -3 Pa, and then fil...
PUM
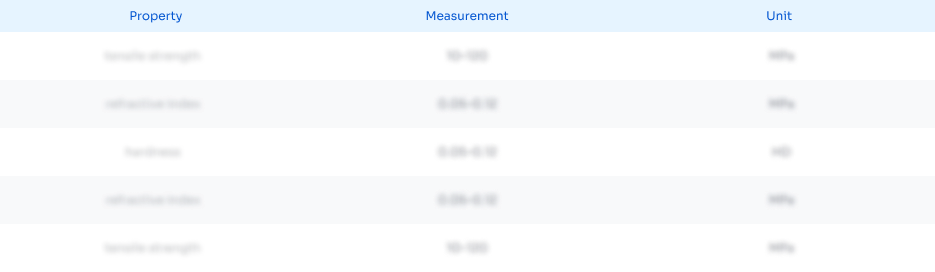
Abstract
Description
Claims
Application Information

- Generate Ideas
- Intellectual Property
- Life Sciences
- Materials
- Tech Scout
- Unparalleled Data Quality
- Higher Quality Content
- 60% Fewer Hallucinations
Browse by: Latest US Patents, China's latest patents, Technical Efficacy Thesaurus, Application Domain, Technology Topic, Popular Technical Reports.
© 2025 PatSnap. All rights reserved.Legal|Privacy policy|Modern Slavery Act Transparency Statement|Sitemap|About US| Contact US: help@patsnap.com