Preparation method of directional solidification high-niobium TiAl-base alloy
A technology of directional solidification and high-niobium titanium-aluminum, which is applied in the field of metal material preparation, can solve problems such as directional solidification of titanium-aluminum-based alloys with high niobium content that have not been studied before, achieve universal applicability and promotion value, improve room temperature performance, and reduce impurities The effect of content
- Summary
- Abstract
- Description
- Claims
- Application Information
AI Technical Summary
Problems solved by technology
Method used
Image
Examples
Embodiment 1
[0030] Grind the surface of the cylindrical (Φ6×100mm) master alloy rod-shaped sample with the composition of 45Ti-45Al-9Nb-0.5W-0.25B-0.25Y (atomic percentage) to remove the oxide layer and impurities on the surface, and then load the coating In a high-purity alumina crucible with a post-layer size of Φ6×120mm, the volume percentage of the coating composition is: 90% yttrium oxide + 3% sodium phosphate + 7% bentonite. Place the crucible firmly on the base of the drawing rod in the directional solidification system of the improved zone, close the vacuum chamber and evacuate to 3×10 -3 After Pa, fill with high-purity argon gas to 380Pa; turn on the power, heat the alloy to 1950K at a heating rate of 18K / min and keep it for 15 minutes to ensure that the melt is fully melted and heated evenly; set the orientation in the PLC control panel The solidification speed is 100μm / s, keep the power of the power constant and start pulling; after the sample is stretched for 100mm, turn off the...
Embodiment 2
[0032] Grind the surface of a cylindrical (Φ10×100mm) master alloy rod sample with a composition of 44.5Ti-46Al-8.5Nb-0.5Mn-0.25B-0.25Y (atomic percentage) to remove the oxide layer and impurities on the surface, and then install it In the high-purity alumina crucible with a size of Φ10×120mm after being coated, the volume percentage of the coating composition is: 87% yttrium oxide + 3% sodium phosphate + 10% bentonite. Place the crucible firmly on the base of the drawing rod in the directional solidification system of the improved zone, close the vacuum chamber and evacuate to 3×10 -3 After Pa, fill with high-purity argon to 380Pa; turn on the power, heat the alloy to 2410K at a heating rate of 18K / min and keep it for 15 minutes to ensure that the melt is fully melted and heated evenly; set the orientation in the PLC control panel The solidification speed is 2μm / s, keep the power of the power constant and start pulling; after the sample is stretched for 100mm, turn off the powe...
Embodiment 3
[0034] Cut a single crystal sample with a seed crystal of 54Ti-43Al-3Si (atomic percentage) into a rod shape with a cross-sectional diameter of Φ20mm and a height of 20mm as the seed crystal, and weld it to a composition of 48.9Ti-45Al- by argon arc welding. The bottom end of the 6Nb-0.1B (atomic percentage) cylinder (Φ20×100mm) master alloy rod sample. After the assembly is completed, the surface is polished to remove the oxide layer and impurities on the surface, and then the size of the coating is Φ20 In the high-purity alumina crucible of ×120mm, the volume percentage of the coating composition is: 92% yttrium oxide + 2% sodium phosphate + 6% bentonite. Place the crucible firmly on the drawing rod base in the improved zone melting directional solidification system, adjust the initial drawing rod position so that the seed crystal welding point enters 5mm above the same horizontal position at the bottom of the graphite sleeve, close the vacuum chamber and evacuate to 3 ×10 -3...
PUM
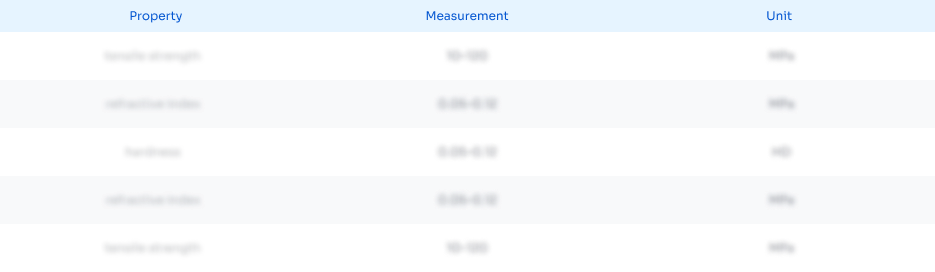
Abstract
Description
Claims
Application Information

- R&D
- Intellectual Property
- Life Sciences
- Materials
- Tech Scout
- Unparalleled Data Quality
- Higher Quality Content
- 60% Fewer Hallucinations
Browse by: Latest US Patents, China's latest patents, Technical Efficacy Thesaurus, Application Domain, Technology Topic, Popular Technical Reports.
© 2025 PatSnap. All rights reserved.Legal|Privacy policy|Modern Slavery Act Transparency Statement|Sitemap|About US| Contact US: help@patsnap.com