Preparation method of high-purity halogenated hydrocarbon used for liquid chromatogram
A technology of liquid chromatography and pure halogenated hydrocarbons, which is applied in the field of preparation of high-purity halogenated hydrocarbons for liquid chromatography, to achieve the effects of reducing costs, reducing process steps, and easy recovery
- Summary
- Abstract
- Description
- Claims
- Application Information
AI Technical Summary
Problems solved by technology
Method used
Examples
Embodiment 1
[0027] 5 kg of industrial grade dichloromethane through preliminary rectification was added to the reaction distillation still, and 0.25 kg of 5% sulfuric acid aqueous solution was added at the same time, the temperature of the reaction kettle was 25° C., and the reaction was carried out for 2 hours. Start extraction and rectification, and after 1 hour of total reflux, start to extract the overhead fraction. After the top product is separated by liquid phase, all the water phase is refluxed, and the oil phase is partially refluxed. The total reflux ratio is 7. Extract the fraction below 37.8°C and put it back into the raw material storage tank, extract 4.86 kg of the fraction at 37.8-38.4°C, pass through the drier equipped with 3A molecular sieve at a space velocity of 1 / hour, and obtain 4.48 kg of product dichloromethane, which enters the second extraction Distillation tower. Add 0.224 kilograms of toluene in the second extractive distillation column, and after full reflux fo...
Embodiment 2
[0029]5.0 kg of industrial grade chloroform through preliminary rectification was added to the reactive distillation still, and 1.5 kg of 1% sulfuric acid aqueous solution was added simultaneously, and the temperature of the reaction still was 25° C., and reacted for 2 hours. Start extraction and rectification, and after 1 hour of total reflux, start to extract the overhead fraction. After the top product is separated by liquid phase, all the water phase is refluxed, and the oil phase is partially refluxed. The total reflux ratio is 2. Extract the fraction below 57.8°C and put it back into the raw material storage tank, extract 4.87 kg of the fraction at 57.8-56.4°C, pass through the drier equipped with 3A molecular sieve at a space velocity of 2 / hour, and obtain 4.43 kg of product chloroform, which enters the second extractive distillation tower. The second tower adds 0.443 kilograms of toluene, and after full reflux for 1 hour, the overhead fraction begins to be extracted. A...
Embodiment 3
[0031] Add 5.0 kilograms of industrial grade carbon tetrachloride through preliminary rectification to the reaction distillation kettle, add 0.10 kilograms of 15% sulfuric acid aqueous solution simultaneously, the reaction kettle temperature is 25 ℃, reacts 2 hours. Start extraction and rectification, and after 1 hour of total reflux, start to extract the overhead fraction. After the top product is separated by liquid phase, all the water phase is refluxed, and the oil phase is partially refluxed. The total reflux ratio is 5. Extract 4.79 kg of 65.7~66.3°C distillate, pass through the drier equipped with 4A molecular sieve at a space velocity of 1 / hour to obtain 4.39 kg of product carbon tetrachloride, and enter the second extractive distillation tower. Add 2.40 kilograms of toluene to the second tower, after full reflux for 1 hour, begin to extract the overhead fraction. The distillate below 76.4°C from the top of the tower is put back into the raw material storage tank, 4.18...
PUM
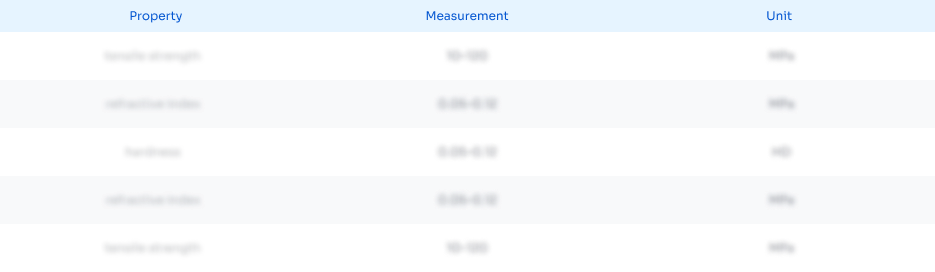
Abstract
Description
Claims
Application Information

- R&D
- Intellectual Property
- Life Sciences
- Materials
- Tech Scout
- Unparalleled Data Quality
- Higher Quality Content
- 60% Fewer Hallucinations
Browse by: Latest US Patents, China's latest patents, Technical Efficacy Thesaurus, Application Domain, Technology Topic, Popular Technical Reports.
© 2025 PatSnap. All rights reserved.Legal|Privacy policy|Modern Slavery Act Transparency Statement|Sitemap|About US| Contact US: help@patsnap.com