Aluminum alloy cyanide-free and nickel-free electroplating method and electroplating products thereof
An aluminum alloy and nickel electroplating technology, applied in the plating of superimposed layers, metal material coating process, transportation and packaging, etc., can solve the problems of pollution, poor adhesion, and many pitting, and reduce allergies and adhesion. High, the effect of high corrosion resistance of the coating
- Summary
- Abstract
- Description
- Claims
- Application Information
AI Technical Summary
Problems solved by technology
Method used
Examples
Embodiment 1
[0029] The base material is AC8A aluminum alloy material, the specific operation steps are as follows:
[0030] 1. Mechanical polishing
[0031] Pretreatment of aluminum alloy materials: according to the requirements, mechanically polish the samples. Generally, the polishing method is carried out with a button cloth wheel combined with a small wool wheel to remove the burrs and scales produced by the raw material itself during the die-casting process, reduce the surface roughness, and improve the quality of the surface. Mirror bright effect and enhanced subsequent treatment or electroplating after sandblasting.
[0032] 2. Ultrasonic wax removal
[0033] Use Procleaner BR1 model wax removal water from Yongxing Chemical Company, the concentration of the tank is 30ml / L; the temperature is 65°C, and the time is 5min.
[0034] 3. Cathodic electrolytic degreasing
[0035] Use the 630 type electrolytic degreasing powder of International Chemical Co., Ltd., the opening volume is 5...
Embodiment 2
[0058] The base material is YL177 aluminum alloy material, the specific operation steps are as follows:
[0059] Steps 1-6 are the same as in Example 1.
[0060] 7. Galvanizing
[0061] The zinc dipping solution is: zinc oxide 40g / l, sodium hydroxide 125g / l, potassium sodium tartrate 50g / l, ferric chloride 1.5g / l, sodium nitrite 2g / l, dipping at a temperature of 23°C Zinc 45s.
[0062] 8. Plating cyanide-free alkali copper
[0063] The CuMac Strike XD7453 plating solution used by MacDermid is CuMac Strike Makeup solution 150ml / l, Equivalent copper meta 5.5g / l, CuMac Strike Stabilizer 65ml / l, and CuMac Strike Buffer 50ml / l. At a temperature of 60°C, the cathode current density is 1A / dm 2 , cyanide-free alkali copper electroplating for 2 minutes under the condition of pH value 9.5.
[0064] 9. Acid copper plating
[0065] Using Atotech's Ultra acid copper plating solution, the plating solution is: CuSO 4 .5H 2 O 220g / L, H 2 SO 4 50g / L, chloride ion 100mg / L, tank opener...
Embodiment 3
[0096] The base material is ZL102 aluminum alloy material, and the specific operation steps are as follows:
[0097] Steps 1-6 are the same as in Example 1.
[0098] 7. Galvanizing
[0099] The zinc dipping solution is: zinc oxide 60g / l, sodium hydroxide 130g / l, potassium sodium tartrate 60g / l, ferric chloride 1.5g / l, sodium nitrite 3.5g / l, at a temperature of 20°C Dip zinc for 2min.
[0100] 8. Plating cyanide-free alkali copper
[0101] The CuMac Strike XD7453 plating solution used by MacDermid is CuMac Strike Makeup solution 200ml / l, Equivalent copper meta 7.5g / l, CuMac Strike Stabilizer70ml / l, CuMac Strike Buffer80ml / l. At a temperature of 35°C, the cathode current density is 1A / dm 2 , cyanide-free alkali copper electroplating for 5 minutes under the condition of pH value 9.5.
[0102] 9. Acid copper plating
[0103] Using Atotech's Ultra acid copper plating solution, the plating solution is: CuSO 4 .5H 2 O 225g / L, H 2 SO 4 55g / L, chloride ion 100mg / L, tank opene...
PUM
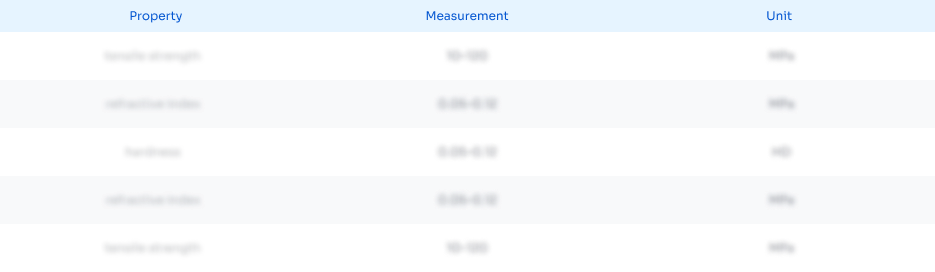
Abstract
Description
Claims
Application Information

- R&D Engineer
- R&D Manager
- IP Professional
- Industry Leading Data Capabilities
- Powerful AI technology
- Patent DNA Extraction
Browse by: Latest US Patents, China's latest patents, Technical Efficacy Thesaurus, Application Domain, Technology Topic, Popular Technical Reports.
© 2024 PatSnap. All rights reserved.Legal|Privacy policy|Modern Slavery Act Transparency Statement|Sitemap|About US| Contact US: help@patsnap.com