Biodegradable film and preparation method thereof
A biodegradable and thin film technology, applied in the field of biodegradable thin films and their preparation, achieves the effects of simple process, easy control and high tensile strength
- Summary
- Abstract
- Description
- Claims
- Application Information
AI Technical Summary
Problems solved by technology
Method used
Examples
Embodiment 1
[0025] (1), take by weighing 40 parts of terephthalic acid, oxalic acid, 1,4 butanediol copolyester, 50 parts of thermoplastic starch, 5.3 parts of nano-scale silicon dioxide after modification, respectively to these three kinds of raw materials Carry out drying and modification treatment;
[0026] (2) Utilize a high-speed mixer to mix the dried p-phthalic acid, oxalic acid, 1,4-butanediol copolyester, thermoplastic starch, and modified nano-scale silicon dioxide to add plasticizer (polyethylene glycol) Diol) 3.9 parts, antioxidant (antioxidant 1010) 0.1 part, lubricant (zinc stearate) 0.6 part and anti-ultraviolet agent (catechol) 0.1 part, fully mix until uniform.
[0027] (3) Add the mixed material to a twin-screw extruder for melt blending, then strand and pelletize to obtain granular mixed resin. The granular mixed resin is dehydrated and dried. The treated granular mixed resin is extruded and blown by single screw to produce terephthalic acid, oxalic acid and 1,4 butan...
Embodiment 2
[0029] (1), take by weighing 50 parts of terephthalic acid, oxalic acid, 1,4 butanediol copolyester, 40 parts of thermoplastic starch, 5.3 parts of nano-scale silicon dioxide after modification, respectively to these three kinds of raw materials Carry out drying and modification treatment;
[0030] (2) Utilize a high-speed mixer to mix the dried p-phthalic acid, oxalic acid, 1,4-butanediol copolyester, thermoplastic starch, and modified nano-scale silicon dioxide to add plasticizer (orthophthalic acid) Dimethyl diformate) 3.9 parts, antioxidant (antioxidant 1076) 0.1 part, lubricant (sodium stearate) 0.6 part and anti-ultraviolet agent (hydroquinone) 0.1 part, fully mix until uniform.
[0031] (3) Add the mixed material to a twin-screw extruder for melt blending, then strand and pelletize to obtain granular mixed resin. The granular mixed resin is dehydrated and dried. The treated granular mixed resin is extruded and blown by single screw to produce terephthalic acid, oxalic...
Embodiment 3
[0033] (1), take by weighing 60 parts of terephthalic acid, oxalic acid, 1,4 butanediol copolyester, 25 parts of thermoplastic starch, 10 parts of nano-scale silicon dioxide after modification, respectively to these three kinds of raw materials Carry out drying and modification treatment;
[0034] (2) Utilize a high-speed mixer to mix the dried p-phthalic acid, oxalic acid, 1,4-butanediol copolyester, thermoplastic starch, and modified nano-scale silicon dioxide to add a plasticizer (acetylated Triethyl citrate) 3.9 parts, antioxidant (antioxidant 1076) 0.1 part, lubricant (mixture of zinc stearate and sodium stearate) 0.9 part and anti-ultraviolet agent (catechol and hydroquinone Diphenol mixture) 0.1 part, fully mixed until uniform.
[0035](3) Add the mixed material to a twin-screw extruder for melt blending, then strand and pelletize to obtain granular mixed resin. The granular mixed resin is dehydrated and dried. The treated granular mixed resin is extruded and blown b...
PUM
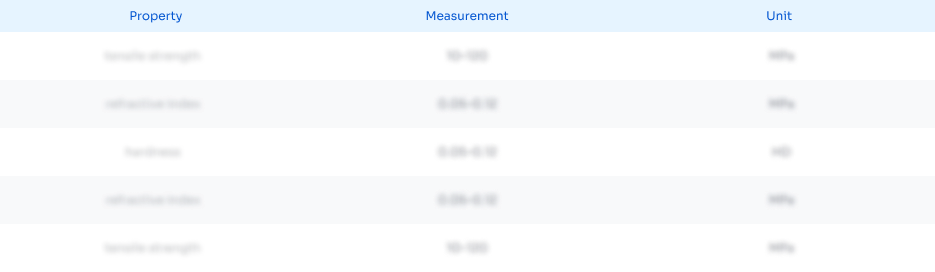
Abstract
Description
Claims
Application Information

- R&D
- Intellectual Property
- Life Sciences
- Materials
- Tech Scout
- Unparalleled Data Quality
- Higher Quality Content
- 60% Fewer Hallucinations
Browse by: Latest US Patents, China's latest patents, Technical Efficacy Thesaurus, Application Domain, Technology Topic, Popular Technical Reports.
© 2025 PatSnap. All rights reserved.Legal|Privacy policy|Modern Slavery Act Transparency Statement|Sitemap|About US| Contact US: help@patsnap.com