Indirect extruding and casting method of wrought aluminum alloy casting
A deformed aluminum alloy, extrusion casting technology, applied in the field of indirect extrusion casting of deformed aluminum alloy castings, to achieve the effects of reduced machining, high mechanical properties, dimensional accuracy and high surface finish
- Summary
- Abstract
- Description
- Claims
- Application Information
AI Technical Summary
Problems solved by technology
Method used
Image
Examples
Embodiment 1
[0026] Alloy formulation:
[0027] The mass percentage of pure aluminum, aluminum-silicon alloy, aluminum-copper alloy, aluminum-chromium alloy, and pure magnesium is: Si: 0.5%, Cu: 0.25%, Mg: 0.9%, Cr: 0.06%, Al: balance preparation;
[0028] Alloy smelting: first heat up pure aluminum and aluminum-silicon, aluminum-copper, and aluminum-chromium master alloys and melt them. When the temperature rises to 700°C, add 0.5% (mass percentage) of the total amount of the alloy to refine the HGJ-1 solid refining agent, and cool down to 680°C. Add magnesium at ℃, adjust the temperature to 720℃ and start indirect extrusion casting; the heating or cooling of molten aluminum is implemented by turning on and cutting off the power supply (the same below).
[0029] Indirect squeeze casting: The process parameters of indirect squeeze casting are: the pressurized pressure is 80MPa, the holding time is 15s, the pouring temperature is 690°C, and the mold temperature is 80°C; it is better to hea...
Embodiment 2
[0033] Alloy formulation:
[0034] Prepare pure aluminum, aluminum-silicon alloy, aluminum-copper alloy, aluminum-chromium alloy, and pure magnesium according to the mass percentage of alloy elements: Si: 0.8%, Cu: 0.5%, Mg: 1.0%, Cr: 0.1%, and Al: the balance ;
[0035] Alloy smelting: first heat up pure aluminum and aluminum-silicon, aluminum-copper, and aluminum-chromium master alloys to melt, when the temperature rises to 710°C, add HGJ-1 solid refining agent with 0.8% (mass percentage) of the total amount of the alloy for refining, and cool down to 690°C Add magnesium, adjust the temperature to 730°C and start indirect extrusion casting;
[0036] Indirect squeeze casting: The process parameters of indirect squeeze casting are: the pressurized pressure is 140MPa, the pressure holding time is 20s, the pouring temperature is 710°C, and the mold temperature is 120°C;
[0037] Heat treatment: solid solution treatment: solid solution temperature and time (515±5)℃×10h, the tra...
Embodiment 3
[0040] Alloy formulation:
[0041] Prepare pure aluminum, aluminum-silicon alloy, aluminum-copper alloy, aluminum-chromium alloy, and pure magnesium according to the mass percentage of alloy elements: Si: 1.15%, Cu: 0.8%, Mg: 1.2%, Cr: 0.3%, and Al: the balance ;
[0042] Alloy smelting: first heat up pure aluminum and aluminum-silicon, aluminum-copper, and aluminum-chromium master alloys to melt, raise the temperature to 720°C, add HGJ-1 solid refining agent with 0.6% (mass percentage) of the total amount of the alloy for refining, cool down to 700°C and add For magnesium, adjust the temperature to 740°C and start indirect extrusion casting;
[0043] Indirect squeeze casting: The process parameters of indirect squeeze casting are: the pressurized pressure is 180MPa, the pressure holding time is 25s, the pouring temperature is 730°C, and the mold temperature is 160°C;
[0044] Heat treatment: solution treatment: solution temperature and time (515±5)℃×8h, transfer time of cas...
PUM
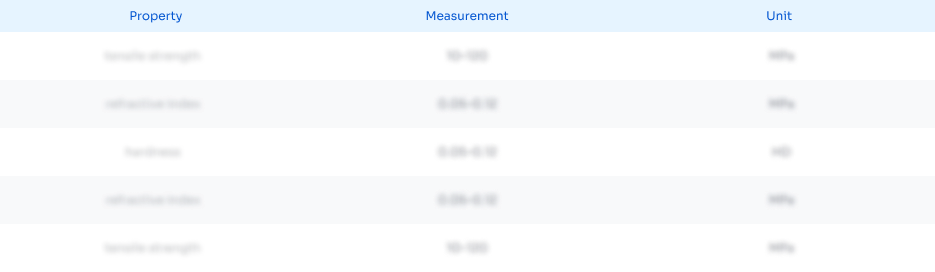
Abstract
Description
Claims
Application Information

- Generate Ideas
- Intellectual Property
- Life Sciences
- Materials
- Tech Scout
- Unparalleled Data Quality
- Higher Quality Content
- 60% Fewer Hallucinations
Browse by: Latest US Patents, China's latest patents, Technical Efficacy Thesaurus, Application Domain, Technology Topic, Popular Technical Reports.
© 2025 PatSnap. All rights reserved.Legal|Privacy policy|Modern Slavery Act Transparency Statement|Sitemap|About US| Contact US: help@patsnap.com